CFD study of heat transfer augmentation and fluid flow characteristics of turbulent flow inside helically grooved tubes
Journal of the Brazilian Society of Mechanical Sciences and Engineering(2022)
Abstract
In this study, heat transfer enhancement in an internally helically grooved tube is investigated numerically and validated with experimental data from Aroonrat et al. (Int Commun Heat Mass Transfer 42:62-68, 2013) Simulations were conducted utilizing computational fluid dynamics software package ANSYS-FLUENT to gain a deeper understanding of heat transfer augmentation in a plain tube and helically grooved tubes with three different pitch sizes, 19, 57, and 95 mm. The simulations were performed for turbulent flow conditions of Reynolds number of 12,000 to 22,000 utilizing water as a working fluid. Results showed that the enhanced tube independent of tested groove pitch sizes provided better thermal–hydraulic performance than their plain tube counterparts. With the view of estimating the optimum case that gives the highest thermal performance factor in using this choice of heat transfer enhancement technique, analysis of its overall enhancement is also done. Mathematical correlations for predicting Nusselt number and friction factor in an internally helically grooved tube are proposed in this study as well. The use of enhanced surface geometry considering the internally helically grooved tube is suitable and profitable if applied in a relatively low turbulent Reynolds number region of the evaporator.
MoreTranslated text
Key words
Heat transfer enhancement,Grooved pitch size,Thermal performance factor,CFD simulation
AI Read Science
Must-Reading Tree
Example
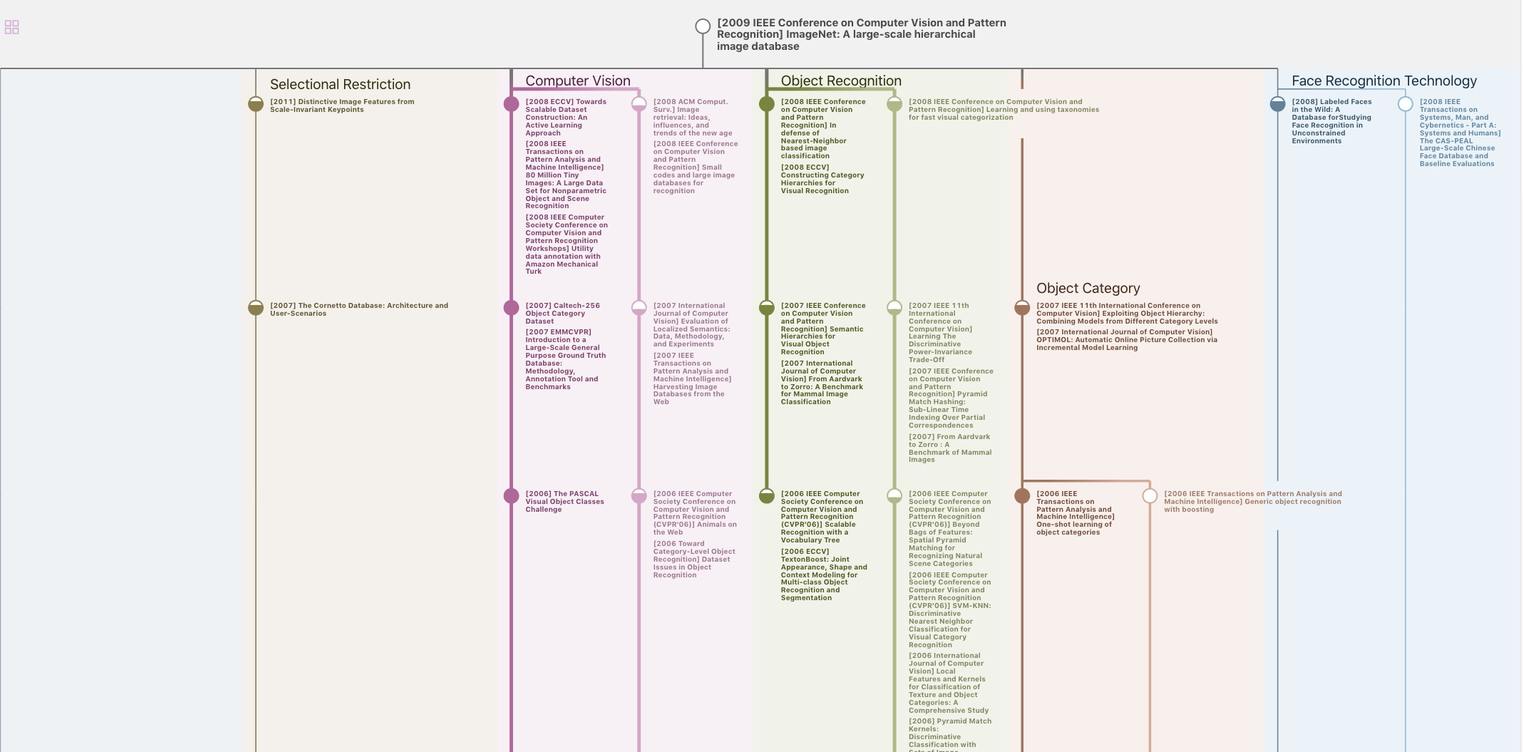
Generate MRT to find the research sequence of this paper
Chat Paper
Summary is being generated by the instructions you defined