Electromagnetic induction post heating to reduce nde delay times of welding in-service repairs
Volume 3: Operations, Monitoring, and Maintenance; Materials and Joining(2020)
Abstract
When a pipeline requires a repair, a pressure-containing steel sleeve or an emergency repair fitting is often fillet welded to the in-service pipe to return the pipeline to normal service conditions. During welding, the flowing product rapidly quenches the fillet weld, promoting the formation of high hardness and low ductility microstructures in the heat-affected zone. The rapid cooling rates also limit the mobility of diffusible hydrogen introduced from the welding electrodes. The hydrogen can be trapped in the weld metal and heat-affected zone and concentrated in specific locations throughout the weld based on the welding deposition sequence. Fillet welds also contain inherent locations of geometric stress concentration at the weld toes and root locations. The elevated hydrogen concentration in the in-service weld, combined with the geometrical stress concentrations at the location of crack-susceptible microstructures, can increase the likelihood of forming a hydrogen-induced crack Delayed non-destructive examination (NDE) is often employed to wait a sufficient time for any cracks to form so they can be detected. To reduce hydrogen concentration at the locations of stress concentration and NDE delay times, post-heating can be applied to the in-service weld Elevating the temperature within the weld can enable hydrogen diffusion and reducing the cracking propensity. The rapid heat removal due to flowing product requires post-heating techniques with high energy outputs that will not overheat the steel surfaces. Electromagnetic induced current (induction heating) methods can produce sufficient thermal energy in the electrically conductive steel pipe and sleeve. Coupled numerical finite element analysis (PEA) models were utilized to simulate various induction cable arrangements and thermal convection coefficients, representative of various pipeline products. The analysis of the induction heating arrangements for the studied thermal convection coefficient was conducted to achieve a minimum temperature of 120 degrees C in the fillet weld root and toes to enable sufficient thermal driving force for hydrogen diffusion while ensuring the pipe and sleeve surface temperature does not exceed 200 degrees C. An optimal induction heating procedure was found to which could achieve the target temperatures within a reasonable heating time such that NDE delay times of in-service welds can be reduced by 5-6 times.
MoreTranslated text
Key words
electromagnetic induction post heating,in-service
AI Read Science
Must-Reading Tree
Example
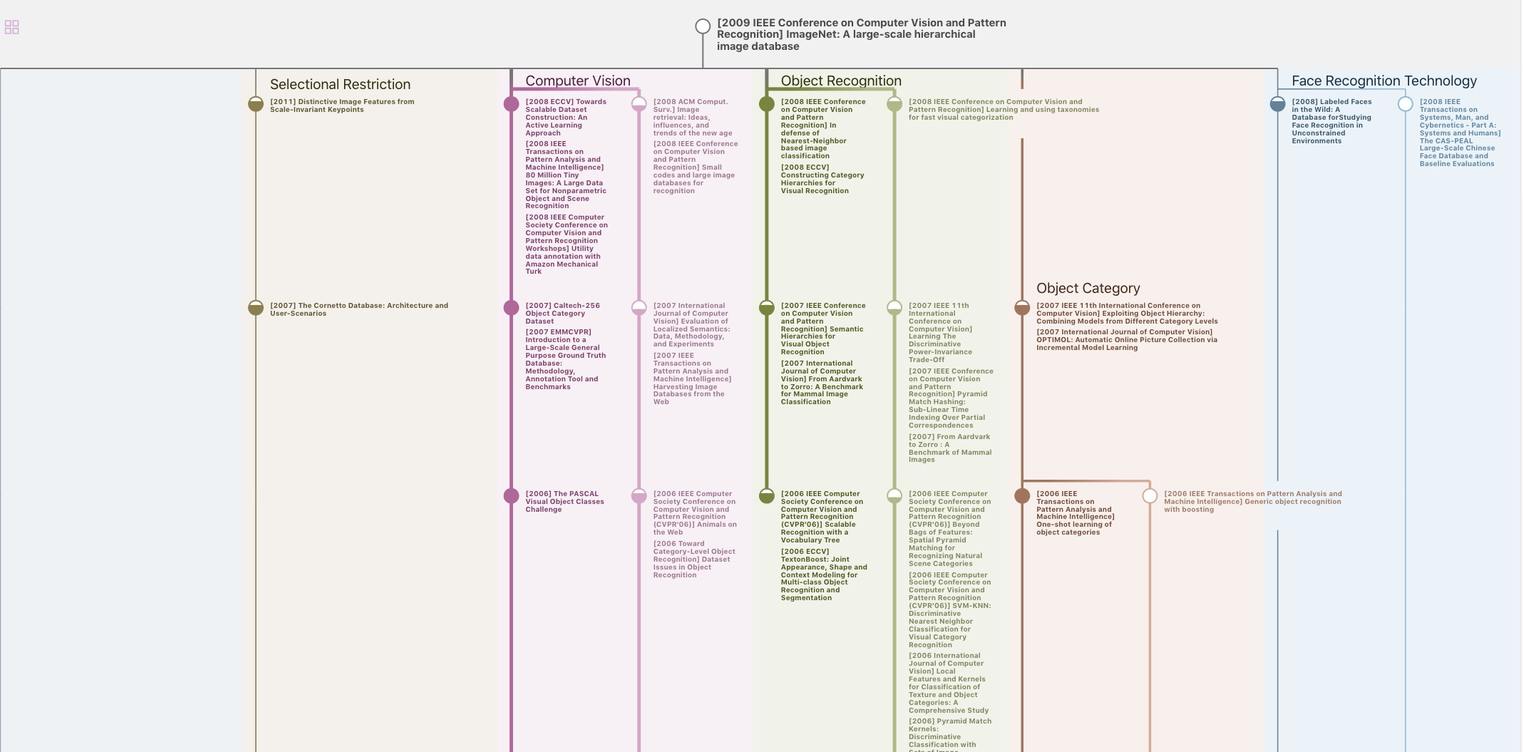
Generate MRT to find the research sequence of this paper
Chat Paper
Summary is being generated by the instructions you defined