Effect of Stacking Sequence on Stiffness of Al / CFRTP Multi-Material Hat Shaped Member and Its Cost Evaluation
Journal of the Society of Materials Science, Japan(2021)
Abstract
Due to the high cost of carbon fiber reinforced plastics (CFRP), the use of CFRP is limited to the appropriate part, which is based on the multi-material concept. We have molded the multi-material hat-shaped members by press-injection hybrid molding, in which carbon fiber reinforced thermoplastics (CFRTP) are pressed as the outer structural material followed by injection molding, and their mechanical properties have been evaluated. The selection of the stacking sequence of CFRTP, the material ratio of Al alloy and CFRTP, and its configurations are currently carried out on a trial and error basis. To reduce experimental costs, it is important to select appropriate configurations by simulation. In this study, the effects of the stacking sequence of CFRTP, material ratio of Al Alloy and CFRTP, and the stacking order on the stiffness of a hat-shaped member were analyzed by finite element method. Three points bending test for two types of model using neat PA6 and carbon fiber reinforced PA6(CF/PA6) as the injection materials were analyzed. In addition, their stiffness, specific stiffness, and specific stiffness per cost of molded part were calculated. In the analysis of the bending test of the hat-shaped member, the model using CFRTP with the stacking sequence of [±45] showed the higher stiffness. This is because the large strain at the side of the surface material was in the 40° direction. The hat-shaped member using only CFRTP with stacking sequence [±45] for the surface material served as the outer shell structure showed the highest specific stiffness. Furthermore, the stiffness, specific stiffness and specific stiffness per cost of molded part with injection material of CF/PA6 were 6.6, 6.3 and 5.0 times higher than neat PA6 model in average, due to the increased stiffness of the rib structure. In hat-shaped member, the use of carbon fiber reinforced PA6 to mold rib structure is extremely effective to obtain low cost and high stiffness member.
MoreTranslated text
Key words
Fiber-Reinforced Composites
AI Read Science
Must-Reading Tree
Example
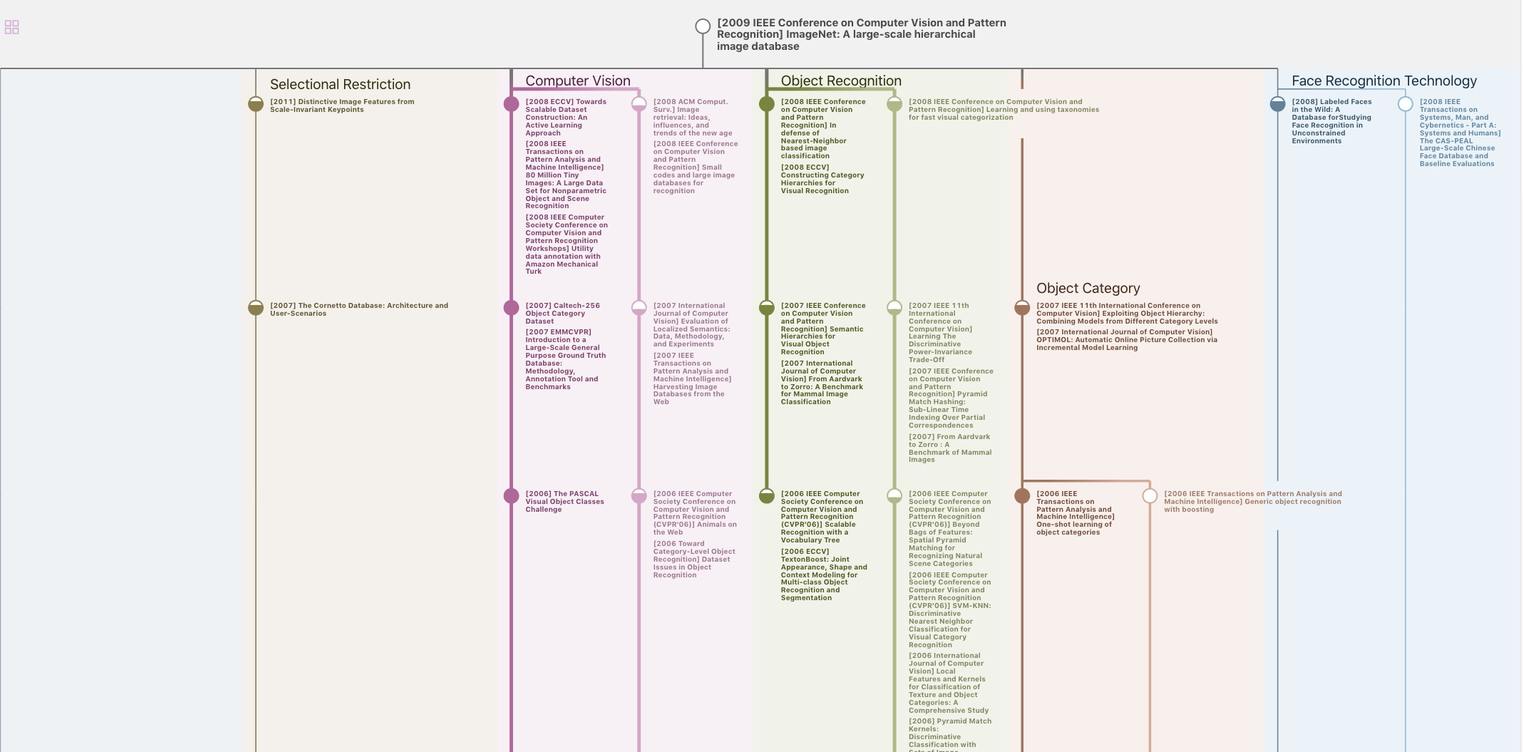
Generate MRT to find the research sequence of this paper
Chat Paper
Summary is being generated by the instructions you defined