Deformation Mechanisms in Tool–Workpiece Asperity Contact in Metal Forming
The minerals, metals & materials series(2021)
摘要
The contribution to friction stemming from dissipation of plastic energy is studied by numerical simulations and experiments. The geometrical setup consists of a single model asperity, which is first flattened against a tool with grooves on a smaller length scale. Relative, tangential sliding between the model asperity and the tool is induced subsequently until a steady state is reached. The flank angle of the grooves on the tool is varied. Comparison between the simulations and the experiments leads to validation of the simulations at low tool flank angles, while the current numerical implementation cannot handle the complicated flow around the tool grooves with a large flank angle. At low flank angles, the simulated tangential tool force is in agreement with experiments when keeping one determined friction factor. This proves that the change in tangential force, corresponding to a change in apparent friction factor, is only due to the dissipated energy from the plastic waves. The validated numerical model can be used to determine a wider range of apparent friction factors for strain hardening materials.
更多查看译文
关键词
Friction, Asperity contact, Plastic waves
AI 理解论文
溯源树
样例
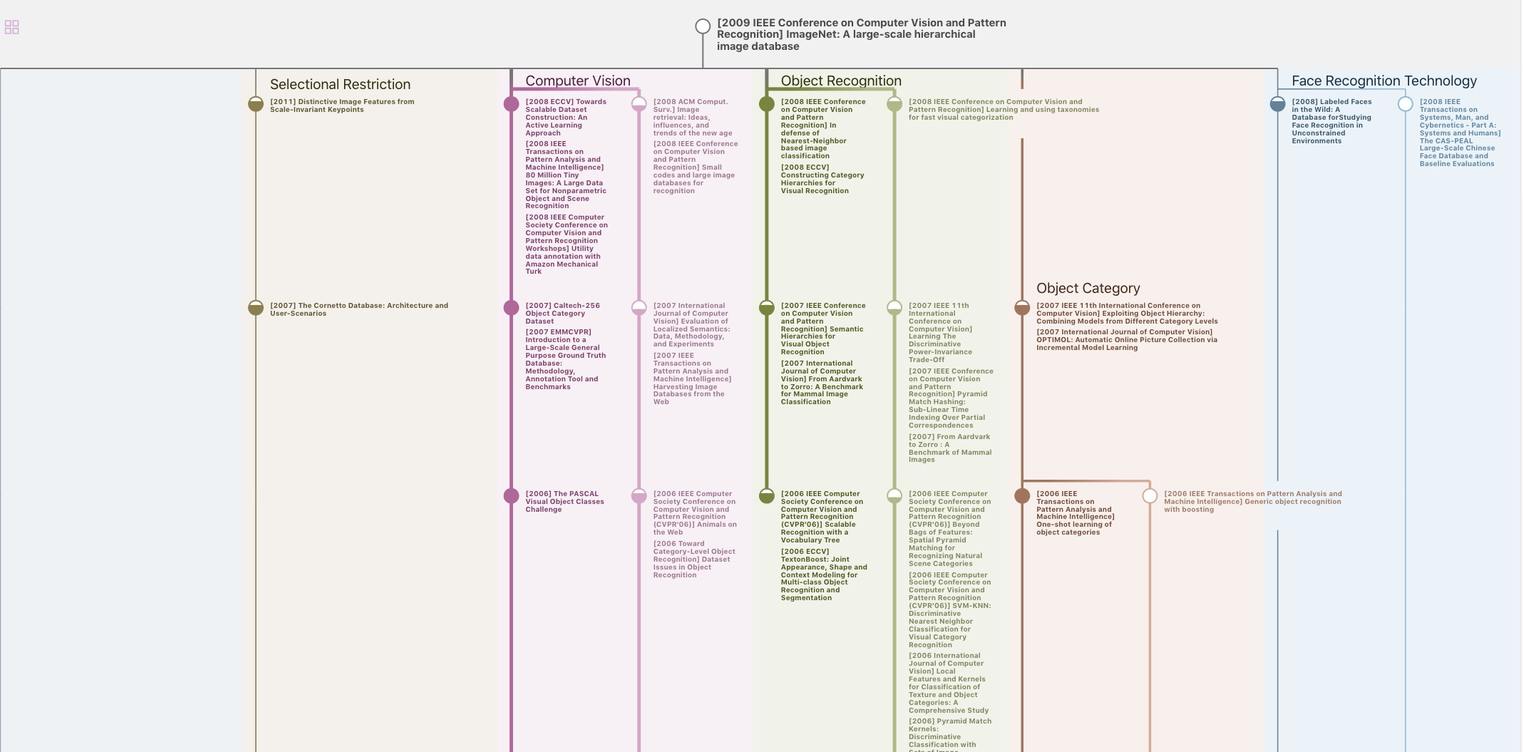
生成溯源树,研究论文发展脉络
Chat Paper
正在生成论文摘要