A Comparative Experimental and Numerical Study on Buckling Behavior of Composite Lattice Cylinders
IRANIAN JOURNAL OF SCIENCE AND TECHNOLOGY-TRANSACTIONS OF MECHANICAL ENGINEERING(2022)
Abstract
In this study, the buckling behavior of three samples of composite lattice cylinders made of Carbon/Epoxy, Glass/Epoxy, and Aramid/Epoxy materials manufactured by wet filament winding method under axial compressive loading has been investigated numerically and experimentally. In the numerical simulation, linear eigenvalue buckling analysis is achieved using ABAQUS software. Effect of four element types including quadratic beam element B32, conventional shell element S8R, continuum shell element SC8R, and solid element C3D20R on the buckling load, buckling mode shape and solution CPU-run-time are investigated. Comparison between the experimental test results and numerical results indicates that the most accurate element is C3D20R, while the most rapid and cost-effective element is S8R. Also, it is shown that the beam element B32 is not reliable enough for predicting buckling mode shape and buckling load. The experimental results show that local crippling of the helical ribs followed by delamination at the ribs’ intersection (nodes) is the predominant failure mode in all the composite samples.
MoreTranslated text
Key words
Composite lattice cylinder, Experimental method, Buckling mode shape, Axial buckling simulation, Finite element modeling, Cost-effective element
AI Read Science
Must-Reading Tree
Example
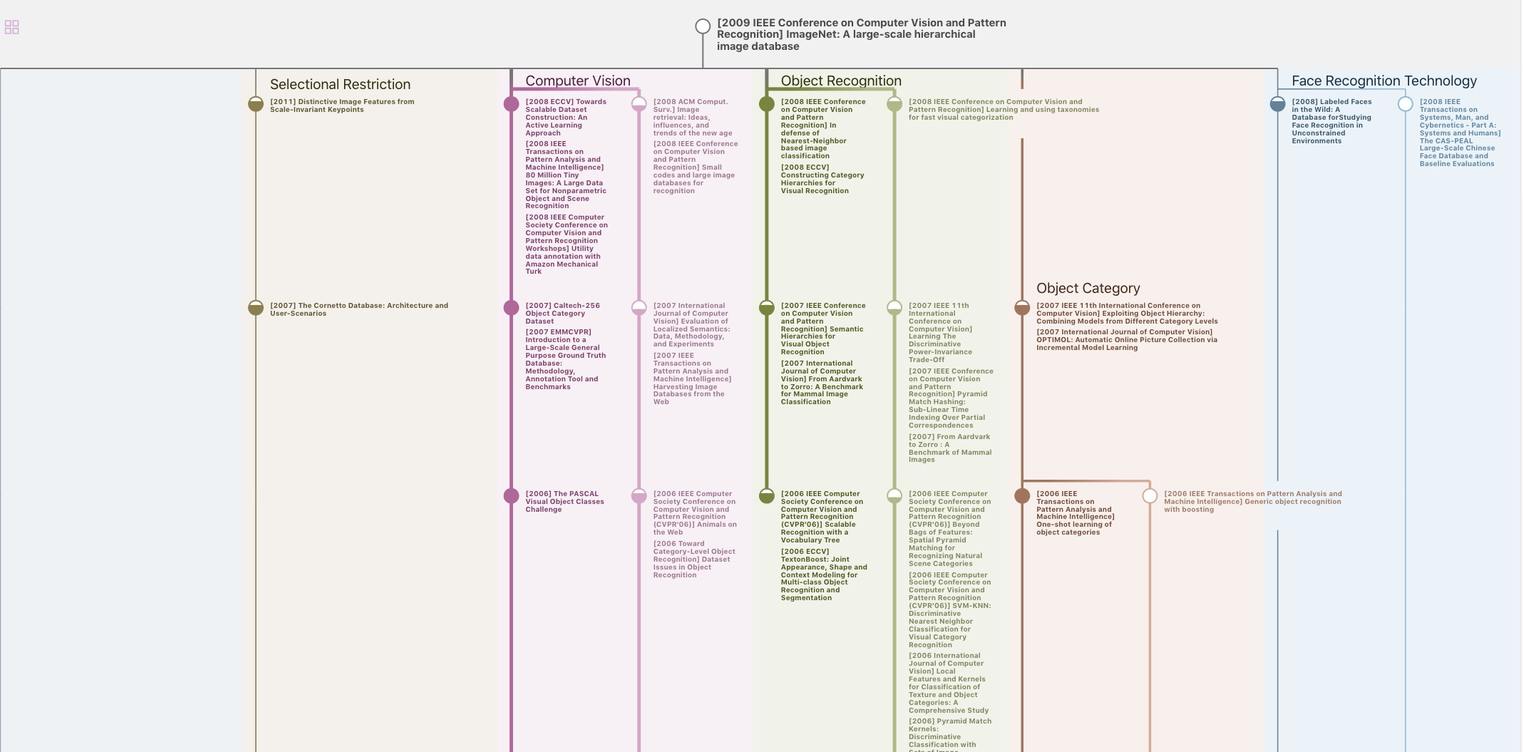
Generate MRT to find the research sequence of this paper
Chat Paper
Summary is being generated by the instructions you defined