CFD Simulation of Cavitation Erosion Behavior in an Impeller of Industrial Lean Amine Liquid Pump
Volume 2: Computer Technology and Bolted Joints; Design and Analysis(2021)
Abstract
Abstract Multistage pump of lean amine liquid is crucial rotating equipment in an industrial refining catalytic reforming unit. Cavitation often causes the damage of impeller in the pump to affect the long-term safe operation of unit. The formation of cavitation on impeller is 3D simulated by using Zwart-Gerber-Belamri model in accord with the actual position under the industrial operating condition. The discrepancies of cavitation range between different volume flux (400 to 800 m3/s. operating pressure (0.4 to 2.0 MPa) and vapor pressure of lean amine liquid (0.05 to 0.5 MPa) in terms of the industrial running conditions every stage impeller are investigated to guide design and safety operation of pump. The simulation results indicate that the impeller cavitation often starts from the forward-curved groove of the blade. and then gradually expands along the flow path of the blade and the two side walls of the forward bend. When the volume flux exceeds critical value of cavitation. the impellers appear cavitation and those ranges enlarge and expend along the flow direction of the blade with the increase of volume flux. With the cavitation pressure increasing. the cavitation ranges of impeller lesson even to disappear. especially at 2.0 MPa. Bigger vapor pressure of lean amine liquid leads easily to erosion.
MoreTranslated text
Key words
Cavitation,impeller,pump,simulation
AI Read Science
Must-Reading Tree
Example
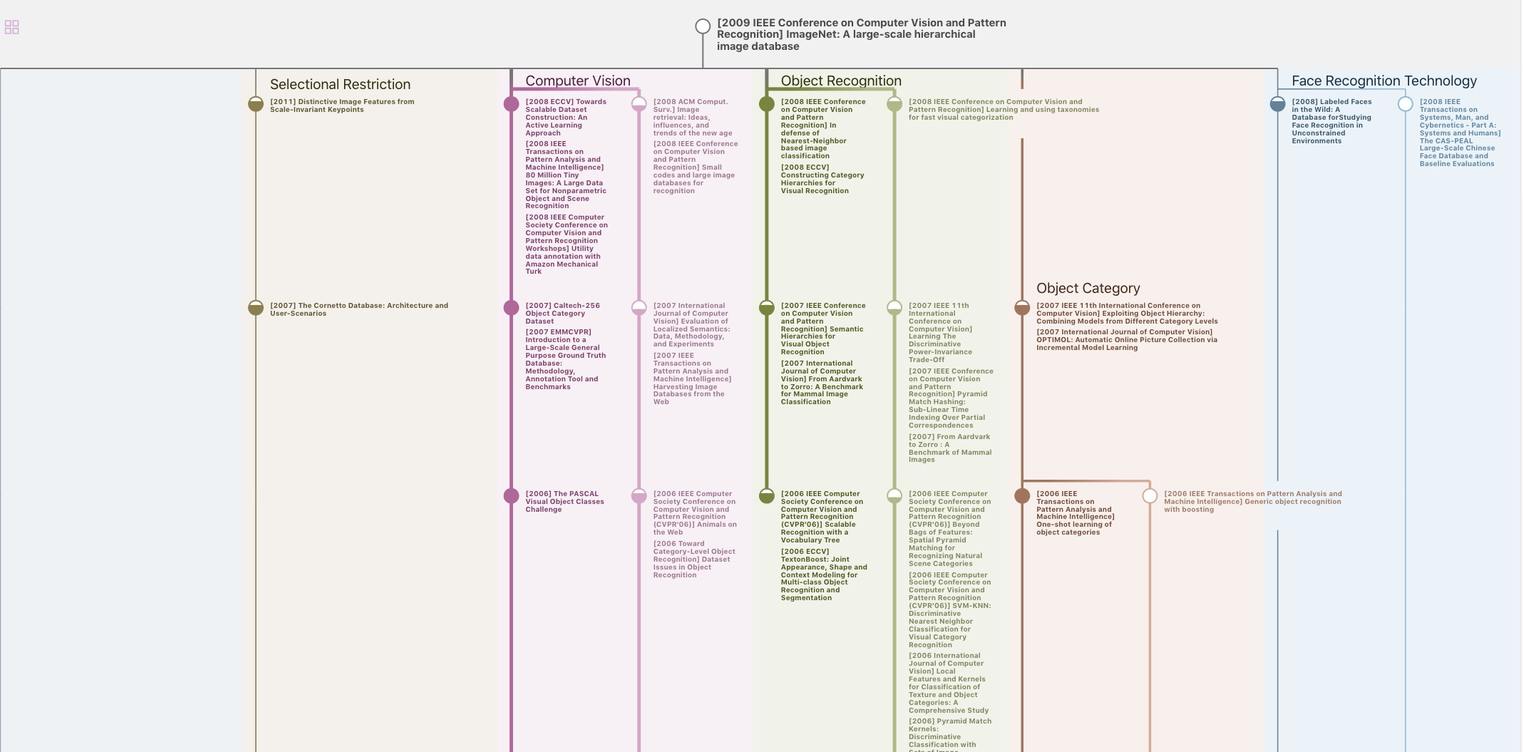
Generate MRT to find the research sequence of this paper
Chat Paper
Summary is being generated by the instructions you defined