Welding of Super Duplex Stainless Steel and Austenitic Stainless Steel: Influence and Role of Bicomponent Fluxes
MATERIALS AND MANUFACTURING PROCESSES(2023)
摘要
This study investigated dissimilar tungsten inert gas and activated tungsten inert gas welding experimental results of austenitic 202 with a super duplex 32760 stainless steel. Their microstructural study revealed a balanced austenite-ferrite morphology that mainly consisted of Widmanstatten austenite (WA), grain boundary austenite (GA), and intergranular austenite (IGA). The study showed that the use of flux reduced the heat input necessary to achieve complete penetration, which tends to increase ferrite count in the heat-affected zone and the weld zone of weldment, resulting in minimizing the hot cracking propensity. Further, structure-property connections were also established by evaluating these two weldments' tensile strength, impact strength, and microhardness. It was determined that weldments of activated tungsten inert gas weldment had better mechanical properties than traditional tungsten inert gas weldment. A weld zone fracture occurred near the austenitic weld interface in both weldments. It was noticed that unmixed zone formation on the side of the austenitic steel was to blame for the poor mechanical properties and failure of tungsten inert gas and activated tungsten inert gas weld joints. In both cases, the hardness distribution in the weld zones is ranked as super duplex stainless steel base metal > heat-affected zone of super duplex steel side > welded zone > heat-affected zone of austenitic steel side > austenitic base metal.
更多查看译文
关键词
Bicomponent flux, activated tungsten inert gas, microstructure, fractographs, corrosion, secondary austenite
AI 理解论文
溯源树
样例
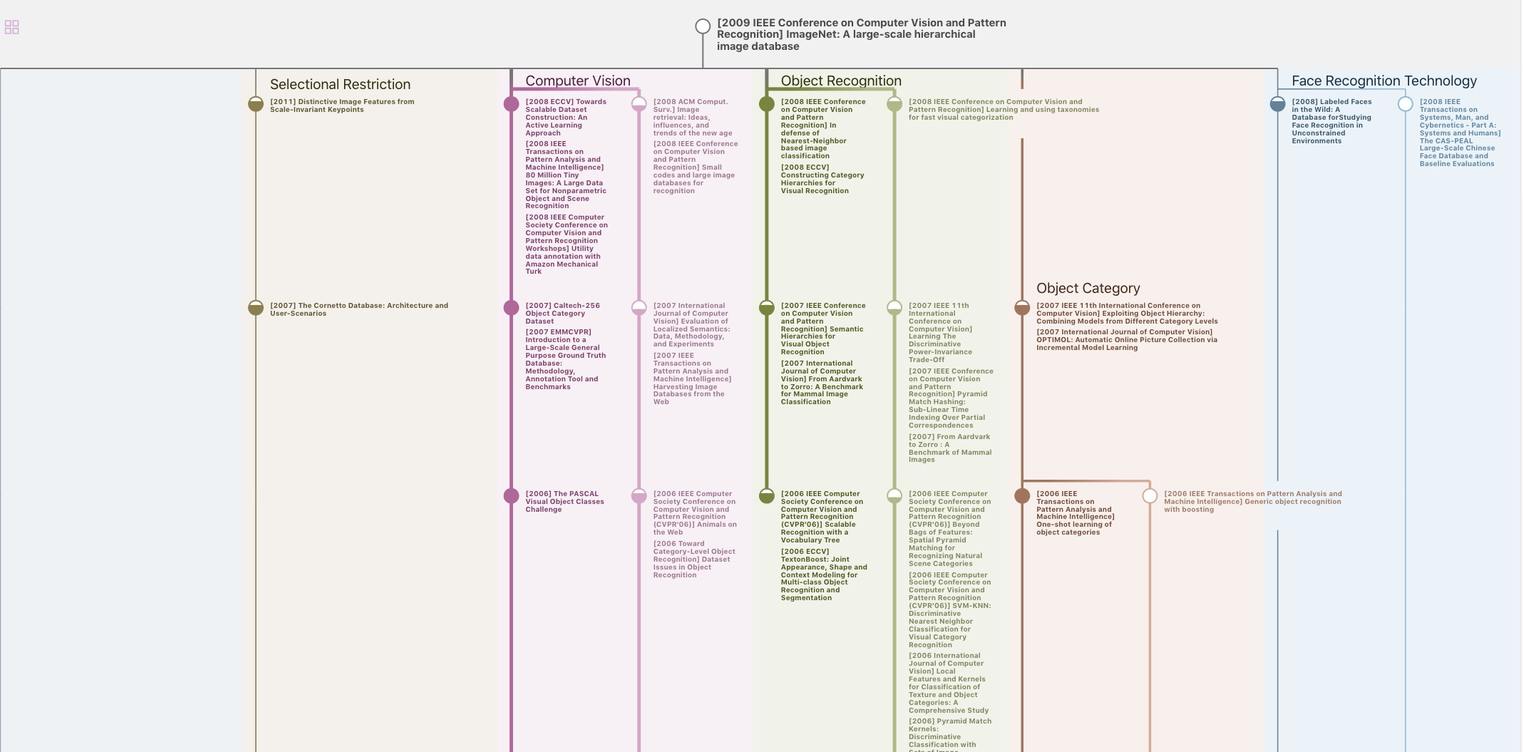
生成溯源树,研究论文发展脉络
Chat Paper
正在生成论文摘要