Thermal Delamination Modelling And Evaluation Of Aluminium-Glass Fibre-Reinforced Polymer Hybrid
POLYMERS(2021)
摘要
This paper aims to propose a temperature-dependent cohesive model to predict the delamination of dissimilar metal-composite material hybrid under Mode-I and Mode-II delamination. Commercial nonlinear finite element (FE) code LS-DYNA was used to simulate the material and cohesive model of hybrid aluminium-glass fibre-reinforced polymer (GFRP) laminate. For an accurate representation of the Mode-I and Mode-II delamination between aluminium and GFRP laminates, cohesive zone modelling with bilinear traction separation law was implemented. Cohesive zone properties at different temperatures were obtained by applying trends of experimental results from double cantilever beam and end notched flexural tests. Results from experimental tests were compared with simulation results at 30, 70 and 110 degrees C to verify the validity of the model. Mode-I and Mode-II FE models compared to experimental tests show a good correlation of 5.73% and 7.26% discrepancy, respectively. Crack front stress distribution at 30 degrees C is characterised by a smooth gradual decrease in Mode-I stress from the centre to the edge of the specimen. At 70 degrees C, the entire crack front reaches the maximum Mode-I stress with the exception of much lower stress build-up at the specimen's edge. On the other hand, the Mode-II stress increases progressively from the centre to the edge at 30 degrees C. At 70 degrees C, uniform low stress is built up along the crack front with the exception of significantly higher stress concentrated only at the free edge. At 110 degrees C, the stress distribution for both modes transforms back to the similar profile, as observed in the 30 degrees C case.
更多查看译文
关键词
metal–, composite hybrid laminate, finite element analysis, temperature effect, cohesive zone modelling, Mode-I delamination, Mode-II delamination
AI 理解论文
溯源树
样例
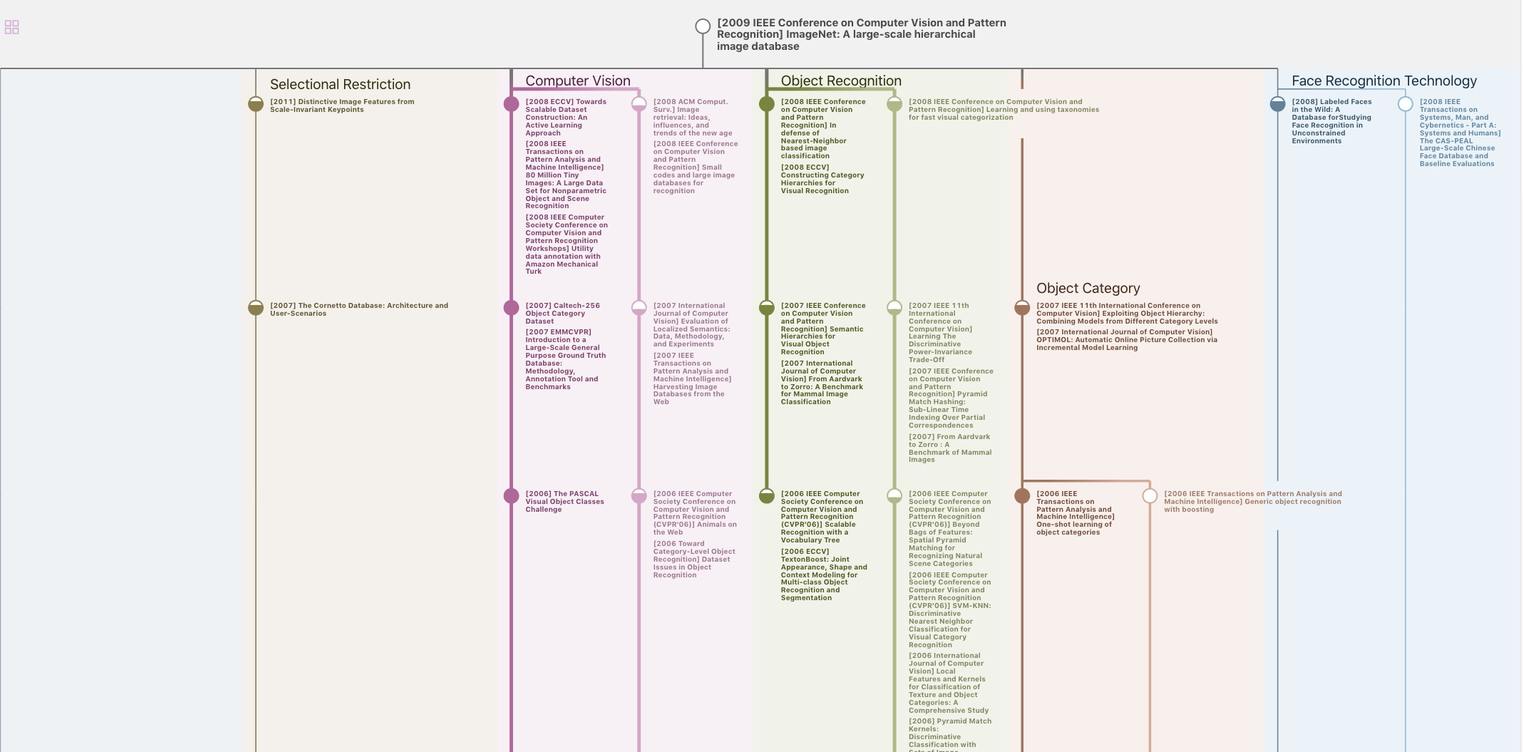
生成溯源树,研究论文发展脉络
Chat Paper
正在生成论文摘要