Microstructure Evolution and Recrystallization Mechanisms of High Mg Alloyed Al-Mg Alloy during Friction Stir Welding with Different Cooling Media
Journal of Materials Engineering and Performance(2022)
Abstract
Heat input in friction stir welding (FSW) plays a vital role in determining the microstructure of the weld joint. Microstructure evolution and recrystallization mechanisms of high Mg alloyed Al-Mg alloy (Al-9.2 Mg-0.8Mn-0.2Zr-0.15Ti) during FSW with natural cooling and water cooling are carefully investigated by SEM, TEM and EBSD. Compared with natural cooling, water cooling can refine grain size and produce the higher fraction of high-angle grain boundaries (HAGBs) and lower texture intensity in the stir zone (SZ) but generate the lower fractions of HAGBs in the thermo-mechanically affected zone (TMAZ) and heat-affected zone (HAZ) and the higher texture density in the HAZ of the weld joint. The dispersed Al 6 Mn phases and some broken Al 6 (Fe, Mn) particles are existent in the SZ of both FSWed joints, while the β-Al 3 Mg 2 phase is dissolved in the SZ due to the frictional heat. Continuous dynamic recrystallization (CDRX) and dynamic recovery (DRV) are the main mechanisms of microstructure evolution in the SZ of both FSWed joints. CDRX occurs in the TMAZ of the joint with natural cooling, while discontinuous dynamic recrystallization (DDRX) occurs in that with water cooling. Static recovery (SRV) and continuous static recrystallization (CSRX) are the main mechanisms of microstructure evolution in the HAZ of the joint with natural cooling, while the microstructure evolution in the HAZ of the joint with water cooling includes SRV and discontinuous static recrystallization mechanism (DSRX).
MoreTranslated text
Key words
Al-Mg alloy,friction stir welding,microstructure evolution,water cooling
AI Read Science
Must-Reading Tree
Example
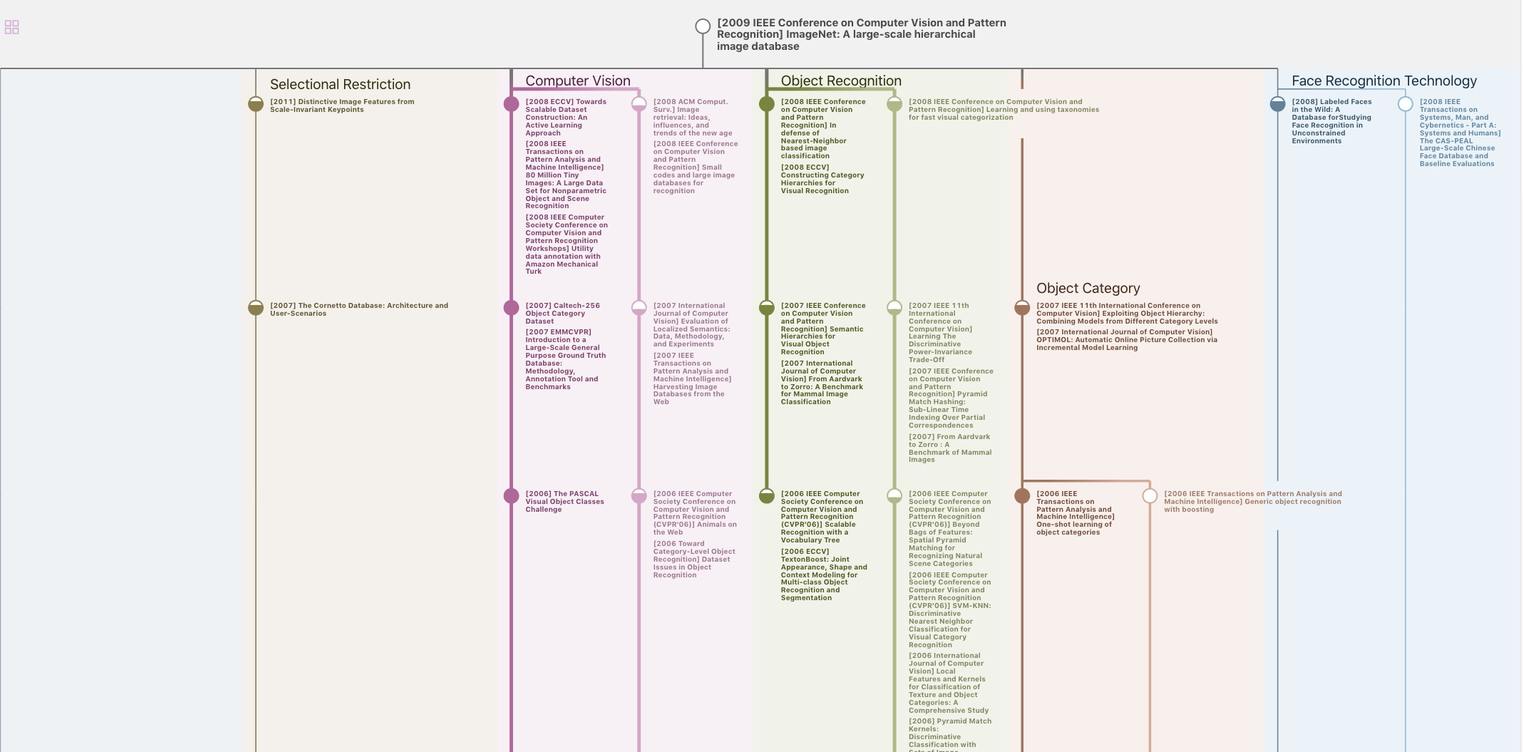
Generate MRT to find the research sequence of this paper
Chat Paper
Summary is being generated by the instructions you defined