FESM-based approach for stiffness modeling, identification and updating of collaborative robots
INDUSTRIAL ROBOT-THE INTERNATIONAL JOURNAL OF ROBOTICS RESEARCH AND APPLICATION(2023)
摘要
Purpose The purpose of this paper is to introduce a method for stiffness modeling, identification and updating of collaborative robots (cobots). This method operates in real-time and with high precision and can eliminate the modeling error between the actual stiffness model and the theoretical stiffness model. Design/methodology/approach To simultaneously ensure the computational efficiency and modeling accuracy of the stiffness model, this method introduces the finite element substructure method (FESM) into the virtual joint method (VJM). The stiffness model of the cobots is built by integrating several 6-degree of freedom virtual joints that represent the elastic deformation of the cobot modules, and the stiffness matrices of these modules can be identified and obtained by the FESM. A model-updating method is proposed to identify stiffness influence coefficients, which can eliminate the modeling error between the actual prototype model and the theoretical finite element model. Findings The average relative error and the cycle time of the proposed method are approximately 6.14% and 1.31 ms, respectively. Compared with other stiffness modeling methods, this method not only has high modeling accuracy in high dexterity poses but also in low dexterity poses. Originality/value A hybrid stiffness modeling method is introduced to integrate the modeling accuracy of the FESM into the VJM. Stiffness influence coefficients are proposed to eliminate the modeling error between the theoretical and actual stiffness models.
更多查看译文
关键词
Collaborative robot stiffness modeling,Stiffness identification,Model updating,Finite element substructure method
AI 理解论文
溯源树
样例
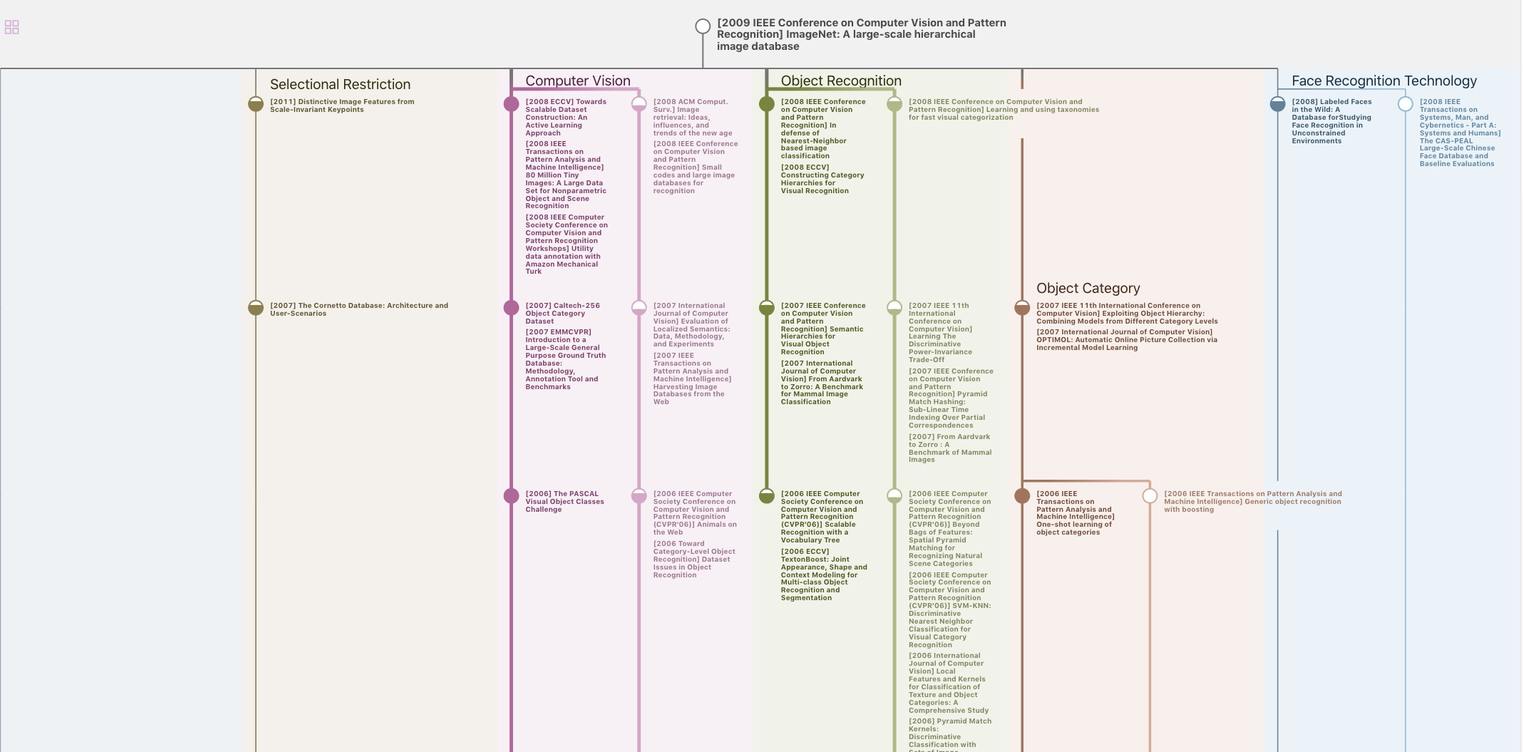
生成溯源树,研究论文发展脉络
Chat Paper
正在生成论文摘要