An improved creep damage mechanics model and its application to evaluate creep strain design codes for hot outlet manifold in steam reformer furnace
International Journal of Pressure Vessels and Piping(2022)
摘要
Considering the effect of carbide coarsening and cavity nucleation and growth on the creep damage of Fe–Cr–Ni-based austenitic stainless steels, an improved creep damage constitutive model is established based on the hyperbolic sine function. The material parameter optimisation procedure and the associated ABAQUS user subroutine CREEP of the model are also developed. In addition, the improved model is calibrated and validated by comparing the extrapolated failure times for the three creep damage models, and applied to an idealized pipe bend to evaluate the inelastic strain limits in the ASME-NH code. The results show that the proposed model is capable to reflect the creep behaviour of a hot outlet manifold steel under different stress levels at 890 °C. During the long-term creep exposure of the manifold component, the limits of 1% creep membrane strain and 2% creep membrane strain + bending strain ruled in ASME-NH code may not be conservative. If only the cumulative inelastic strain is considered in the structural design, membrane strain is the primary rule for investigating the failure of the pipe bending.
更多查看译文
关键词
Manifold,Creep,Design code,Strain classification
AI 理解论文
溯源树
样例
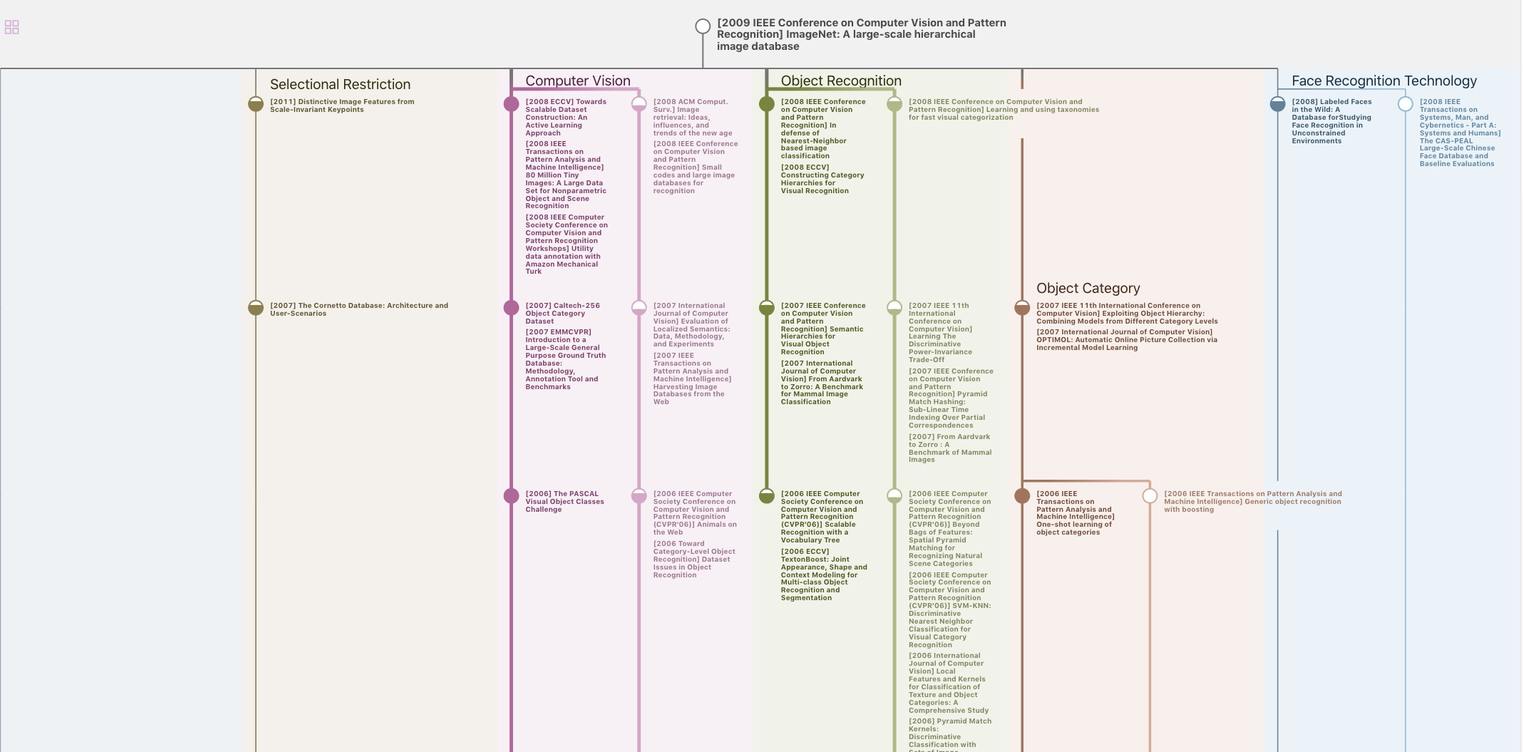
生成溯源树,研究论文发展脉络
Chat Paper
正在生成论文摘要