Optimizing the coupling structural parameters of composite porous vapor chamber with radial grooves based on design of experiment and response surface
Applied Thermal Engineering(2022)
Abstract
• Groove parameters of composite porous vapor chamber (CPVC) are highly coupled. • A decoupling strategy is developed to handle the coupling groove parameters. • Design of experiments and response surface are used to optimize groove parameters. • Parameter effects on the performance of CPVC are analyzed more systematically. • The optimized parameters improve the thermal hydraulic performance of CPVC. The recently developed composite porous vapor chamber (CPVC) with central and radial grooves shows small thermal resistance and good thermal performance under high heat fluxes. However, the groove parameters are difficult to optimize due to their coupling relationship and the lack of sound scientific ground. This paper addresses the issues by proposing an optimization method based on design of experiments (DOE) and response surface methodology (RSM) with the help of a developed decoupling strategy. In this method, a decoupling strategy inspired by the golden section rule is proposed to break the coupling relationship between groove parameters. Then DOE and RSM analyses are performed to provide data for single-objective and multi-objective optimization of groove parameters. Results indicate that, due to the decoupling strategy, the total number of sampling points is reduced by about 40% and the ratio of effective sampling points is increased by about 65.43% in DOE analysis. The influence of the groove parameters is nonmonotonic, and groove depth ( T ) has the greatest effect on the thermal hydraulic characteristics of CPVC, while the influence of central circular diameter ( D ) and groove width ( W ) is similar. The effect trend of the number of grooves ( N ) is contrary to that of W at small values due to the dramatic decrease of W . The thermal hydraulic performances can not reach the minimum or maximum value simultaneously, and the groove parameter configuration of D = 29 mm, W = 3.7 mm, T = 2.1 mm and N = 16 can be chosen as the optimal, leading to the decrease of the maximum temperature and the maximum temperature difference on the condensing surface, and the liquid pressure drop by 0.005 K, 0.015 K and 9.68%, respectively, compared with the initial design. The proposed method may pave a more objective and scientific alternative to design the structural parameters of CPVC.
MoreTranslated text
Key words
composite porous vapor chamber,coupling groove parameters
AI Read Science
Must-Reading Tree
Example
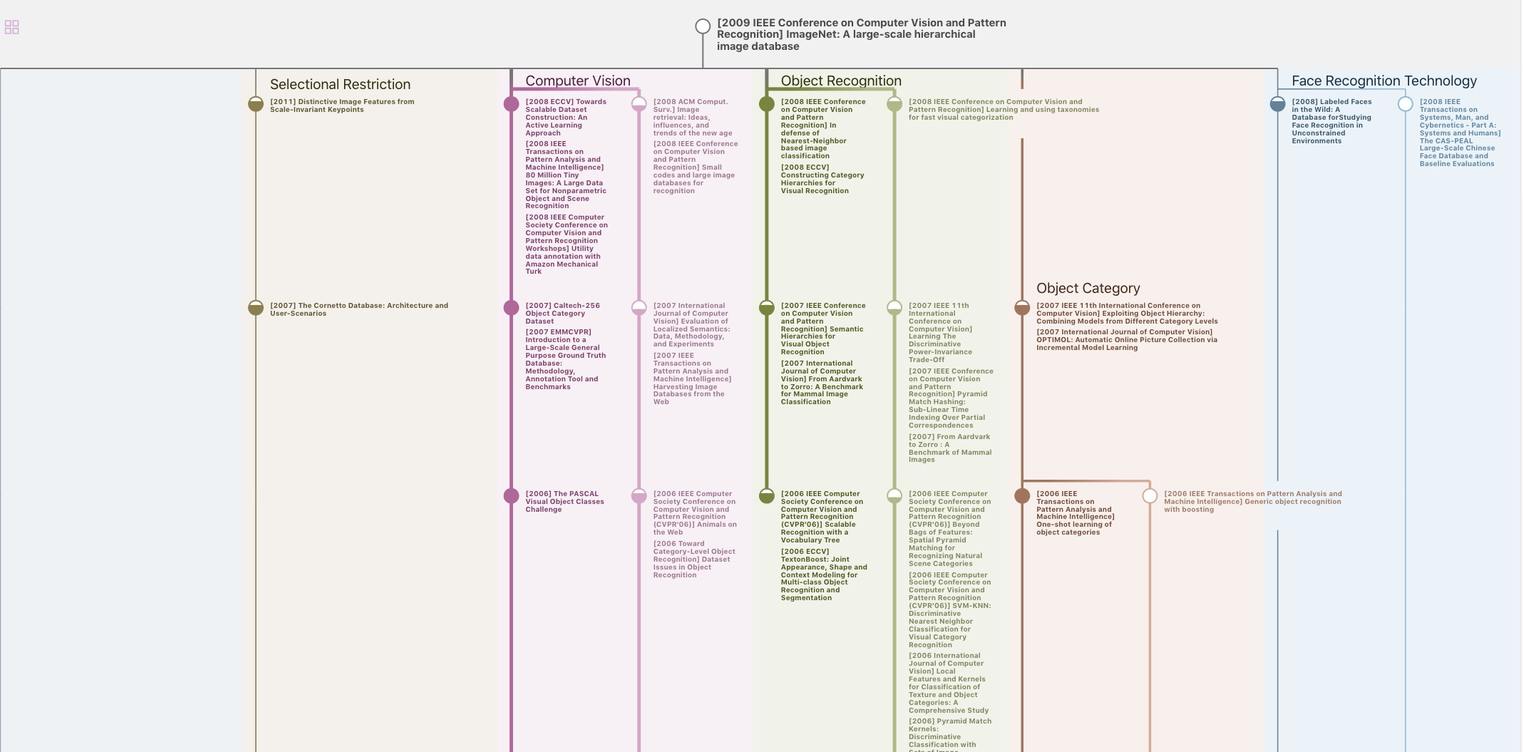
Generate MRT to find the research sequence of this paper
Chat Paper
Summary is being generated by the instructions you defined