Mechanized spreading of ceramic powder layers for additive manufacturing characterized by transmission x-ray imaging: Influence of powder feedstock and spreading parameters on powder layer density
Powder Technology(2022)
摘要
Spreading of uniform, dense powder layers is a critical requirement for powder bed additive manufacturing (AM) processes, and layer quality is influenced by powder feedstock selection and spreading parameters. In prior work, quantification of powder layer density has required disruption of the powder layer after spreading, or compromise in the precision and/or design of the spreading mechanism compared to actual AM equipment. This work demonstrates the use of a precision, mechanized powder spreading testbed coupled with transmission x-ray imaging for spatially-resolved, non-contact powder layer density measurements. Specifically, the influence of several variables on the spreading of aluminum oxide powders is studied: powder size and shape, spreading tool choice (i.e., blade versus roller), traverse speed and/or rotation rate, and powder dispensing methodology (i.e., piston-fed vs hopper). For coarse powders, the density of layers spread with a roller geometry outperforms a blade geometry, reaching the tapped density for the coarse spherical powder. In addition, spreading with roller counter-rotation increases layer density for fine powders but decreases layer density for coarse powders. Increasing traverse speed or the use of textured rollers results in reduced powder layer density for fine powders. Finally, for fine powders, deposition with a vibrating hopper dispenser instead of a piston-fed mechanism, coupled with spreading by a counter-rotating roller, gives spread layer density equal to the tapped density.
更多查看译文
关键词
Powder bed additive manufacturing,Powder spreading,Recoating mechanism,powder bed density,Particle size and shape
AI 理解论文
溯源树
样例
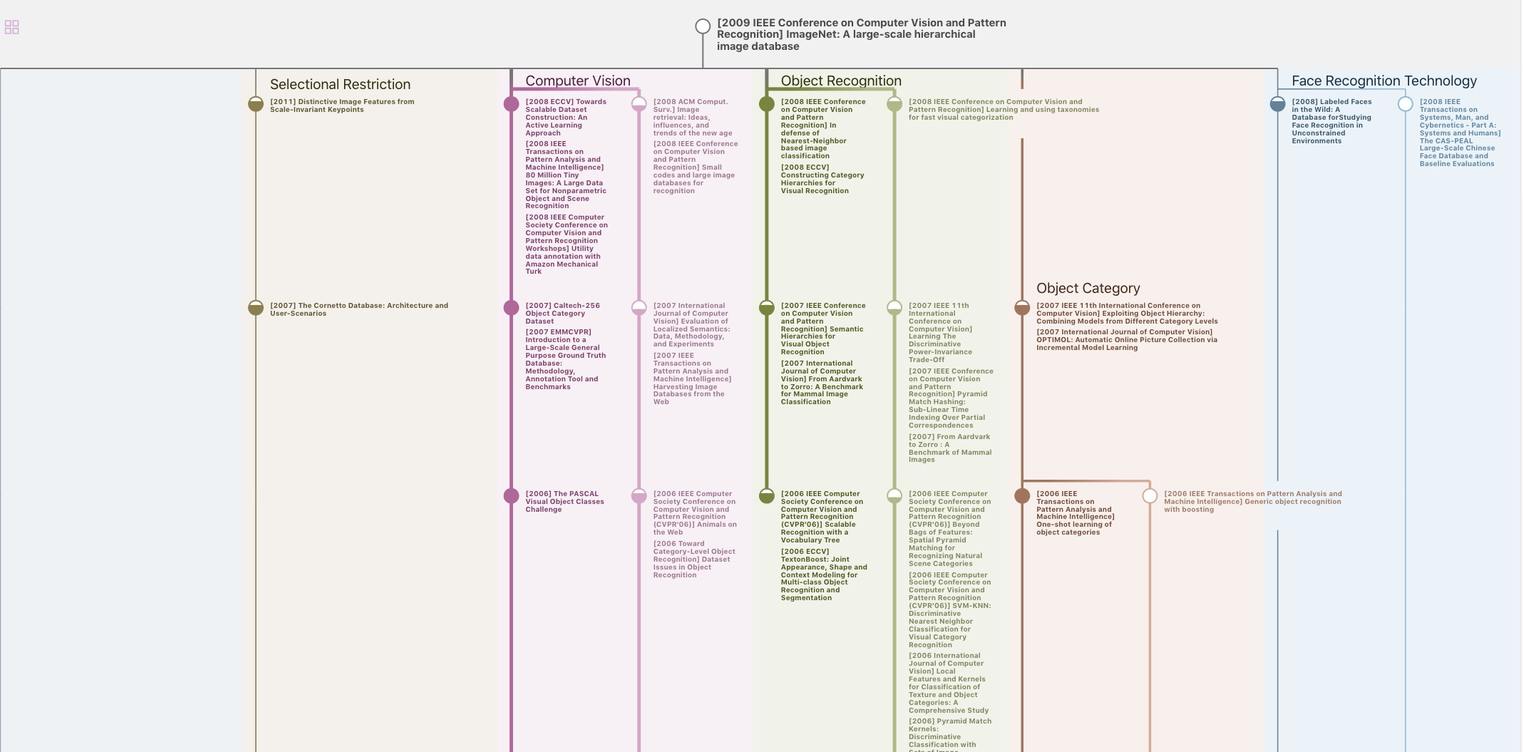
生成溯源树,研究论文发展脉络
Chat Paper
正在生成论文摘要