Simulation of flow-field and debris temperature analysis in micro-electrical discharge milling using slotted tools
PROCEEDINGS OF THE INSTITUTION OF MECHANICAL ENGINEERS PART B-JOURNAL OF ENGINEERING MANUFACTURE(2022)
Abstract
In micro-electrical discharge milling (mu ED-milling), the rotation and forward feed motion of the tool is the key element responsible for evacuation of the debris particles. The inability to eliminate debris from the interelectrode gap (IEG) causes secondary discharge, short-circuit, and hampers removal rate. This problem is predominant in electrical discharge machining (EDM) where the tool is stationary. Various methods have been devised in the literature to boost debris removal from the IEG. In this paper, the use of a slotted tool with different cross-sections is proposed. The dielectric flow-field, debris trajectory, and cooling rate are calculated using computational fluid dynamics (CFD). Effect of different parameters such as tool rotation, gap size, jet velocity, the shape of slots on the dielectric flow is determined. The slots on the tool create turbulence which enhances the debris removal from the IEG. It also provides the space to accumulate the debris particles, thereby increasing the removal rate. The variation in the dielectric flow-field greatly affects the debris flushing from the IEG. The trajectory of the debris particles depends on their initial position in the IEG and they cool rapidly, which is validated using simulation and mathematical approach.
MoreTranslated text
Key words
CFD, debris, dielectric, electrical, discharge, milling, slotted tool
AI Read Science
Must-Reading Tree
Example
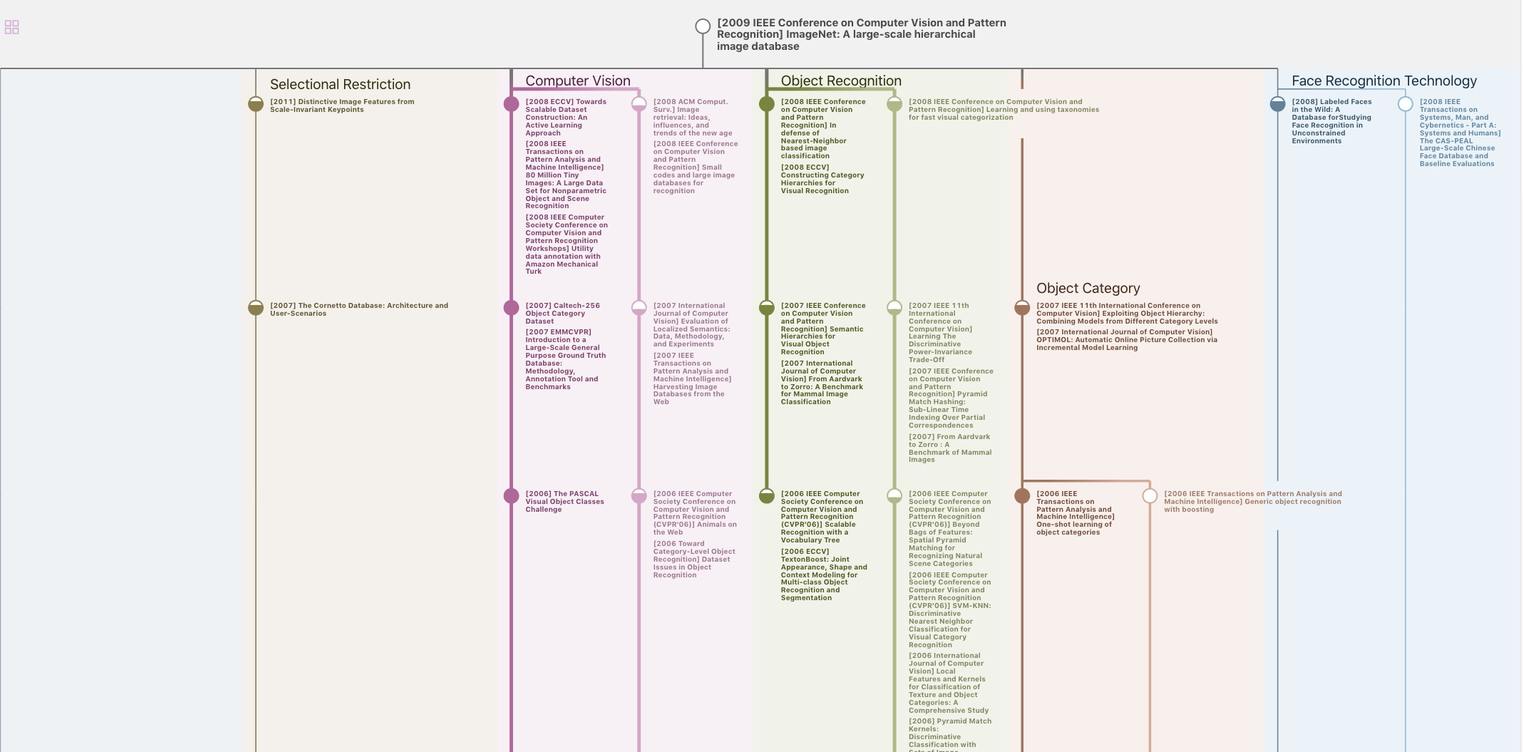
Generate MRT to find the research sequence of this paper
Chat Paper
Summary is being generated by the instructions you defined