Delamination and hole wall roughness evaluation in air-cooled drilling of carbon fiber-reinforced polymer
JOURNAL OF COMPOSITE MATERIALS(2021)
Abstract
Drilling of carbon fiber-reinforced polymer (CFRP) is widely employed in manufacturing processes in the aeronautical, automobile, and energy industries. The evaluation of the hole region focusing on wall roughness and delamination phenomena is extremely important to predict bolted joints' performance, where at least one of the adherent is a composite material. Thus, this work performed a statistical analysis on the delamination (entrance and exit of the plate) and wall roughness of drilling holes in an 8.6 mm thick CFRP plate carried out by an uncoated carbide drill under compressed air-cooling, varying the cutting speeds and feed rates. Since air-cooling usage combines positive aspects, such as low-cost implementation and shorter process time compared to ultrasonic-assisted drilling, it turns out to be an excellent alternative for aeronautical industry. Thus, the main contribution of the present work consists on analyzing the variation of the delamination in the entrance and exit of the first and tenth holes of a CFRP plate after dry and air-cooled drilling. This variation of the delamination between the cold drill (first hole) and the heated drill due to the drilling holes' sequence (after ten holes) is investigated for 18 different combinations of parameters (runs). For instance, it is shown that if the combination of parameters values is suitable, then it is possible to reduce the mean value of adjusted delamination factor for the entrance of the tenth hole around 11% when comparing cooled-air with dry cutting.
MoreTranslated text
Key words
CFRP drilling, compressed air-cooling, delamination, hole wall roughness
AI Read Science
Must-Reading Tree
Example
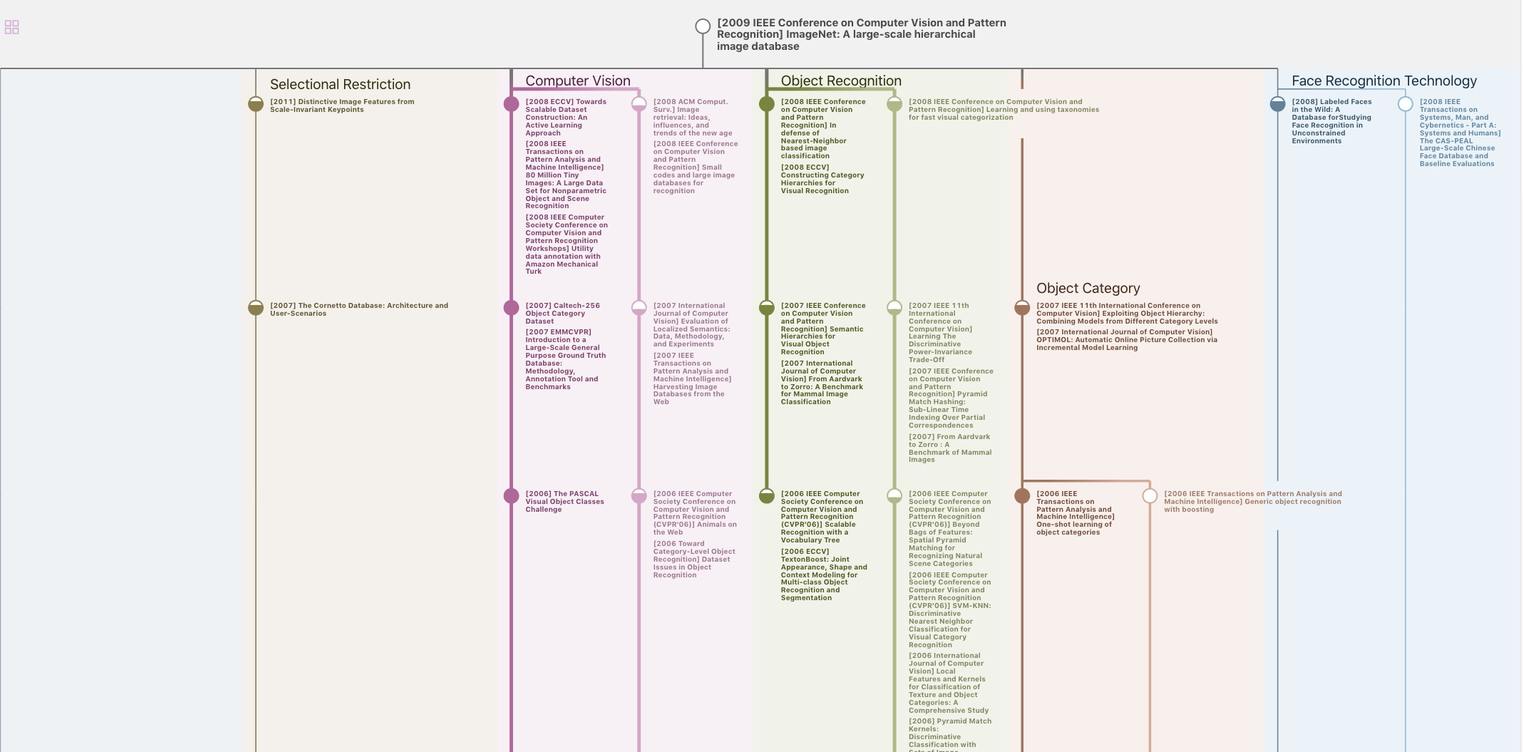
Generate MRT to find the research sequence of this paper
Chat Paper
Summary is being generated by the instructions you defined