Computational Assessment Of A 3-Stage Axial Compressor Which Provides Airflow To The Nasa 11-By 11-Foot Transonic Wind Tunnel, Including Design Changes For Increased Performance
PROCEEDINGS OF THE ASME TURBO EXPO: TURBINE TECHNICAL CONFERENCE AND EXPOSITION, 2017, VOL 2A(2017)
Abstract
New rotor blades are to be fabricated for the 24 foot diameter, 3-stage axial compressor which provides airflow in the 11- by 11-Foot Transonic Wind Tunnel Facility at NASA Ames Research Center in Moffett Field, California. This presents an opportunity to increase the peak Mach number capability of the tunnel by redesigning the compressor for increased pressure ratio. Simulations of the existing compressor from the APNASA CFD code were compared to performance predictions from the HT0300 turbomachinery design code and to compressor performance data taken during a 1997 facility checkout test. It was found that the existing compressor is operating beyond the stability limits predicted by the analysis tools. Additionally, CFD simulations were sensitive to endwall leakages associated with stator button gaps and under-stator-platform flow recirculation. When stator button leakage and cavity recirculation were modeled, pressure rise at design point increased by over 25% due to a large reduction in aerodynamic blockage at the hub. After improving the CFD model and validating the tools against test data, a new design is proposed which achieved 10.5% increased total pressure rise and substantially reduced diffusion factors.
MoreTranslated text
Key words
airflow,wind
AI Read Science
Must-Reading Tree
Example
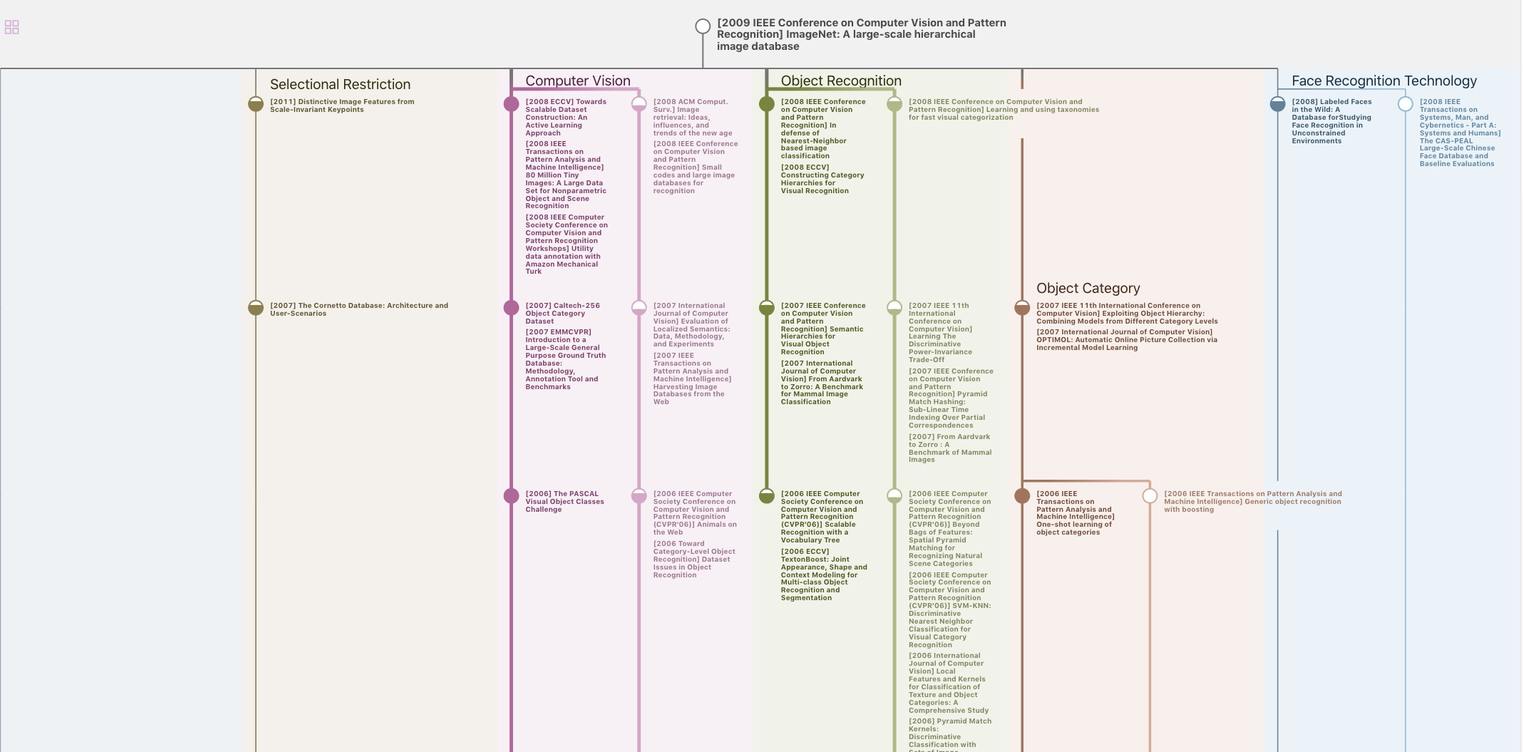
Generate MRT to find the research sequence of this paper
Chat Paper
Summary is being generated by the instructions you defined