Corrosion Resistance Of Thermal-Pulsed Inconel 625 Mig/Mag Weld Overlays
SURFACE TOPOGRAPHY-METROLOGY AND PROPERTIES(2021)
Abstract
The deposition of Inconel 625 can be performed by MIG/MAG (Metal Inert Gas/Metal Active Gas) welding process. Despite resulting in larger dilution than other welding methods, MIG/MAG has the advantage of a high production capacity. The present work aimed to study the use of a variant of the MIG/MAG process known as MIG/MAG Double Pulse (MIG/MAG-DP), where the variation of the welding current in the form of pulses can alter the microstructure of the deposits. The effects on corrosion resistance of the macrogeometry and microstrucure of Inconel 625 weld overlays onto low carbon steel substrates were evaluated via cyclic potentiodynamic polarization corrosion tests under two test temperatures (25 degrees C and 60 degrees C). The results showed that the MIG/MAG-DP process produced weld overlays with higher dilution (almost twice of that observed for conventional MIG/MAG). Moreover, MIG/MAG-DP resulted in more refined microstructure; the spacing between the dendritic secondary arms was around 49% smaller than for conventional MIG/MAG. This had a negative impact on the corrosion resistance of the deposits at both temperatures and increased the susceptibility of the deposits to crevice corrosion. Therefore, the use of MIG/MAG-DP, although often a positive strategy in welding operations, is not a good route for depositing high corrosion resistance deposits.
MoreTranslated text
Key words
MIG, MAG, microstructure, welding, secondary dendritic arm spacing, cyclic potentiodynamic polarization corrosion tests
AI Read Science
Must-Reading Tree
Example
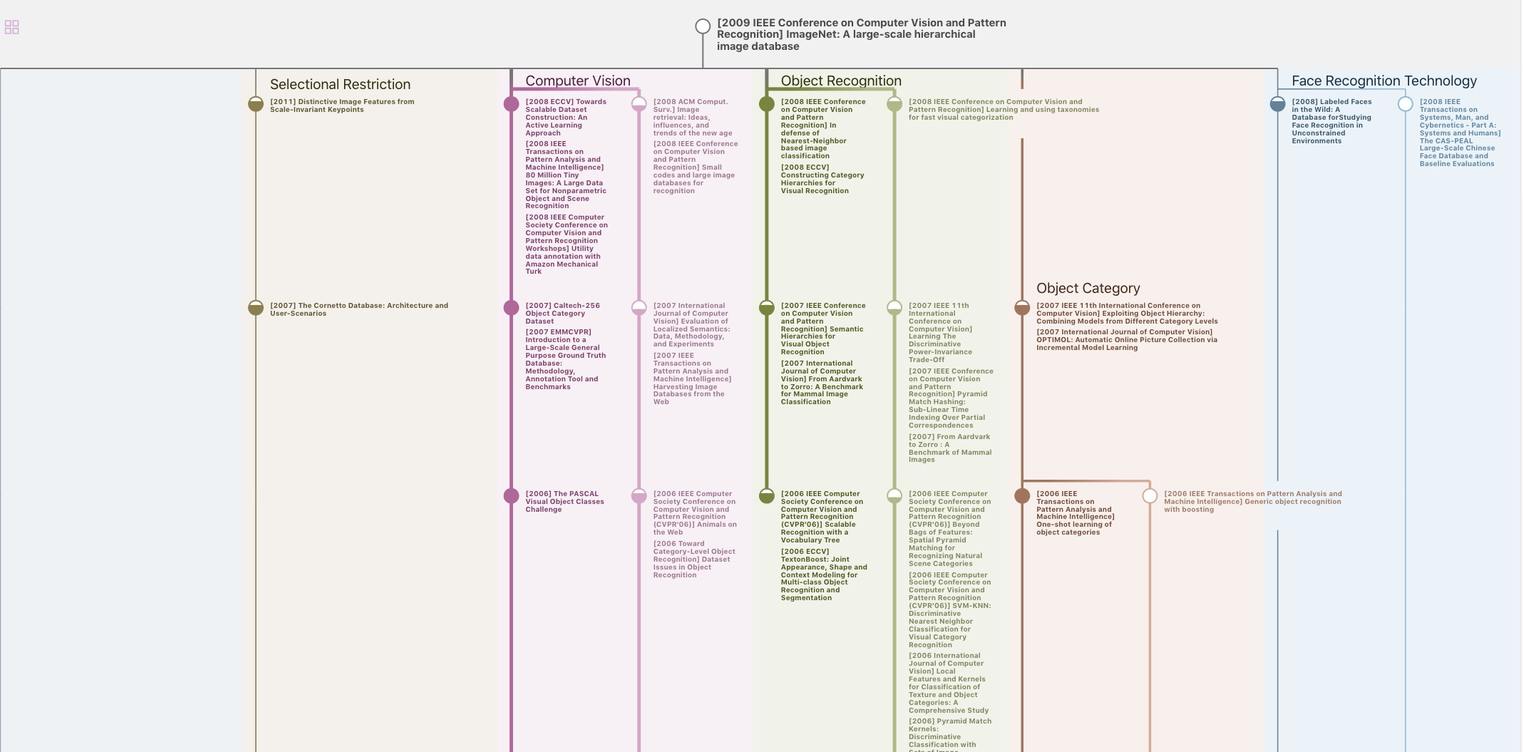
Generate MRT to find the research sequence of this paper
Chat Paper
Summary is being generated by the instructions you defined