Numerical and experimental investigation of HDPE hybrid propulsion with dual vortical-flow chamber designs
51st AIAA/SAE/ASEE Joint Propulsion Conference, 2015(2015)
Abstract
Hybrid rocket combustion has been often considered inefficient mainly due to its diffusion flame nature, which often leads to excessively lengthy chamber design that is an undesirable configuration to future application. Thus, how to shorten the chamber size but maintain high combustion efficiency becomes critical for the future research and development of hybrid rocket propulsion. In the present study, we would like to numerically and experimentally investigate a compact HDPE hybrid propulsion system with dual vortical-flow chamber design to possibly mitigate the problem. This design concept features counter-rotating injections of nitrous oxide into the chamber, which can increase the residence time and mixing as well as automatic roll control. In the present study, a 3-D computational model with finite-rate chemistry and radiative heat transfer effects with parallel computing are used to assess the mixing effectiveness and combustion efficiency of the present design. The internal ballistics and flame structure in hybrid rocket motors using HDPE fuel with nitrous oxide are investigated. A series of static-burn tests are performed to verify the designs and simulations. The preliminary results show that vacuum Isp of the tests for ~300 kgf of thrust can reach 270 seconds. Ground tests and simulations results of combustor with 1,000 and 3,000 kgf of thrust will be presented in the meeting.
MoreTranslated text
Key words
hdpe hybrid propulsion,vortical-flow
AI Read Science
Must-Reading Tree
Example
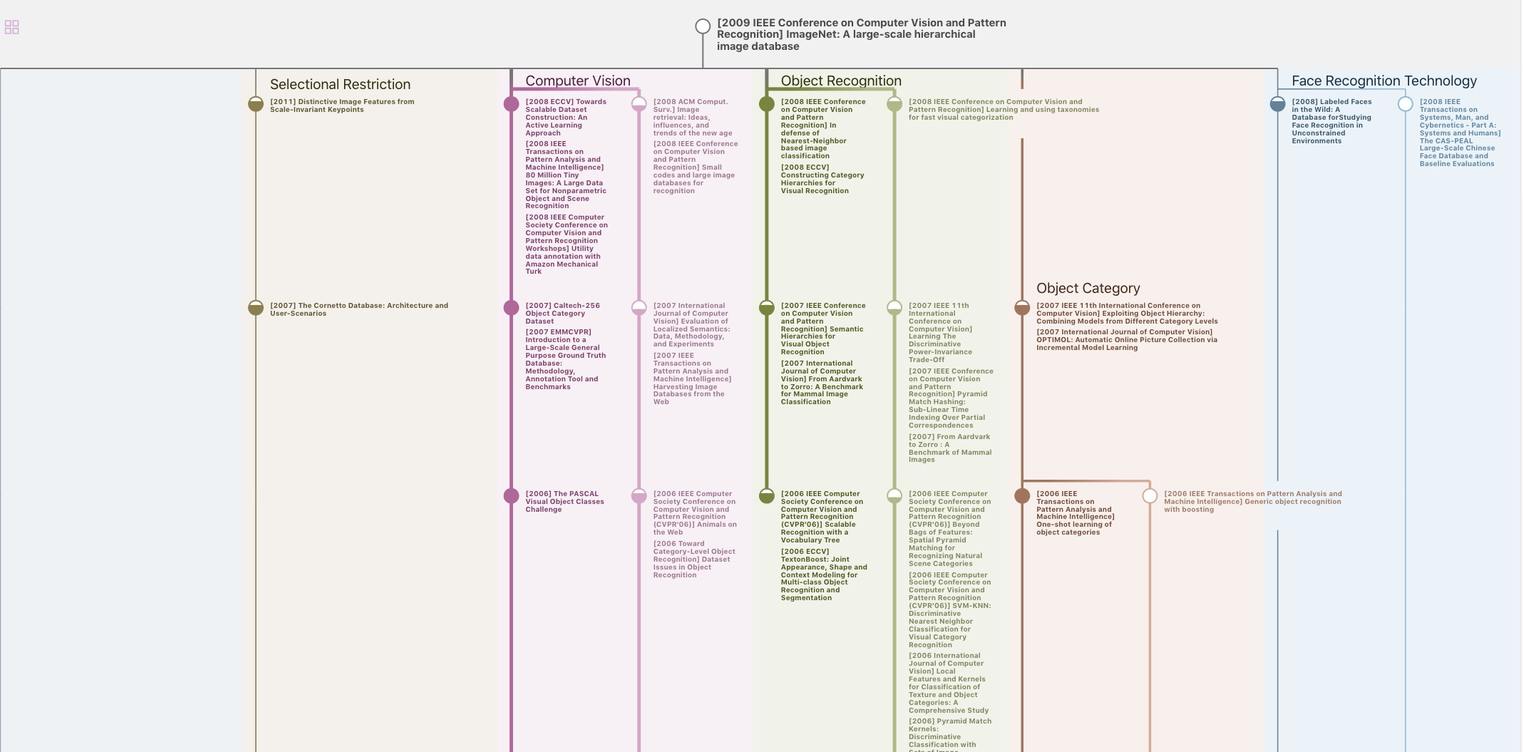
Generate MRT to find the research sequence of this paper
Chat Paper
Summary is being generated by the instructions you defined