From three-dimensional tessellations to lightweight filling materials for additively manufactured structures: Concept, simulation, and testing
PROCEEDINGS OF THE INSTITUTION OF MECHANICAL ENGINEERS PART L-JOURNAL OF MATERIALS-DESIGN AND APPLICATIONS(2022)
摘要
To improve the structural efficiency and reduce costs, most additively manufactured parts are printed as thin shells filled with a lightweight cellular material. The filling material reacts to secondary stresses and provides distributed support for the load-carrying outer shell. In a recent publication, the authors have proposed a two-step method to design lightweight filling metamaterials that are intrinsically strong and stiff. Conceptually, the space is first divided into repetitive volumes according to known three-dimensional tessellation schemes. The tessellation is then replaced by a kinematically rigid wireframe with beams along the edges and across the faces of the native volumes. Elaborating on that idea, the present paper pursues three objectives: (a) show the variety of material designs that derive from the tessellation-wireframe approach; (b) characterize the materials through finite element analyses on full-scale models and compare them with former predictions based on scaling and homogenization techniques; (c) validate the numerical results against experimental tests on a selection of prototype structures. Good correlation is revealed between theoretical predictions, computational models, and experimental data.
更多查看译文
关键词
Additive manufacturing,volume filling,periodic metamaterials,lattice structures,mechanical properties
AI 理解论文
溯源树
样例
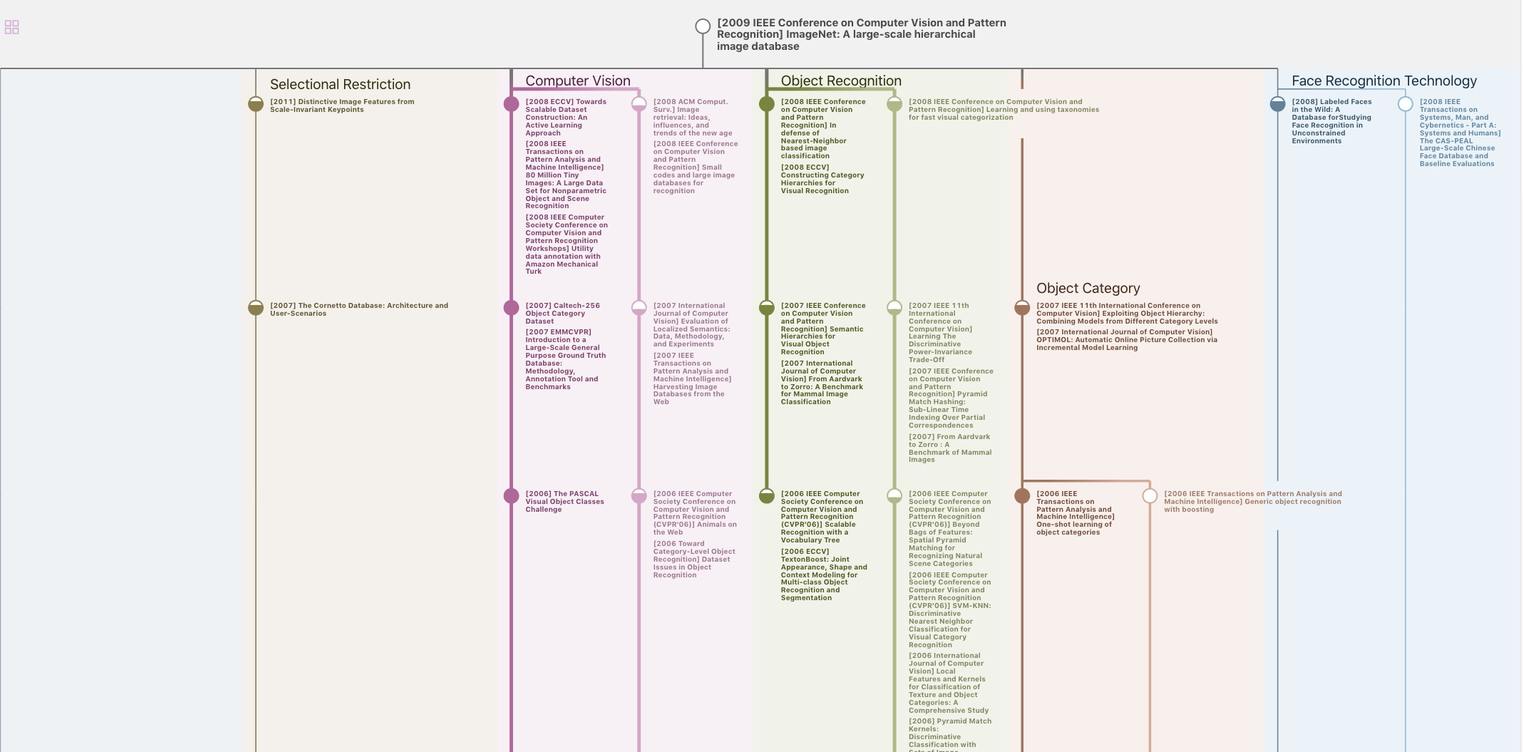
生成溯源树,研究论文发展脉络
Chat Paper
正在生成论文摘要