Microstructural Characterization of Laser Weld of Hot-Stamped Al-Si Coated 22mnb5 and Modification of Weld Properties by Hybrid Welding
MATERIALS(2021)
Abstract
The presence of Al-Si coating on 22MnB5 leads to the formation of large ferritic bands in the dominantly martensitic microstructure of butt laser welds. Rapid cooling of laser weld metal is responsible for insufficient diffusion of coating elements into the steel and incomplete homogenization of weld fusion zone. The Al-rich regions promote the formation of ferritic solid solution. Soft ferritic bands cause weld joint weakening. Laser welds reached only 64% of base metal’s ultimate tensile strength, and they always fractured in the fusion zone during the tensile tests. We implemented hybrid laser-TIG welding technology to reduce weld cooling rate by the addition of heat of the arc. The effect of arc current on weld microstructure and mechanical properties was investigated. Thanks to the slower cooling, the large ferritic bands were eliminated. The hybrid welds reached greater ultimate tensile strength compared to laser welds. The location of the fracture moved from the fusion zone to a tempered heat-affected zone characterized by a drop in microhardness. The minimum of microhardness was independent of heat input in this region.
MoreTranslated text
Key words
22MnB5,laser welding,hybrid welding,cooling rate,tensile strength,microstructure
AI Read Science
Must-Reading Tree
Example
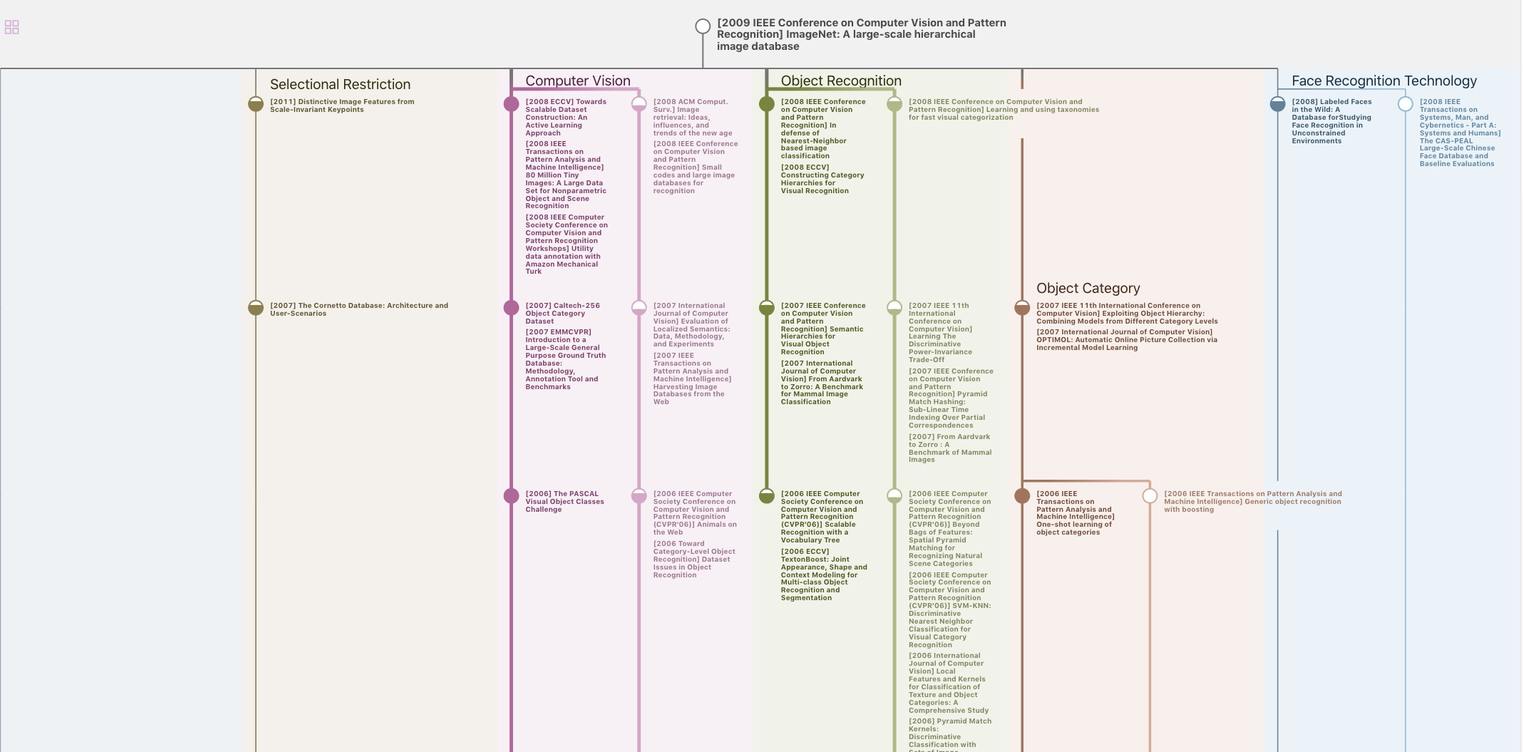
Generate MRT to find the research sequence of this paper
Chat Paper
Summary is being generated by the instructions you defined