Evaluation of experimentally observed asymmetric distributions of hardness, strain and residual stress in cold drawn bars by FEM-simulation
Journal of Materials Research and Technology(2018)
Abstract
The purpose of this paper is to investigate the correlation of strain and hardness parameters in a drawing process chain of an SAE 1045 steel bar. The present work discusses the application of the experimental and numerical method of analysis, based on hardness measurements, which allows evaluation of the strain distribution and mechanical properties in drawn products. The influence on the strain, hardness and residual stress distributions of cold drawing parameter variations were investigated by numerical simulation. A misalignment between bar and drawing tool was evaluated in the models, as well as variation of friction at different regions of the bar. Compression tests were carried out at different reductions to determine the flow curve and analyze the material behavior during a cold hardening process. The microstructural analysis has shown a potential influence of material segregation in the characteristics of the final products. Simulation results validate the assumption of die misalignment and inhomogeneous lubrication influences on residual stresses profiles after wire drawing. Taking into account effects of misalignment and friction at the same time, in a so-called combination model, a better agreement between numerical simulation and experimental results for cold drawing process was achieved.
MoreTranslated text
Key words
Hardness,Plastic strain deformation,Residual stresses
AI Read Science
Must-Reading Tree
Example
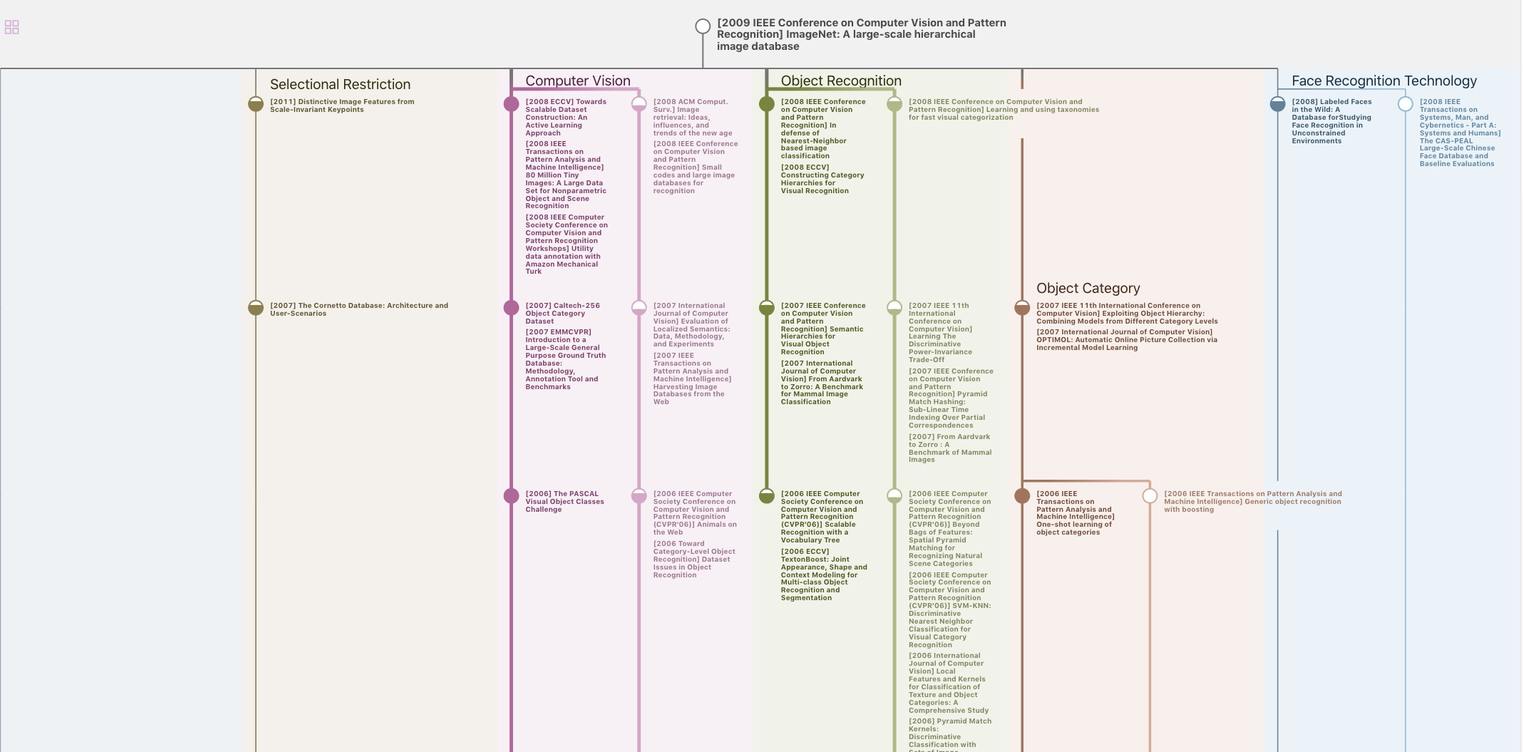
Generate MRT to find the research sequence of this paper
Chat Paper
Summary is being generated by the instructions you defined