Fabrication of continuous carbon-fibers reinforced aluminum matrix composites and coating evolution during heat treatment
JOURNAL OF MATERIALS RESEARCH AND TECHNOLOGY-JMR&T(2022)
Abstract
The nickel (Ni) was coated onto carbon fibers (CFs) through an electroplating process to enhance the infiltration of aluminum (Al) matrix to fiber. Moreover, these continuous CFs reinforced Al matrix (CF/Al) composites were fabricated via a twin-roll casting method. Here, the effects of rolling speed, pouring temperature and solidification times on the morphologies of CF/Al composites were discussed. The results show that the rolling speed of 4 rad/min provided excellent integrity between reinforcement and matrix. Moreover, solidification times of 60 s offered an effective balance between the heat transfer and infiltration. Furthermore, pouring temperature of 700 degrees C was advantageous to infiltrate Al matrix into fibers. In addition, the influence of heat-treatment time on coating evolution and property of the materials were discussed through microstructure evolution, phases composition and mechanical property tests. The results confirmed that composites with outstanding mechanical properties were acquired at the temperature of 600 degrees C for 160 min in a tube furnace. Hence, it is concluded that the twin-roll casting approach has great application prospects in the fabrication of CF/Al composites with high tensile properties. (c) 2022 The Authors. Published by Elsevier B.V. This is an open access article under the CC BY-NC-ND license (http://creativecommons.org/licenses/by-nc-nd/4.0/).
MoreTranslated text
Key words
Continuous carbon fibers, Aluminum matrix composites, Twin-roll casting, Heat treatment, Coating evolution, Mechanical properties
AI Read Science
Must-Reading Tree
Example
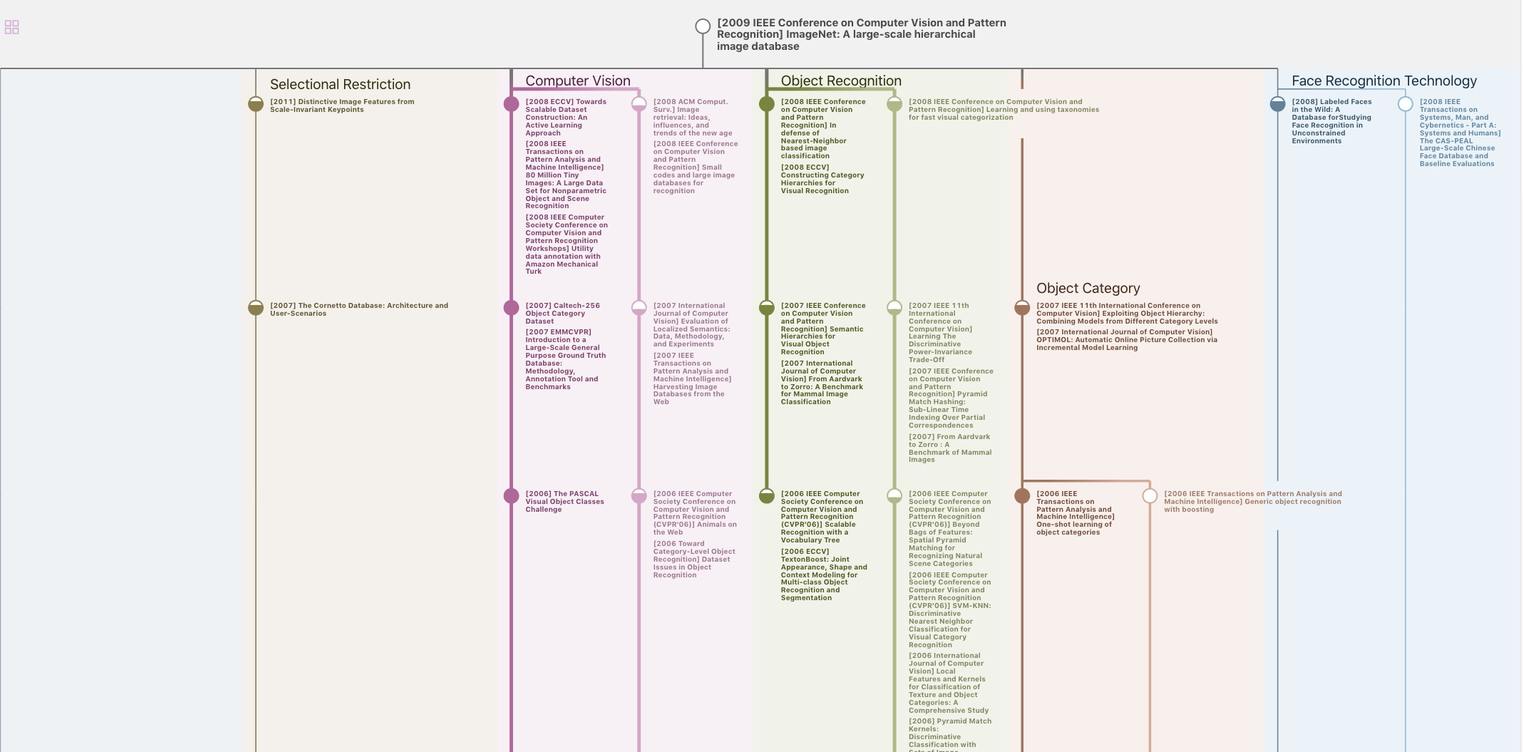
Generate MRT to find the research sequence of this paper
Chat Paper
Summary is being generated by the instructions you defined