Numerical Simulation of 50 mm 316L Steel Joint of EBW and Its Experimental Validation
METALS(2022)
Abstract
The 316L thick plate electron beam welding (EBW) has been widely used in fusion test reactor manufacturing. Therefore, the numerical simulation of the 50 mm 316L austenitic stainless steel by two heat sources and experimental on microstructure and residual stress have been studied in this article. In the simulation study, the traditional heat source model (3D Gaussian heat source) and composite heat source (double ellipsoid heat source superimposed on the 3D Gaussian heat source) were proposed to simulate the welding of local joint. Weld cross-section, temperature curve, and residual stress after welding obtained by simulations were investigated. The experimental study involved residual stress tests and microstructure analysis. It turned out that the result of the composite heat source was closer to the actual joint. The residual stress distribution of simulation was validated and in accordance with experimental measurement. Moreover, the microstructures were studied by electro backscattered diffraction (EBSD) and compared with the temperature curve. The formation mechanism of microstructural heterogeneity was caused mainly by different thermal cycles at different positions of the thick plate. The top of the joint was more prone to stress concentration.
MoreTranslated text
Key words
electron beam welding, numerical modeling, residual stress, microstructure
AI Read Science
Must-Reading Tree
Example
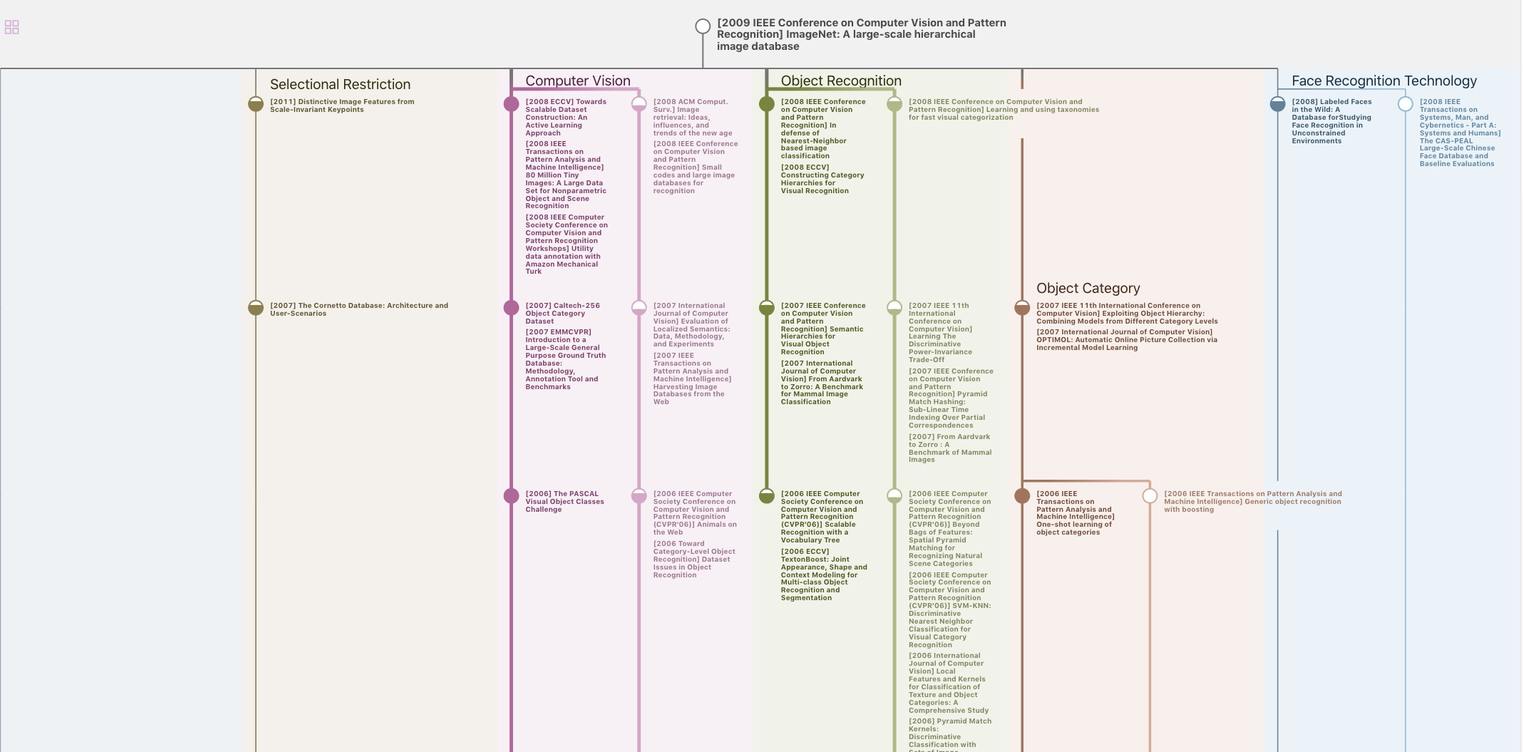
Generate MRT to find the research sequence of this paper
Chat Paper
Summary is being generated by the instructions you defined