Manufacturing a carbon/epoxy NACA 23018 airfoil skin using a circular braiding machine: experimental and numerical study
JOURNAL OF INDUSTRIAL TEXTILES(2022)
Abstract
In the interest of reducing the weight and also cost of blade skins, various automatic preform manufacturing processes were developed including tape laying, filament winding and braiding. Among them, the circular braiding process was found to be an efficient method in producing seamless preforms on mandrels with various geometries. In this regard, an attempt was made to produce a carbon fiber reinforced composite with the shape of NACA 23018 airfoil using a circular braiding machine. Thus, suitable wooden mandrels were manufactured using NACA 23018 airfoil coordinates, which were obtained by assuming the perimeter of 20 cm. Furthermore, both biaxially and triaxially braided preforms were produced and subsequently impregnated with epoxy resin through an appropriate fabrication method. To assess their performance, four-point bending test was carried out on samples. Ultimately, the elastic response of braided composite airfoils was predicted using a meso-scale finite element modeling and was validated with experimental results.
MoreTranslated text
Key words
Circular braiding machine, NACA 23018 airfoil, braided NACA 23018 composite, finite element modeling
AI Read Science
Must-Reading Tree
Example
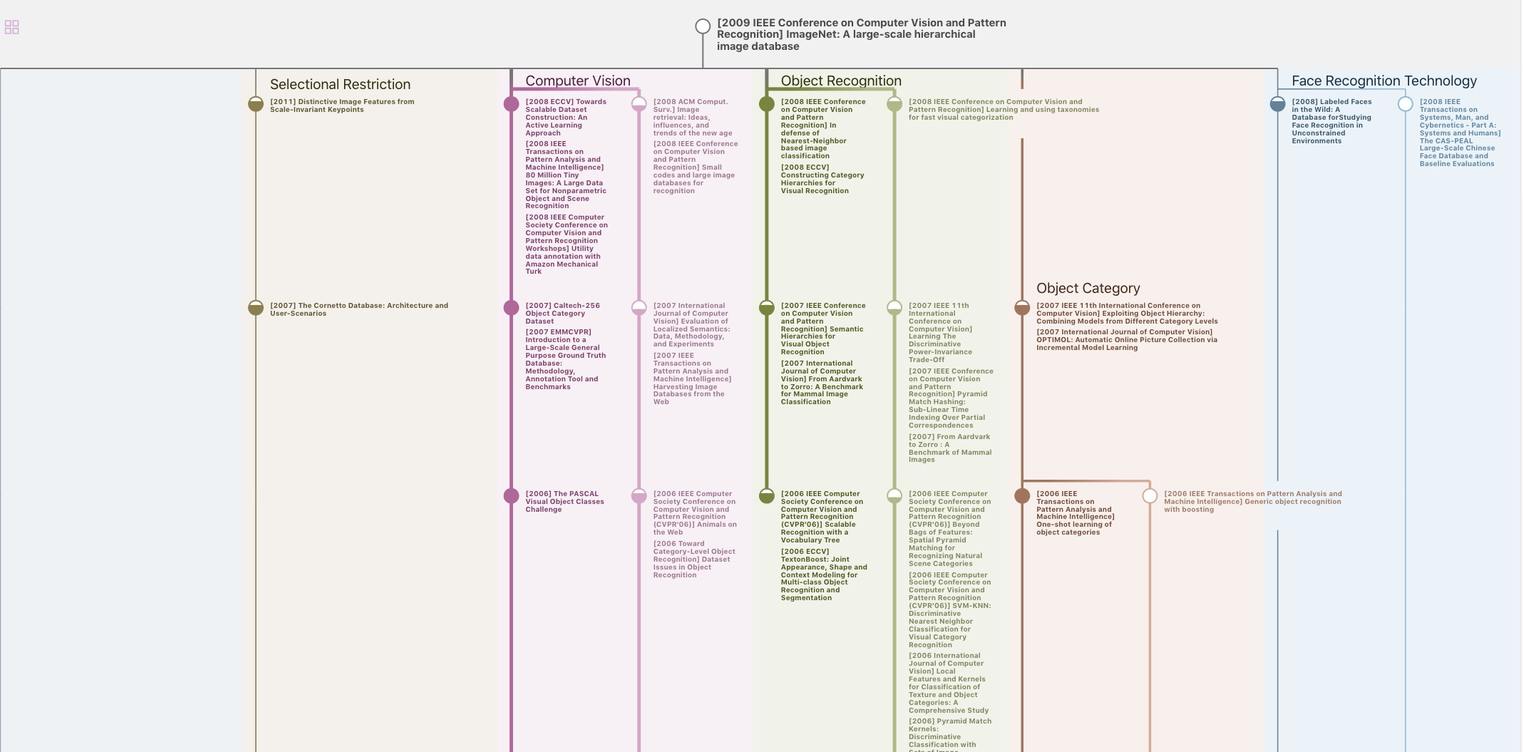
Generate MRT to find the research sequence of this paper
Chat Paper
Summary is being generated by the instructions you defined