Driving investments in ore beneficiation and scrap upgrading to meet an increased demand from the direct reduction-EAF route
Mineral Economics(2021)
Abstract
The pressure on the steel industry to reduce its carbon footprint has led to discussions to replace coke as the main reductant for iron ore and turn to natural gas, bio-syngas or hydrogen. Such a major transition from the blast furnace-basic oxygen furnace route, to the direct reduction-electric arc furnace route, for steel production would drastically increase the demand for both suitable iron ore pellets and high-quality scrap. The value for an EAF plant to reduce the SiO 2 content in DRI by 2 percentage points and the dirt content of scrap by 0.3 percentage points Si was estimated by using the optimization and calculation tool RAWMATMIX®. Three plant types were studied: (i) an integrated plant using internal scrap, (ii) a plant using equal amounts of scrap and DRI and (iii) a plant using a smaller fraction of DRI in relation to the scrap amount. Also, the slag volume for each plant type was studied. Finally, the cost for upgrading was estimated based on using mainly heuristic values. A conservative estimation of the benefit of decreasing the silica content in DRI from 4 to 2% is 20 USD/t DRI or 15 USD/t DR pellets and a conservative figure for the benefit of decreasing the dirt in scrap by 0.3 percentage points Si is 9 USD/t scrap. An estimate on the costs for the necessary ore beneficiation is 2.5 USD/t pellet concentrate and for a scrap upgrade, it is 1-2 USD/t scrap.
MoreTranslated text
Key words
DRI,Ore beneficiation,Scrap upgrading,Slag volume
AI Read Science
Must-Reading Tree
Example
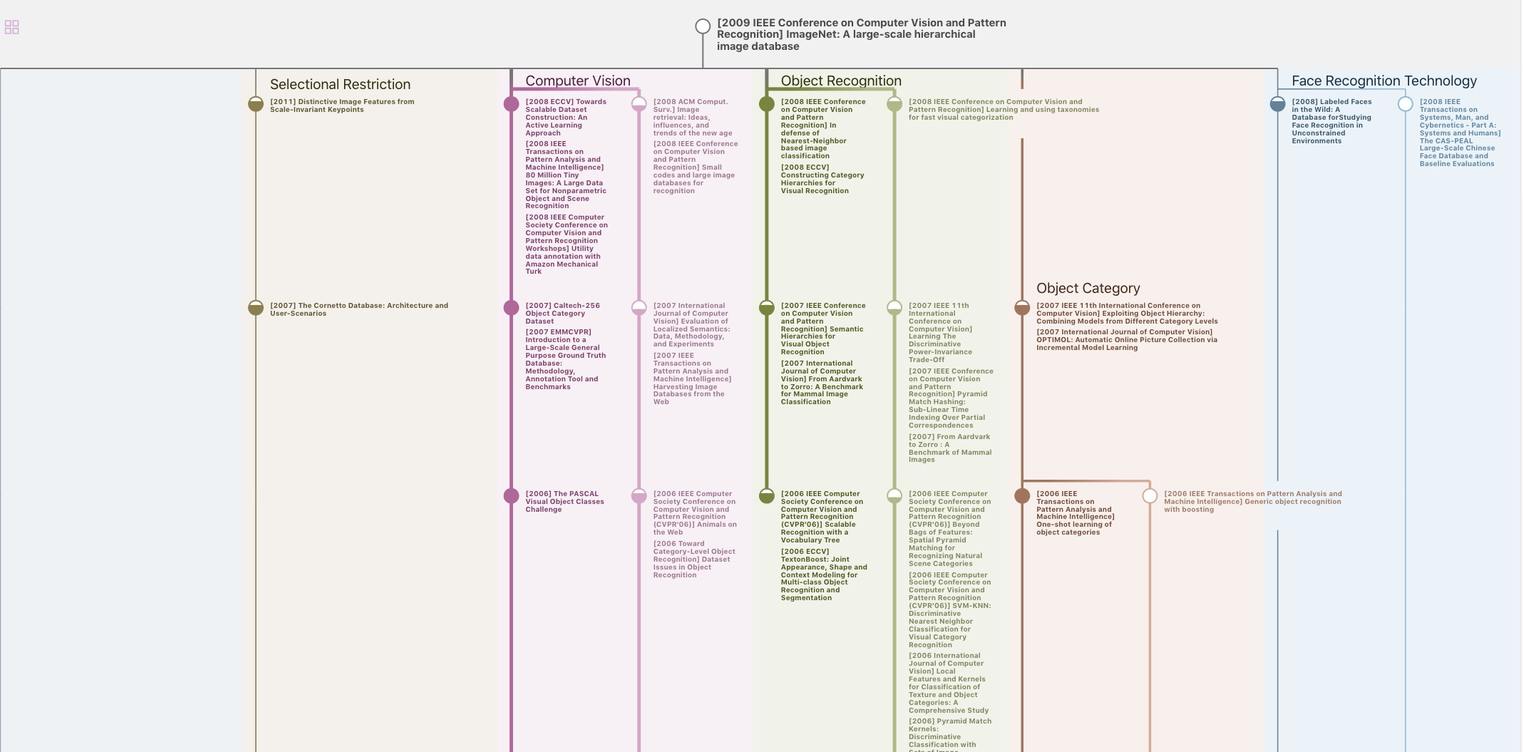
Generate MRT to find the research sequence of this paper
Chat Paper
Summary is being generated by the instructions you defined