Analysis of the Flange Seal Groove Cracking in a Hydrocracking Reactor
Volume 1: Codes and Standards(2020)
Abstract
Abstract The hydrocracking reactor, serving at the high temperature and pressure and containing S and N elements in medium, are the key equipment in the hydrocracking plant. Due to the severe operational conditions, flange and nozzle cracking commonly occurs, especially for the seal groove between the flange and gasket. A cracked stainless flange is found in a hydrocracking reactor during parking and maintenance. Through a series of experiments including chemical composition, metallographic analysis, SEM and fracture analysis, the flange seal groove is analyzed. Under the long term operation at high temperature and high pressure, the σ phase is found in the flange material which will increase the cracking tendency. The hydrogen content measurement also proves that the material has the hydrogen embrittlement tendency. Hence, the combination of σ brittle phase and high stress causes the flange seal groove cracking. After cracking, hydrogen element enters the fracture, thus accelerating the crack growth. Therefore, in order to prevent the flange cracking, the assembly stress should be controlled in an appropriate range. If necessary, periodical inspection must be performed.
MoreTranslated text
Key words
flange groove, cracking, high stress, hydrocracking reactor, failure analysis
AI Read Science
Must-Reading Tree
Example
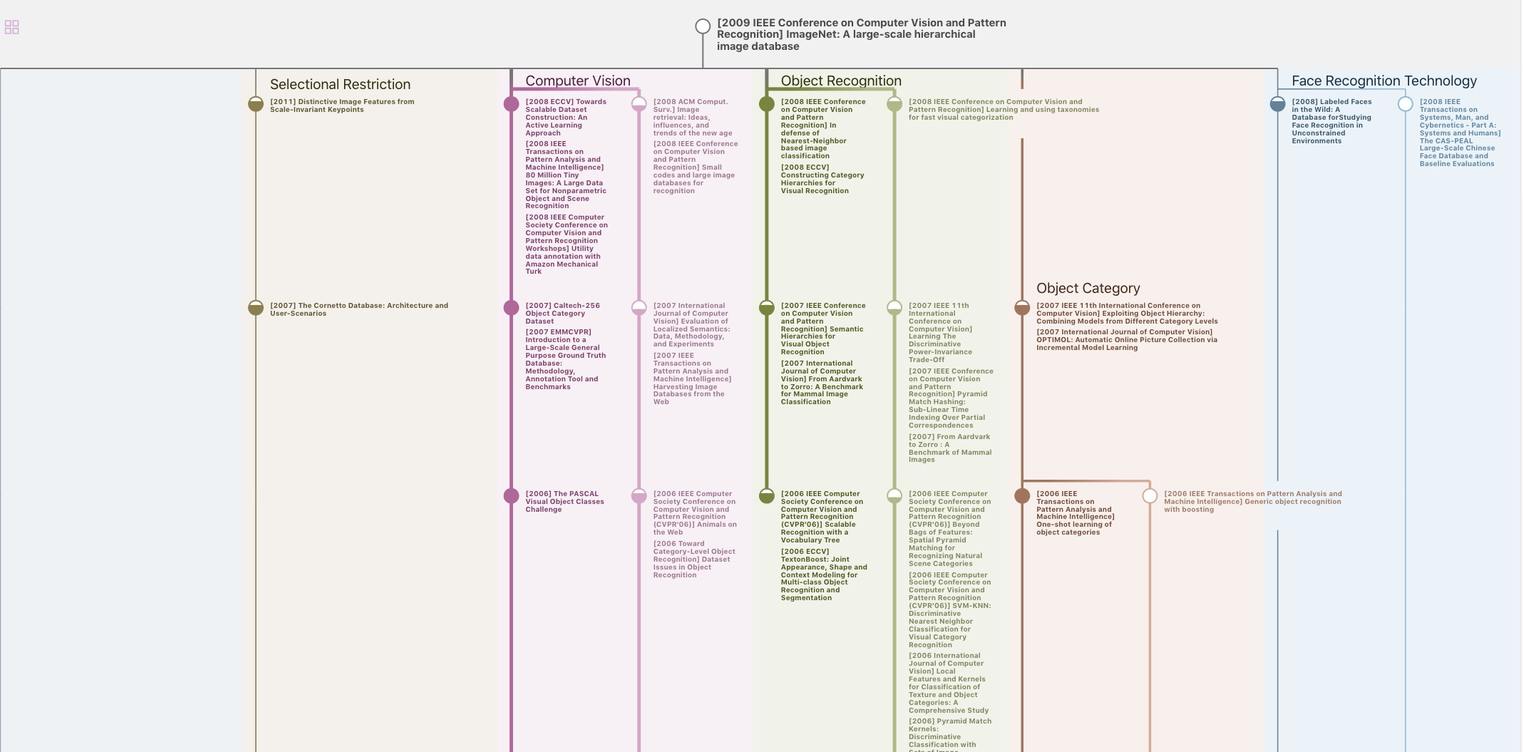
Generate MRT to find the research sequence of this paper
Chat Paper
Summary is being generated by the instructions you defined