Evolution Mechanism Of Subsurface Defect Structure In Particle Micro-Cutting Iron-Carbon Alloy Process
PROCEEDINGS OF THE INSTITUTION OF MECHANICAL ENGINEERS PART J-JOURNAL OF ENGINEERING TRIBOLOGY(2021)
Abstract
In order to explore the evolution mechanism of subsurface defect structure of iron-carbon alloy workpiece during abrasive flow machining, the molecular dynamics model of SiC particle micro-cutting iron-carbon alloys was established. The Common Neighbor Analysis and Dislocation Extraction Algorithm were applied to identify the crystal structure and lattice defects. The distribution and evolution of defect structure during micro-cutting were analyzed and discussed, and the removal mechanism of workpiece material during micro-cutting was revealed. The results show that dislocations, stacking faults, V-shaped dislocation loops, atomic clusters, and point defect structures were generated in the subsurface layer of the iron-carbon alloy workpiece during micro-cutting. Under the action of extrusion and friction of SiC particles, some atoms in the shear slip zone were largely displaced. The plastic deformation occurred on the workpiece and formed chips and machining surfaces. Some atoms extended into the interior of the workpiece material, resulting in subsurface defect structure. After the completion of particle micro-cutting, some defect structures of the subsurface layer disappeared, and some defect structures remained in the subsurface of the workpiece in a certain form, forming a subsurface defect layer.
MoreTranslated text
Key words
Molecular dynamics, micro-cutting, iron-carbon alloy, subsurface defect, evolution mechanism
AI Read Science
Must-Reading Tree
Example
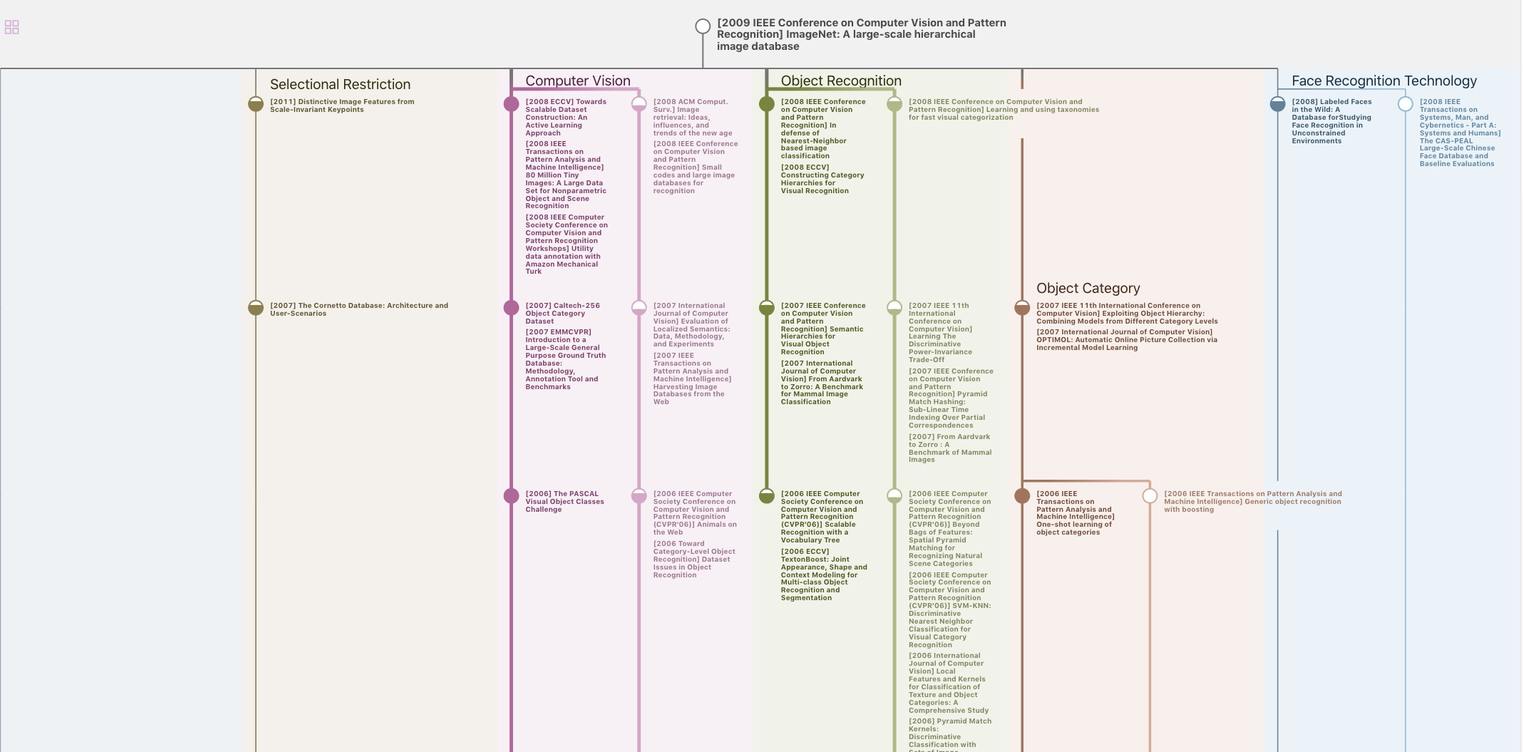
Generate MRT to find the research sequence of this paper
Chat Paper
Summary is being generated by the instructions you defined