Double Diaphragm Forming Simulation Using A Global-To-Local Modelling Strategy For Detailed Defect Detection In Large Structures
COMPOSITES PART A-APPLIED SCIENCE AND MANUFACTURING(2021)
Abstract
A global-to-local modelling strategy is presented based on a sub-modelling approach to predict the formation of macroscale defects in bi-axial non-crimp fabric (NCF) during double diaphragm forming (DDF). A full-scale global simulation is initially performed using a coarse membrane element mesh (5 mm edge length) to locate areas containing potential defects. Refined local simulations are subsequently performed using high a fidelity shell-element mesh (1 mm edge length) to explicitly predict the shape of forming induced defects in these areas, using boundary conditions derived from the global simulation. The methodology is validated by forming a fabric blank over a generic geometry comprising local changes in cross-sectional shape, in order to invoke forming induced defects in a controlled manner. The defective areas predicted by the simulation agree well with the locations observed from the forming experiments, including the shape and length of surface visible defects such as fabric wrinkling and bridging. The CPU time for this two-stage approach is shown to be approximately 13% compared to the CPU time required for the high fidelity full-scale model for the same geometry.
MoreTranslated text
Key words
Fabrics/textiles, Defects, Finite element analysis (FEA), Forming
AI Read Science
Must-Reading Tree
Example
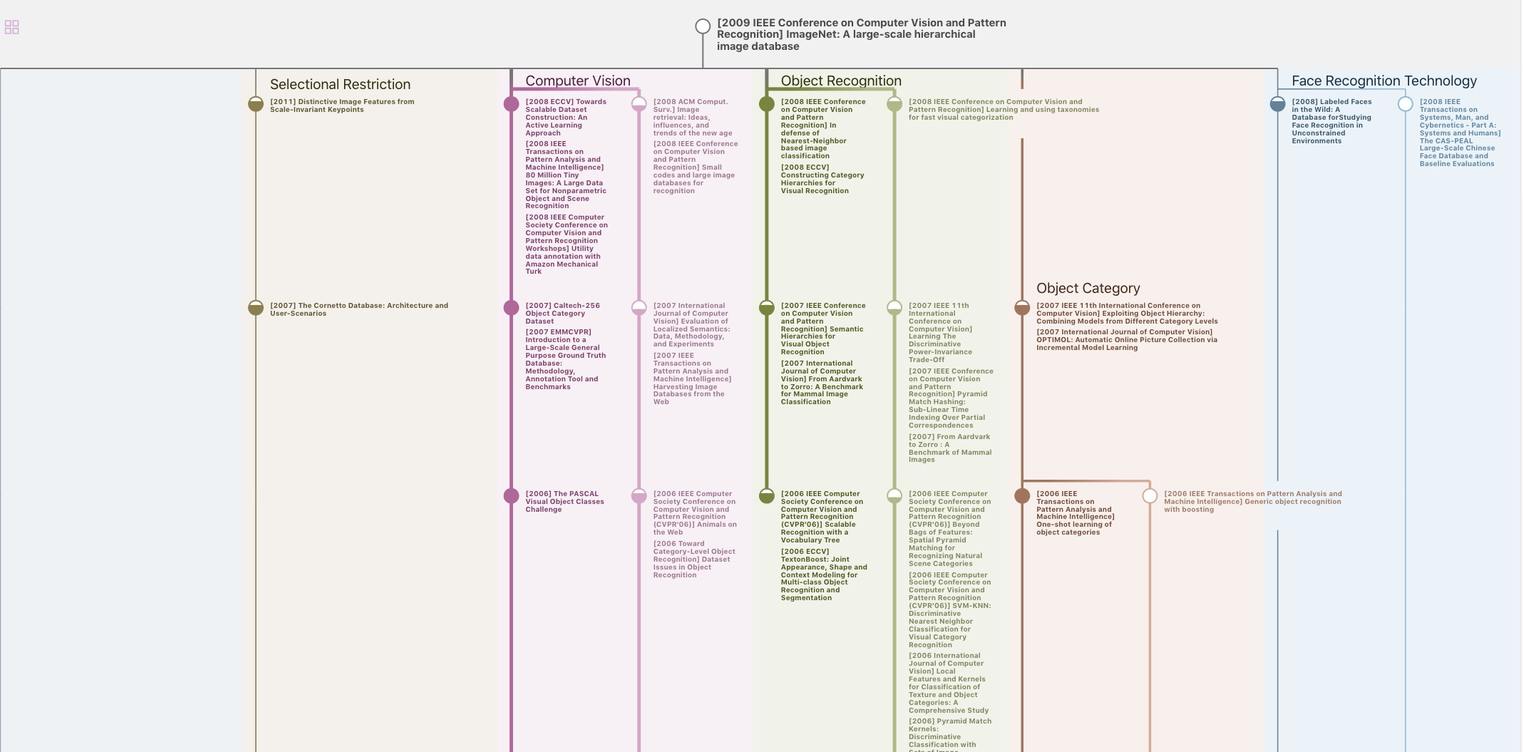
Generate MRT to find the research sequence of this paper
Chat Paper
Summary is being generated by the instructions you defined