Calculation Of The Collision-Free Printing Workspace For Fully-Constrained Cable-Driven Parallel Robots
PROCEEDINGS OF THE ASME INTERNATIONAL DESIGN ENGINEERING TECHNICAL CONFERENCES AND COMPUTERS AND INFORMATION IN ENGINEERING CONFERENCE, 2018, VOL 5B(2018)
摘要
Using fully-constrained cable robots as manipulators for 3D-printing, there is the risk of collisions between the cables and the printing part.This paper presents a method to calculate the shape of the workspace volume within which a part can be printed without such collisions. The presented method is based on the fact that the printing part is produced in a sequence of horizontal layers. The areas occupied by the cables in the layers are scaled similar mappings of the cross-sections of the printing part. There is no collision if the 2D-shapes occupied by the cables in the printing layer do not overlap with the cross-sections of the printing part in the same layer. A procedure to find the largest printable 2D-shapes within the class of parallelograms for each layer is developed. The maximum printable 3D-volume is then given by stacking the 2D-shapes of each layer. Figures show the results of the method applied on the cable robot IPAnema 3. Finally, a guideline for the design of fully-constrained cable robots to maximize their printable volume is given.
更多查看译文
AI 理解论文
溯源树
样例
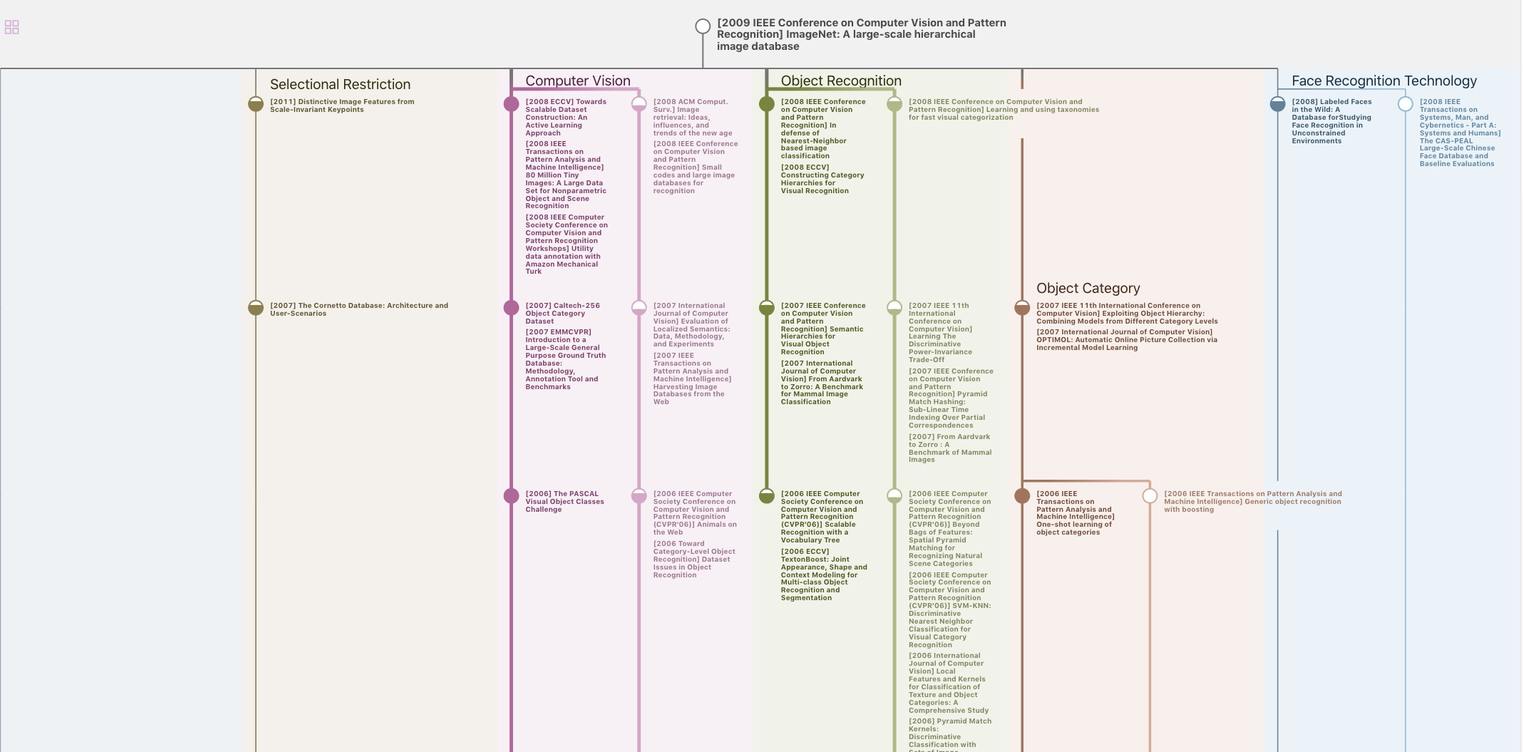
生成溯源树,研究论文发展脉络
Chat Paper
正在生成论文摘要