Simulating In-Service Welding Of Hot-Tap Branches To Quantify The Effect Of Geometry On Level Of Restraint
PROCEEDINGS OF THE 12TH INTERNATIONAL PIPELINE CONFERENCE, 2018, VOL 3(2018)
摘要
Economic and environmental incentives encourage operators to maintain pipeline operation during repair and maintenance procedures including hot-tap branch fitting installation onto pipelines. Welding onto a liquid-filled pipeline induces accelerated cooling of the weld and heat affected zone (HAZ), increasing the propensity for cracking. In-service welding codes and due diligence requires that several key factors be considered during the design of an in-service welding procedure specification for its intended purpose. The level of restraint (LoR) imposed by the geometry, material, or dimensional differences of the branch compared to the run pipe has also been shown to be a significant contributor to cracking. Finite element analysis (FEA) was utilized to investigate the geometric effects of an in-service weld procedure to approximate the LoR of hot-tap branch installation. The LoR was quantified and compared by simulating multi-pass weld sequences on two configurations: a branch-on-pipe (BoP) configuration of various dimensions and a configuration using perpendicular plates (PP) that has been used as an alternative to the branch-on-pipe configuration. The highest LoR, as measured by transverse tensile stress at the fillet weld toe, was the branch-on-pipe configuration with the largest branch wall thickness, the smallest branch diameter, the largest run pipe diameter, and the largest run pipe wall thickness. FEA modeling revealed that the PP configuration has lower LoR, thus it is not recommended to use for simulating in-service branch weld procedures.
更多查看译文
关键词
in-service,hot-tap
AI 理解论文
溯源树
样例
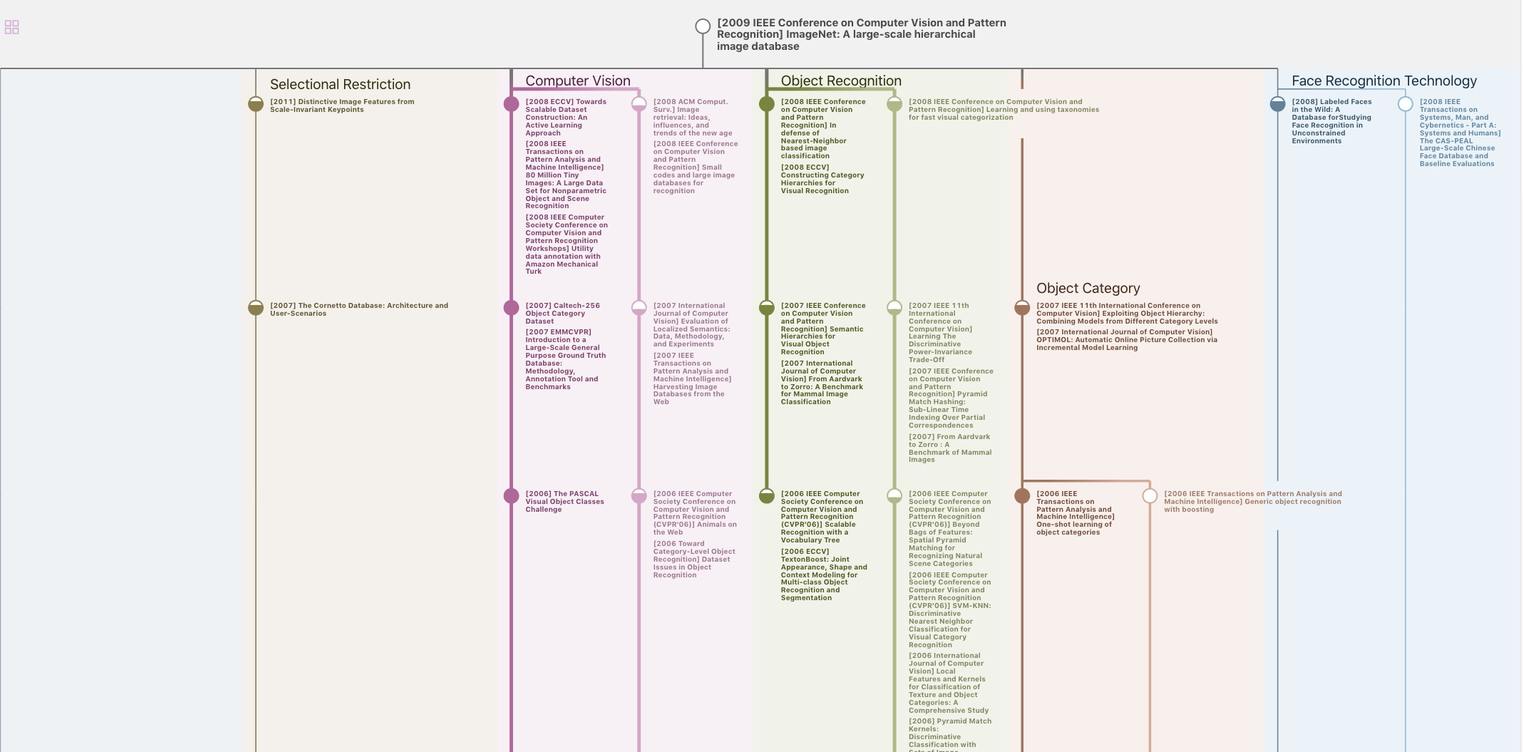
生成溯源树,研究论文发展脉络
Chat Paper
正在生成论文摘要