Heat Transfer Coefficient of Zinc Phosphate Coating with Metal Soap during Cold Backward Extrusion
Defect and Diffusion Forum(2022)
Abstract
In cold forging, the temperature difference between the workpiece and the tool is small and thus deformation analysis is rarely coupled with thermal analysis. However, the friction coefficient of zinc phosphate coating with metal soap has a large temperature dependence. Consideration of the effects of workpiece and tool temperature change on the friction coefficient is thus expected to improve the analytical accuracy of cold forging. Thermally coupled cold forging analysis requires thermal conductivity, specific heat, heat transfer coefficient between the workpiece and the tool, in addition to the temperature dependence of flow stress and friction coefficient. The heat transfer coefficient between workpieces coated with zinc phosphate with metal soap and tools is investigated in this paper. Cold backward extrusion was performed with a 50% reduction of area, and the temperature history in the punch was measured with a thermocouple. The forging speed was 1, 3, and 10 spm. FEM analysis was performed to simulate the experiment by considering the temperature dependence of flow stress and friction coefficient. The heat transfer coefficient was estimated at 20 kW/(m2•°C) by comparing the experimental result and calibration curves.
MoreTranslated text
Key words
zinc phosphate coating,heat transfer,metal soap,extrusion
AI Read Science
Must-Reading Tree
Example
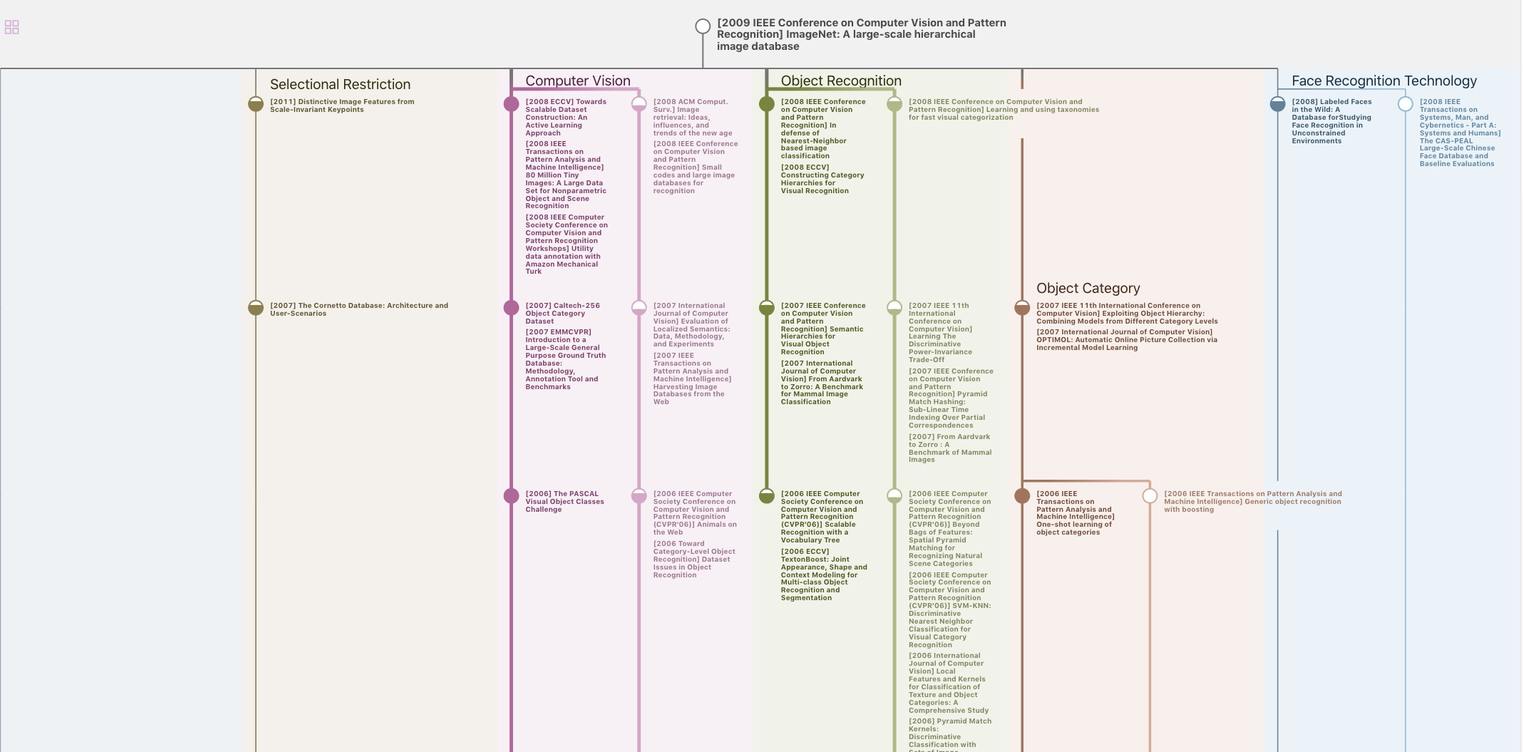
Generate MRT to find the research sequence of this paper
Chat Paper
Summary is being generated by the instructions you defined