Finite Element Analysis of the Effects of Process Representations on the Prediction of Residual Stresses and Chip Morphology in the Down-Milling of Ti6Al4V: Part II: Effect of Flank Wear and Conventional Uncut Chip Thicknesses in Milling With Finite Cutting Edge Radius
JOURNAL OF MANUFACTURING SCIENCE AND ENGINEERING-TRANSACTIONS OF THE ASME(2022)
摘要
In Part II of these two-part papers, the effects of four finite element method (FEM) representations of the milling process on the prediction of chip morphology and residual stresses (RS) are investigated. Part II focuses on the milling of conventional uncut chip thickness h with finite cutting edge radius and flank wear, while Part I of these two-part papers has reported on the results in the case of milling small uncut chip thickness in the micrometer range with finite cutting edge radius. Two geometric models of the flank wear land composed of flat and curved wear land are proposed and assessed. The four process representations are (i) orthogonal cutting with flat wear land and with the mean uncut chip thickness h; (ii) orthogonal cutting with flat wear land and with variable h, which characterizes the down-milling process and which is imposed on a flat surface of the final workpiece; (iii) modeling the true kinematics of the down-milling process with flat wear land, and (iv) modeling the true kinematics of the down-milling process with curved wear land. They are designated as Cte-h, Var-h, True-h, and True-h*. The effectiveness of these representations is assessed when milling Ti6Al4V with a flank wear land of VB = 200 mu m.
更多查看译文
关键词
down-milling, FEM, chip morphology, residual stress, flank wear, ductile machining, rubbing
AI 理解论文
溯源树
样例
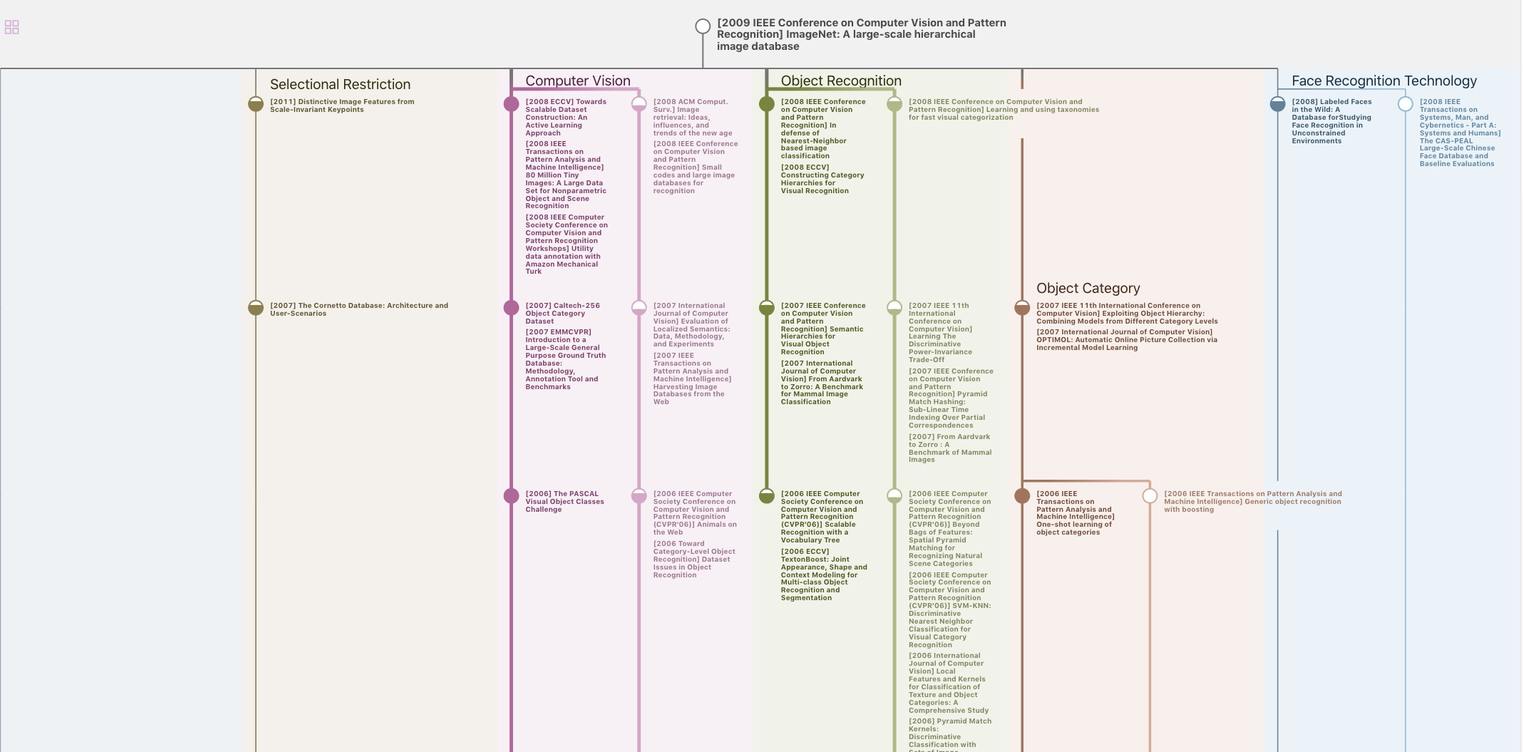
生成溯源树,研究论文发展脉络
Chat Paper
正在生成论文摘要