Comparative analysis of tool wear progression of dry and cryogenic turning of titanium alloy Ti-6Al-4V under low, moderate and high tool wear conditions
The International Journal of Advanced Manufacturing Technology(2022)
摘要
Titanium alloys results in high tool wear when machined at elevated cutting speeds because of their high temperature strength and low thermal conductivity. The issue further aggravates when machining is carried out at cutting speeds above 60 m/min. Since industrial productivity necessitates the use of cutting speeds in excess of 100 m/min, aggravated tool wear occurs. Economy warrants the utilization of available resources efficiently, over a wide range of cutting conditions for prolonged durations. This study analyzed various vital aspects of tool wear progression of Ti-6Al-4V when machined at diverse machining parameters under dry and cryogenic conditions. Machining parameters, used in this research, were from a wide bracket of cutting speed and feed rate for comparative analysis. The progression of tool life was plotted over machining time for high, medium and low wear zone regions, selected from tool wear map available in literature. The research gave an insight about the tool wear progression under dry and cryogenic conditions till end of its useful life. Initially, comparison of continuous and intermittent tool wear under dry and cryogenic conditions was made. It was established that cryogenic machining gives more comparable results for continuous and intermittent machining than dry machining, with less than 1% difference in wear for 100 s of machining. Further investigation of flank wear progression at different intervals showed that, in comparison with dry progression, cryogenic tool wear progresses at a more linear and slower rate throughout its useful life. This establishes the fact that tool wear rate remains constant during evolution of tool wear. Tool wear regions are re-categorized by use of cryogenic cooling. Machining under cryogenic conditions enhances tool life up to 170% at certain machining parameters owing to its high cooling capacity. Difference in tool wear was characterized using tool chip contact length analysis, identifying the seizure and slip regions through EDS analysis. The tool chip contact length is found to reduce owing to elimination of slip region due to cryogenic media. Energy consumption analysis highlights that cryogenic machining improves sustainability by reducing chip thickness and shear plane. Research outcome forms the basis for further studies concerning tool wear evolution under cryogenic conditions.
更多查看译文
关键词
Titanium,Ti-6Al-4V,Cryogenic machining,Tool wear progression,Tool chip contact length
AI 理解论文
溯源树
样例
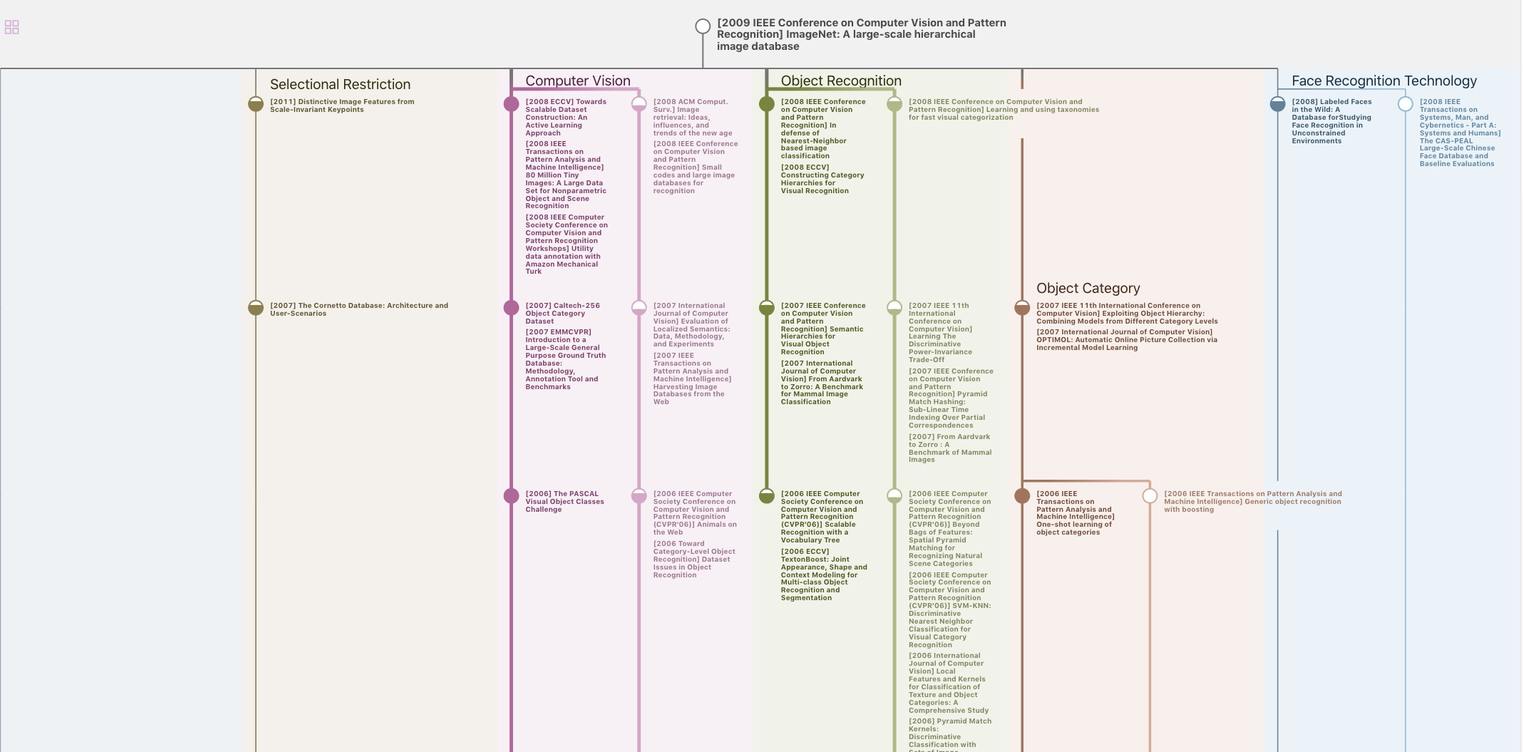
生成溯源树,研究论文发展脉络
Chat Paper
正在生成论文摘要