Material model identification from set of experiments and validation by DIC
MATHEMATICS AND COMPUTERS IN SIMULATION(2021)
Abstract
A methodology for calibration and validation of material models using more simultaneous experiments is presented. The procedure contains the selection of suitable parameters for identification using a sensitivity analysis, parameters identification, analysis of usability of the material model, and validation of the material model. Three elastoplastic models are evaluated in this study: the bilinear isotropic hardening model with Von Mises yield condition, the bilinear isotropic hardening model with the Hill anisotropic yield condition, and the nonlinear isotropic hardening model with Hill anisotropic yield condition. Five proportional as well as nonproportional monotonic loading experiments conducted on aluminium alloy 2124-T851 are used for the presentation of the inverse approach application, whereas four of them are the source of identification. The validation of calibrated material models is done based on the strain field measurement realised by the Digital Image Correlation method. The nonlinear isotropic hardening rule together with Hill yield condition brings the best description of stress-strain behaviour of the material under investigation. (C) 2021 International Association for Mathematics and Computers in Simulation (IMACS). Published by ElsevierB.V. All rights reserved.
MoreTranslated text
Key words
Inverse identification,Finite Element Method,Experiments,Digital Image Correlation method,Sensitivity analysis
AI Read Science
Must-Reading Tree
Example
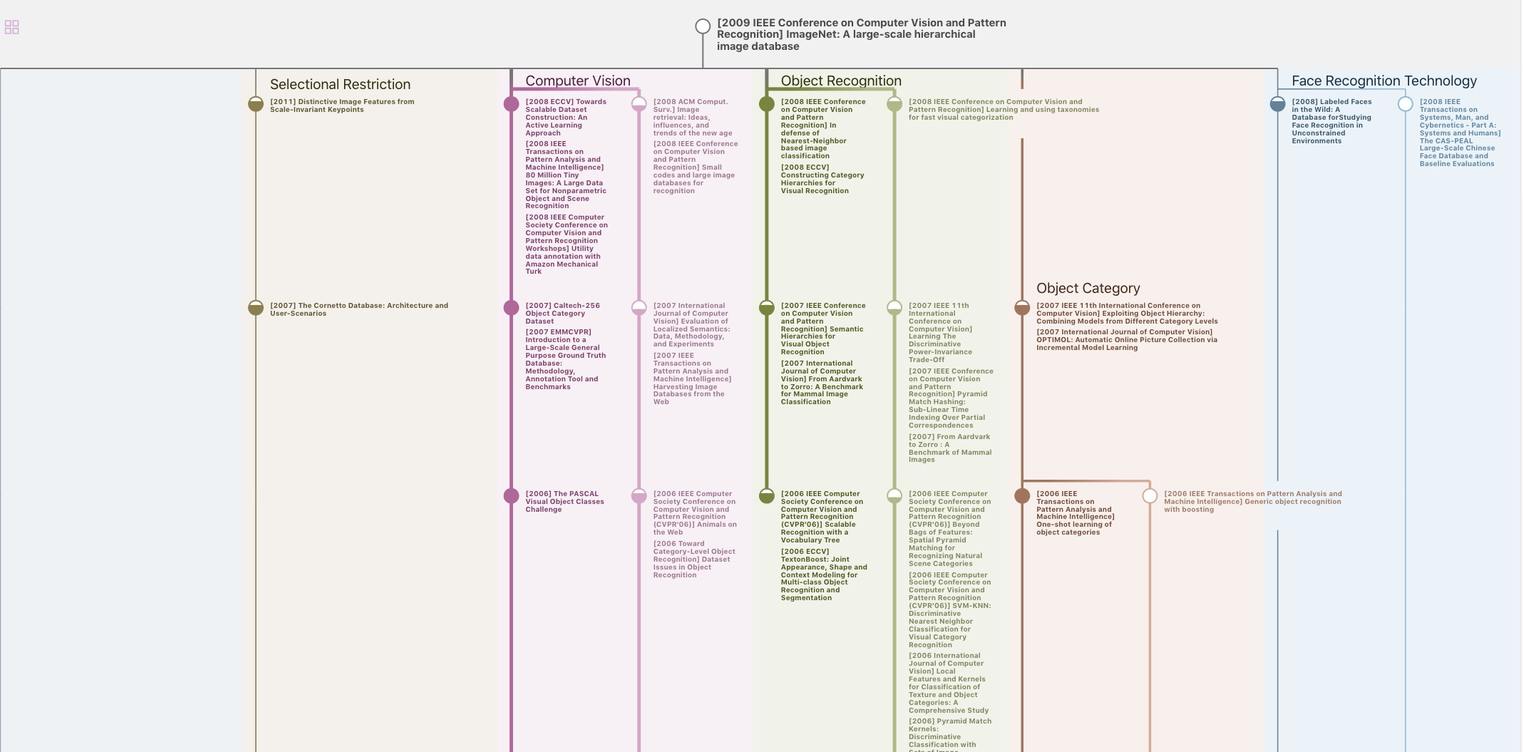
Generate MRT to find the research sequence of this paper
Chat Paper
Summary is being generated by the instructions you defined