Cad-Based Adjoint Optimization Of The Stresses In A Radial Turbine
PROCEEDINGS OF THE ASME TURBO EXPO: TURBINE TECHNICAL CONFERENCE AND EXPOSITION, 2017, VOL 2C(2017)
Abstract
The design optimization of turbomachinery components has witnessed an increased attention in last decade, and is currently used in many companies in the daily design cycle. The adjoint method proves to have the highest potential in this field, however, has still two major shortcomings before its full potential can be used: 1) the shape is mainly parameterized by its grid and the connection to the CAD model is lost, and 2) the optimization process includes only aerodynamic performance and neglects stress and vibration requirements. Within this paper a methodology is developed to include stress calculations into a gradient-based framework, which requires the differentiation of a stress analysis tool. To allow combining the sensitivities from the structural model with those from the aero performance, the CAD model is used for parameterizing the shape, effectively defining a parametrization that controls both the fluid and solid domain that remain linked to each other without creating voids between both models.The method is tested on a radial turbine test case in which the meridional layout is optimized to reduce the maximum von Mises stresses in the material. The results demonstrate a significant reduction in stress concentrations with a limited computational cost.
MoreTranslated text
Key words
optimization,stresses,cad-based
AI Read Science
Must-Reading Tree
Example
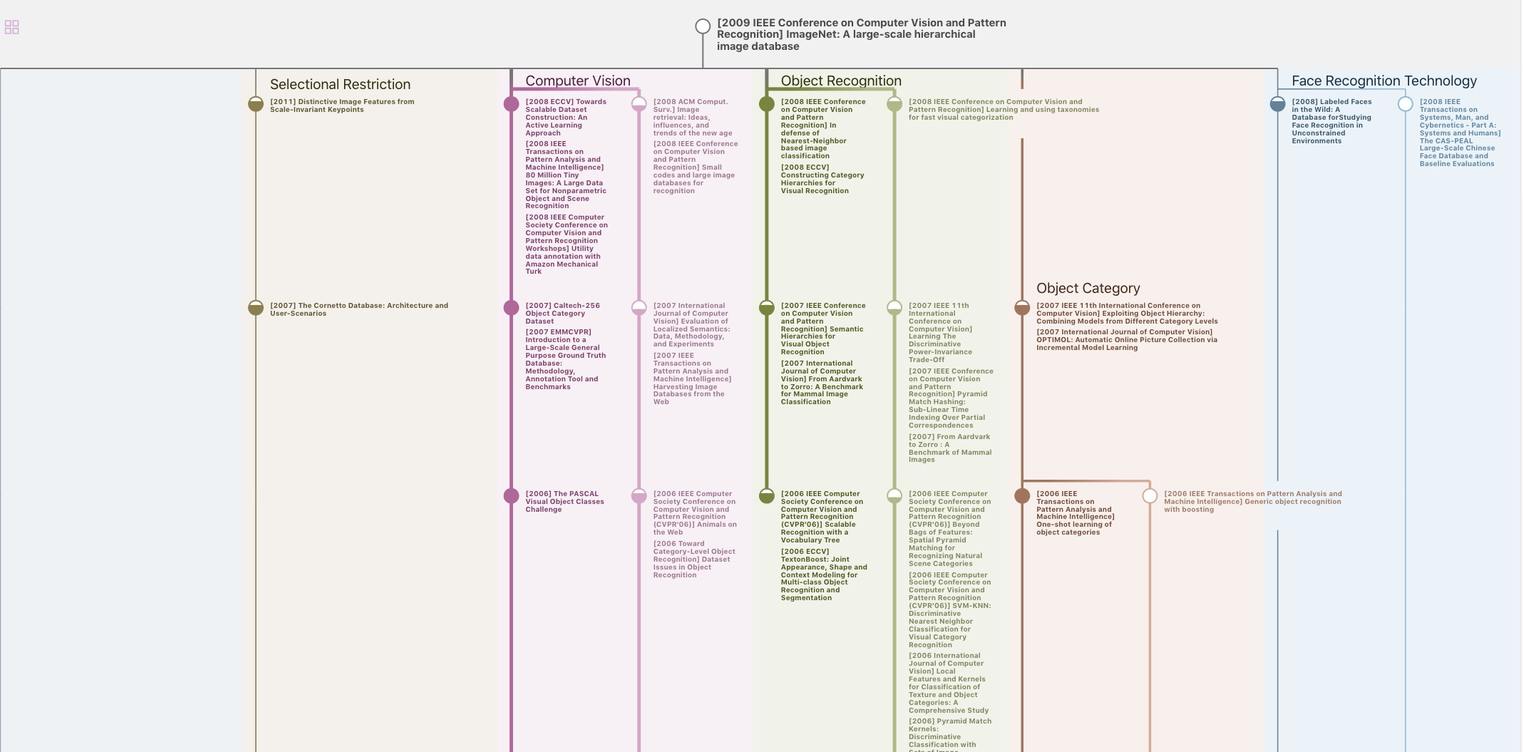
Generate MRT to find the research sequence of this paper
Chat Paper
Summary is being generated by the instructions you defined