Concurrent Modeling of Porosity and Microstructure in Multilayer Three-Dimensional Simulations of Powder-Bed Fusion Additive Manufacturing of Inconel 718
Additive manufacturing(2022)
Key words
Additive manufacturing,Modeling,Microstructure structure,INCONEL 718
AI Read Science
Must-Reading Tree
Example
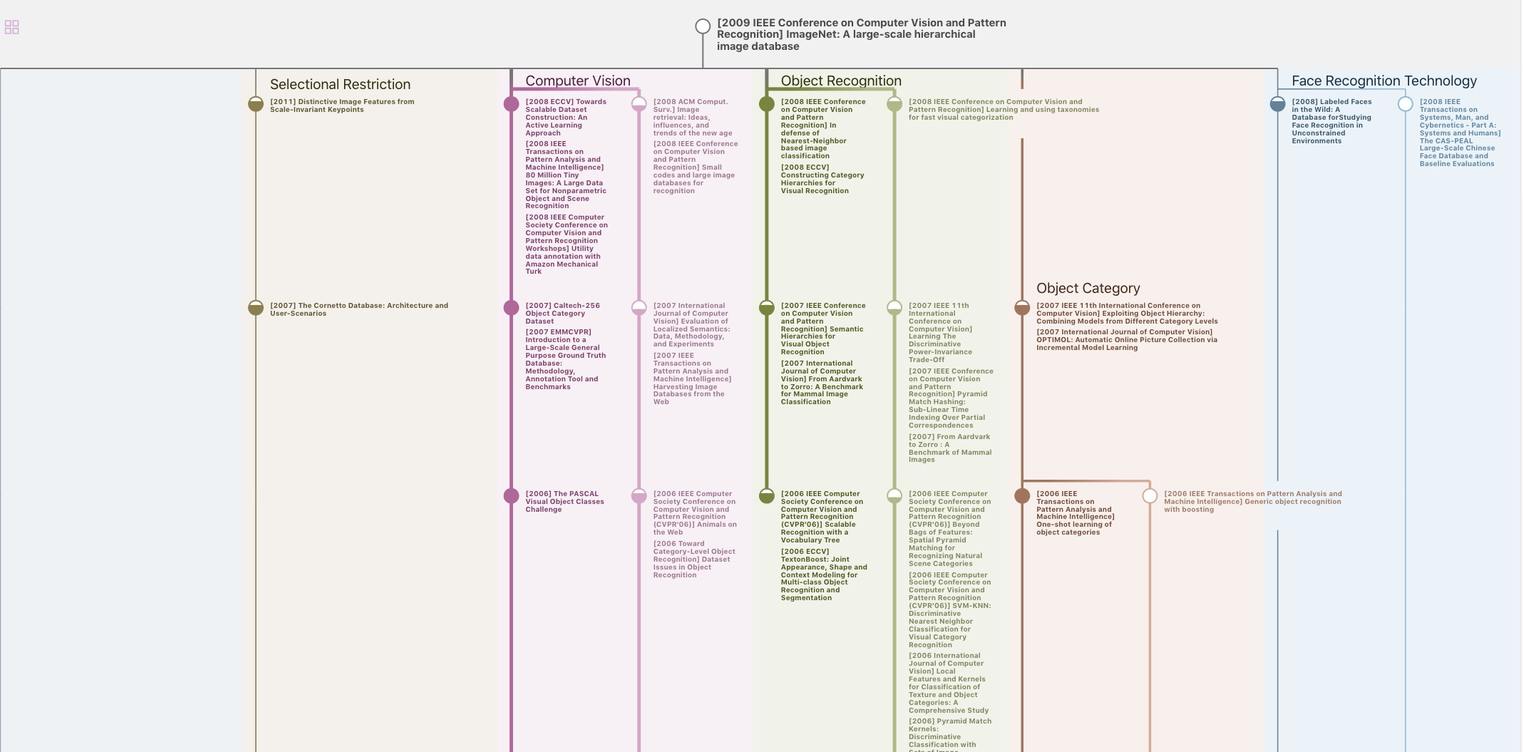
Generate MRT to find the research sequence of this paper
Chat Paper
Summary is being generated by the instructions you defined