Modelling Droplet Heat And Mass Transfer In Aero-Engine Bearing Chambers
PROCEEDINGS OF THE ASME TURBO EXPO: TURBOMACHINERY TECHNICAL CONFERENCE AND EXPOSITION, 2019, VOL 2C(2019)
摘要
The oil inside aeroengine bearing chambers can be found in many forms, including droplets which interact with the core airflow. The ability to model such bearing chambers computationally is desirable and thus a better understanding of the evaporation process of oil droplets is of great interest. Previous studies have analyzed the flow of isothermal droplets in bearing chambers. However, further investigation is needed into the heating of droplets in the highly rotating core region. This will enable designers to evaluate the behavior of droplets in a chamber and the likelihood that they will evaporate. The aim of this research is to analyze the oil droplet evaporation process under aeroengine bearing chamber representative conditions. An ultimate goal is the ability to predict the oil -air heat and mass transfer in the core flow region, as well as to develop an understanding of the flow inside a droplet, and how this affects evaporation. This latter is important as it has not been studied before. This paper presents the results of a numerical study of the evaporation process of a single droplet under bearing chamber temperature and air flow conditions. The two-phase flow is simulated using ANSYS Fluent with the volume of fluid approach and the evaporation process with the "D -square law". First, the modelling approach is validated against previous experimental and numerical analysis of fuel droplets in an air flow with heat transfer. The simulation results were in excellent agreement with a benchmarking data set. The validated approach is then applied for investigation to smaller, bearing chamber representative droplets of an oil base stock used in jet engines. The oil evaporation rate was quantified as well as the evolution of droplet diameter, which revealed the effect of different air velocities and temperatures on the droplet. The extent to which evaporation rate increased with air velocity and temperature is quantified. It is concluded that droplets of initial diameters less than 200 m that remain in the chamber core region for more than 0.3s are likely to evaporate completely. This study allows us to estimate droplet heat and mass transfer and the associated phase change in a bearing chamber. It also provides best practice to predict the performance of small droplets under the effects of high temperature and velocity convective air flows. In future work this methodology will be applied in simulations in a representative bearing chamber to predict how the cooling process is affected by oil evaporation.
更多查看译文
关键词
droplet heat,mass transfer,aero-engine
AI 理解论文
溯源树
样例
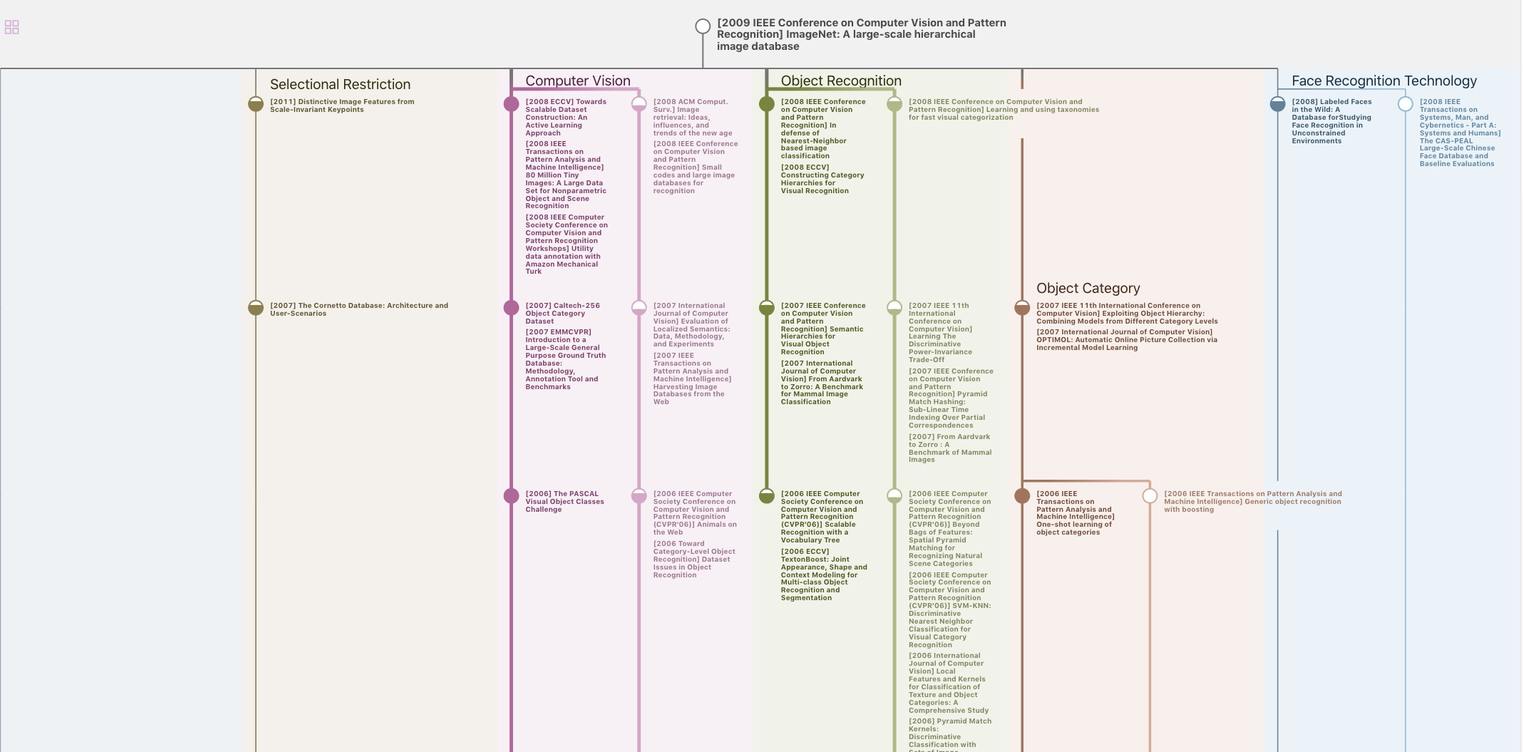
生成溯源树,研究论文发展脉络
Chat Paper
正在生成论文摘要