Experimental study on surface integrity and subsurface damage of fused silica in ultra-precision grinding
The International Journal of Advanced Manufacturing Technology(2021)
摘要
The surface quality and subsurface damage (SSD) distribution achieved with a fine-grained grinding wheel under different depth-of-cut and cutting speed is experimentally studied. The ground surface roughness (SR) is investigated via white light interferometry and expressed in terms of four typical roughness values (PV, RMS, R z , and R a ). The SSD is characterized by the magnetorheological finishing (MRF) spot method and transmission electron microscopy. The results show that brittle-ductile surfaces and ductile-like surfaces are generated during ultra-precision grinding. Largely due to plastic flow removal, fracture defects such as fractured pits and grinding streaks on the ground surface can be mitigated. Instead, a ductile-like surface covered with grinding streaks is found. When the depth-of-cut decreases from 4 to 1 μm, the SR and SSD depth decreases from PV 1.34 μm, R a 15.23 nm, R z 0.94 μm, RMS 22.24 nm, and SSD 6.1 μm to PV 0.51 μm, R a 5.07 nm, R z 0.24 μm, RMS 6.70 nm, and SSD 1.2 μm. In addition, when the cutting speed increases from 3.9 to 23.4 m/s, the SR and SSD depth decreases from PV 1.03 μm, R a 15.01 nm, R z 0.82 μm, RMS 21.43 nm, and SSD 5.6 μm to PV 0.12 μm, R a 3.17 nm, R z 0.07 μm, RMS 4.65 nm, and SSD 0.003 μm. Moreover, the material removal mechanism under different grinding parameters is revealed by calculating undeformed chip thickness, and the mechanism of surface morphology and subsurface crack produced in brittle-ductile mode is analyzed. A linear relationship between the SR and SSD depth is in accord with the formula SSD = 0.41R a −0.68 for brittle-ductile surfaces.
更多查看译文
关键词
Fused silica,Ultra-precision grinding,Ductile material removal,Surface integrity,Subsurface damage
AI 理解论文
溯源树
样例
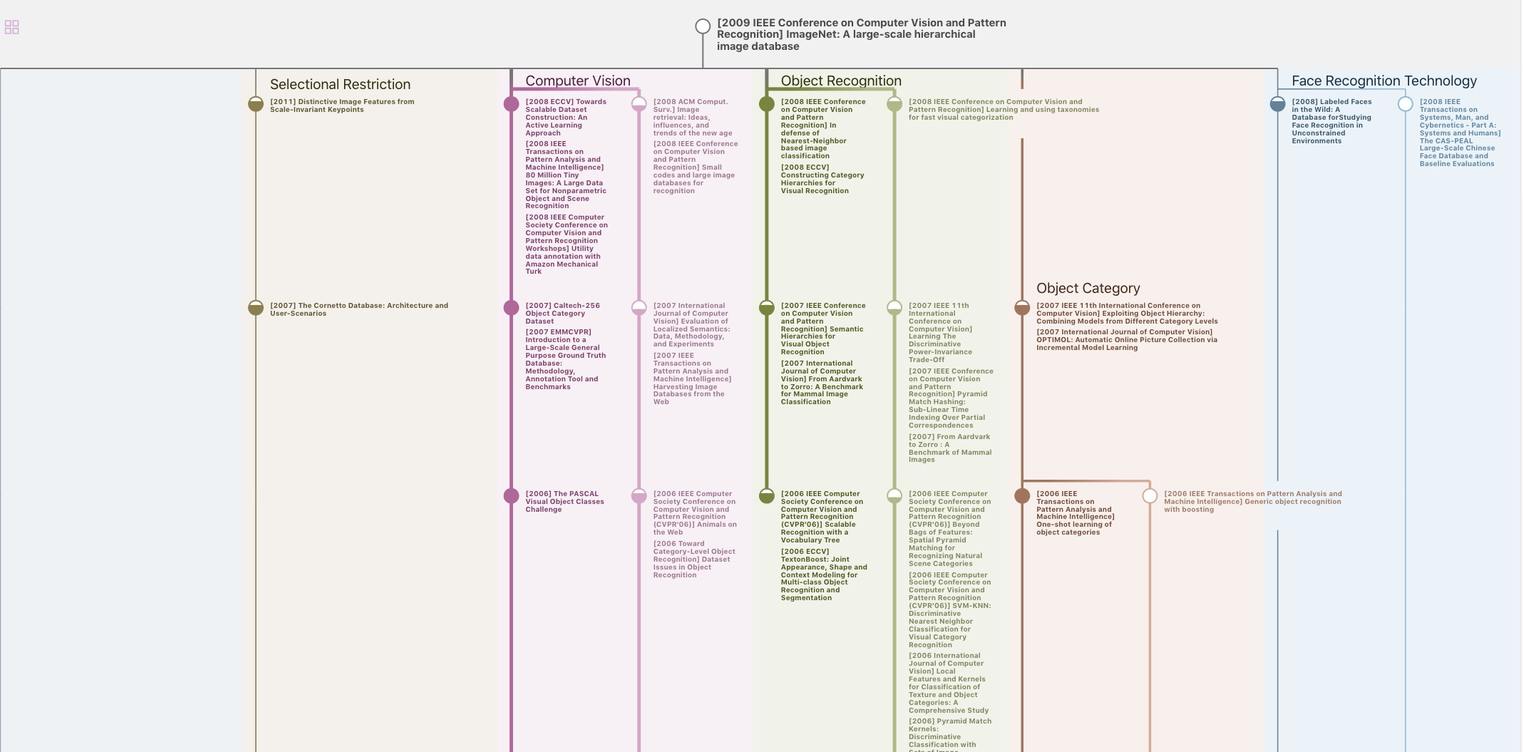
生成溯源树,研究论文发展脉络
Chat Paper
正在生成论文摘要