Numerical simulation research on hot stretch straightening of thin-walled T-shaped profile of titanium alloy assisted by resistance heating
The International Journal of Advanced Manufacturing Technology(2022)
摘要
In accordance with the bending deformation of titanium alloy profile generated by hot extrusion, the hot stretch straightening assisted by resistance heating is an effective strategy to improve the straightness accuracy. In order to reveal the heat transfer behavior and deformation mechanism of titanium alloy profile during hot straightening, this study focuses on Ti-6.5Al-2Zr-1Mo-1 V alloy thin-walled T-shaped profile with unequal thicknesses. The flow stress curves of profile within temperatures from 400 to 800 ℃, strain rate at 5·10 −4 s −1 were obtained by uniaxial tensile tests. The thermal boundary conditions between profile and air were determined by using inverse analysis experiment. Then, the thermal-electrical–mechanical multi-field coupling numerical simulation model was established. The temperature distribution, stress distribution, and deformation of profile were investigated systematically. The results show that the non-uniform temperature field with low temperature in thinner wall region and high temperature in thicker wall region would form during resistance heating. The stress distribution of stretch straightening process was determined by the temperature distribution and the initial bending shape of profile jointly, thereby affecting the springback deflection and direction after unloading. The established numerical simulation models, which have been verified by process experiments, could lay foundation for the prediction and process optimization in hot stretch straightening of titanium profile.
更多查看译文
关键词
Titanium alloy thin-walled T profile,Resistance heating,Hot stretch straightening,Numerical simulation
AI 理解论文
溯源树
样例
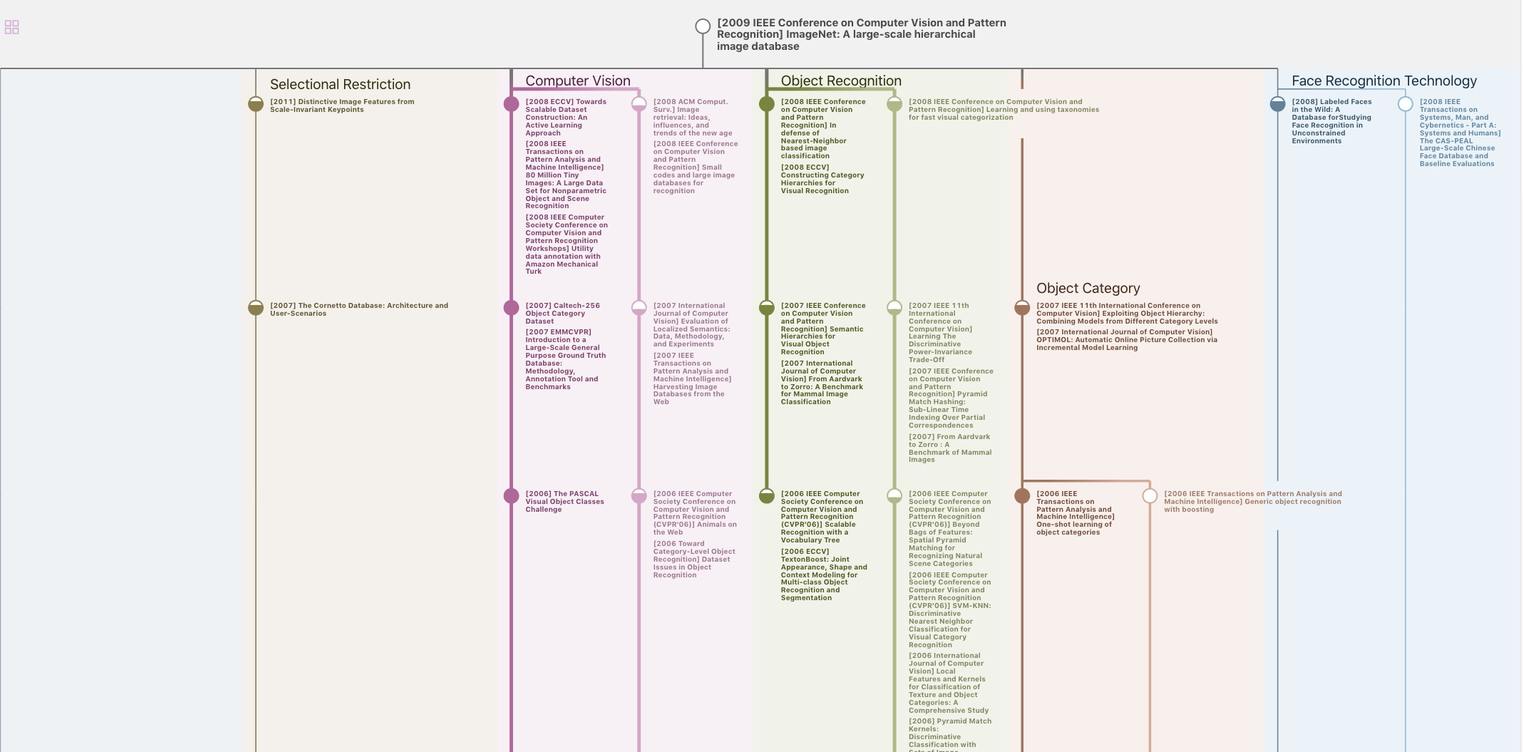
生成溯源树,研究论文发展脉络
Chat Paper
正在生成论文摘要