A Design Methodology of New Connecting rod assembly using Analytical and Finite Element Analysis Approach
2019 IEEE Transportation Electrification Conference (ITEC-India)(2019)
摘要
The application of virtual simulation of engine components has become an integral part of design and development process. Virtual simulation offers opportunities to reduce number of physical tests during design verification and validation. The accuracy of virtual simulation is also dependent on applying accurate boundary conditions like material properties and load acting on components. Accurate simulated model helps in achieving considerable reduction in development time and cost.This paper explains a design methodology of connecting rod assembly for new engine family having shorter stroke. The adopted methodology simulates major loading conditions for Compressive, tensile stresses & fatigue life of connecting rod. Finite element analysis was done to calculate static displacement, strain and stresses under maximum compressive and tensile loading which were then used for critical point evaluation. Fatigue analysis and longevity is assessed through ANSYS. To validate the methodology developed; accelerated physical fatigue testing was carried out on the rig and results were compared. A very close correlation could be established between FEM results and failure point on physical test samples. The strain values predicted through simulation is within 10% of error with measured strain values. This calibrated model helped us to set appropriate design factor of safety for such applications.
更多查看译文
关键词
finite element analysis,virtual simulation,engine components,design verification,tensile loading,accelerated physical fatigue testing,connecting rod assembly,compressive stress,tensile stress,fatigue life
AI 理解论文
溯源树
样例
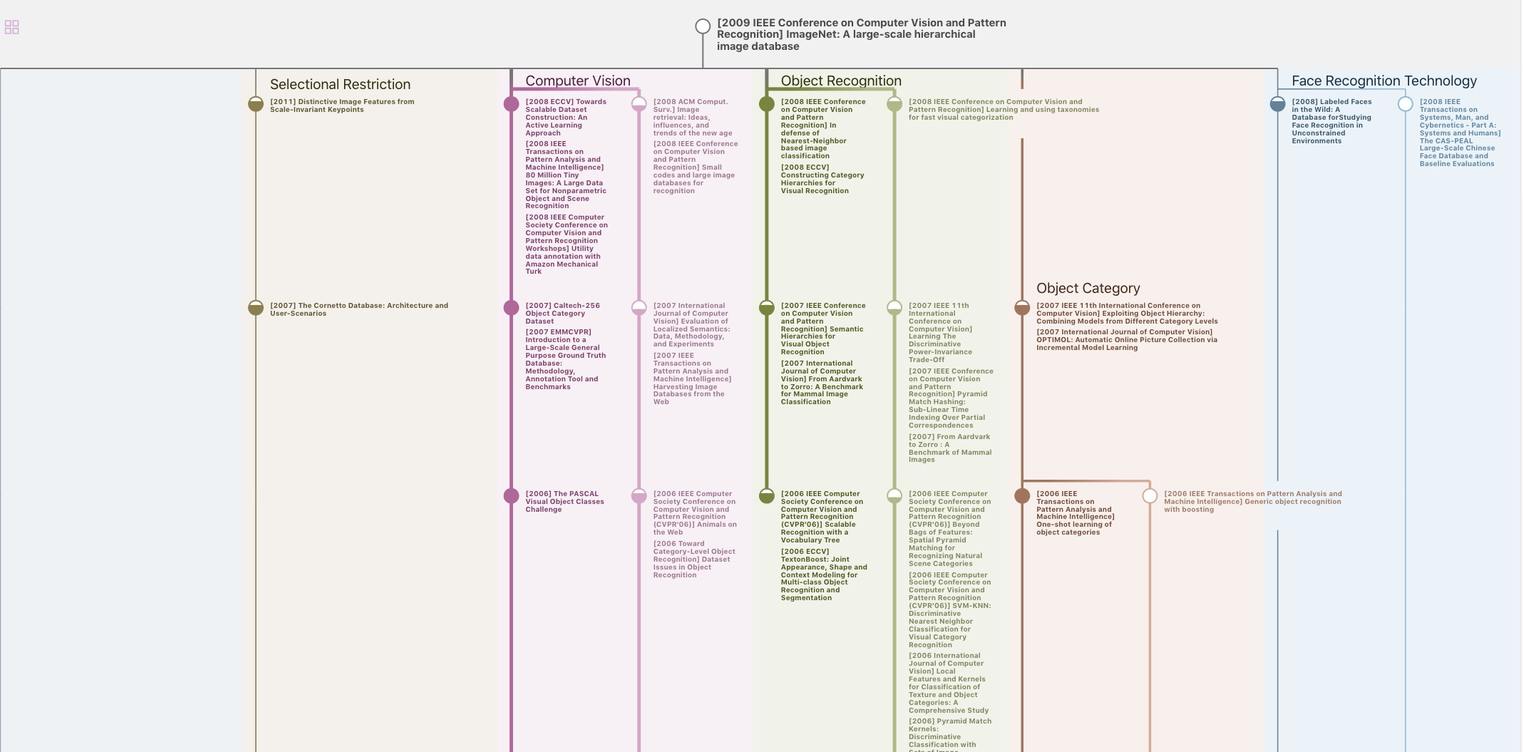
生成溯源树,研究论文发展脉络
Chat Paper
正在生成论文摘要