Determining Process-Window For Manufacturing Of Continuous Carbon Fiber-Reinforced Composite Using 3d-Printing
MATERIALS AND MANUFACTURING PROCESSES(2021)
Abstract
Continuous carbon-fiber-reinforced acrylonitrile butadiene styrene (ABS) has been manufactured by a method based on fused deposition modeling (FDM). Before 3D printing, the carbon fibers pass through an ABS-acetone bath to prepare solution impregnated fibers (prepregs). Continuous fiber-reinforced thermoplastic composites (CFRTCs) were printed by feeding carbon fiber prepregs and ABS filament, simultaneously into a special single port nozzle. By varying print conditions such as nozzle diameter, layer height, and print speed, composite specimens were printed with different qualities. The visual evaluation of printed composites was used to determine a process window for stable or unstable CFRTC printing. In the obtained process window, four regions were observed including fiber fuzzing or tearing instability, fiber twisting instability, low quality stable print and high quality stable print. The optimum condition to print CFRTCs was found and then specimens were printed to investigate mechanical properties under the optimal printing condition. The mechanical and morphological properties of visual-optimized 3D-printed composites, without any fiber fuzzing, tearing or twisting were investigated. The results showed that tensile, flexural, and interlaminar shear strength of 3D-printed ABS-carbon CFRTCs have increased 313%, 121%, and 54%, respectively, when compared with the neat ABS 3D-printed samples.
MoreTranslated text
Key words
3D printing, composite, reinforcement, continuous, fiber, solution, impregnation, process window, ABS, carbon
AI Read Science
Must-Reading Tree
Example
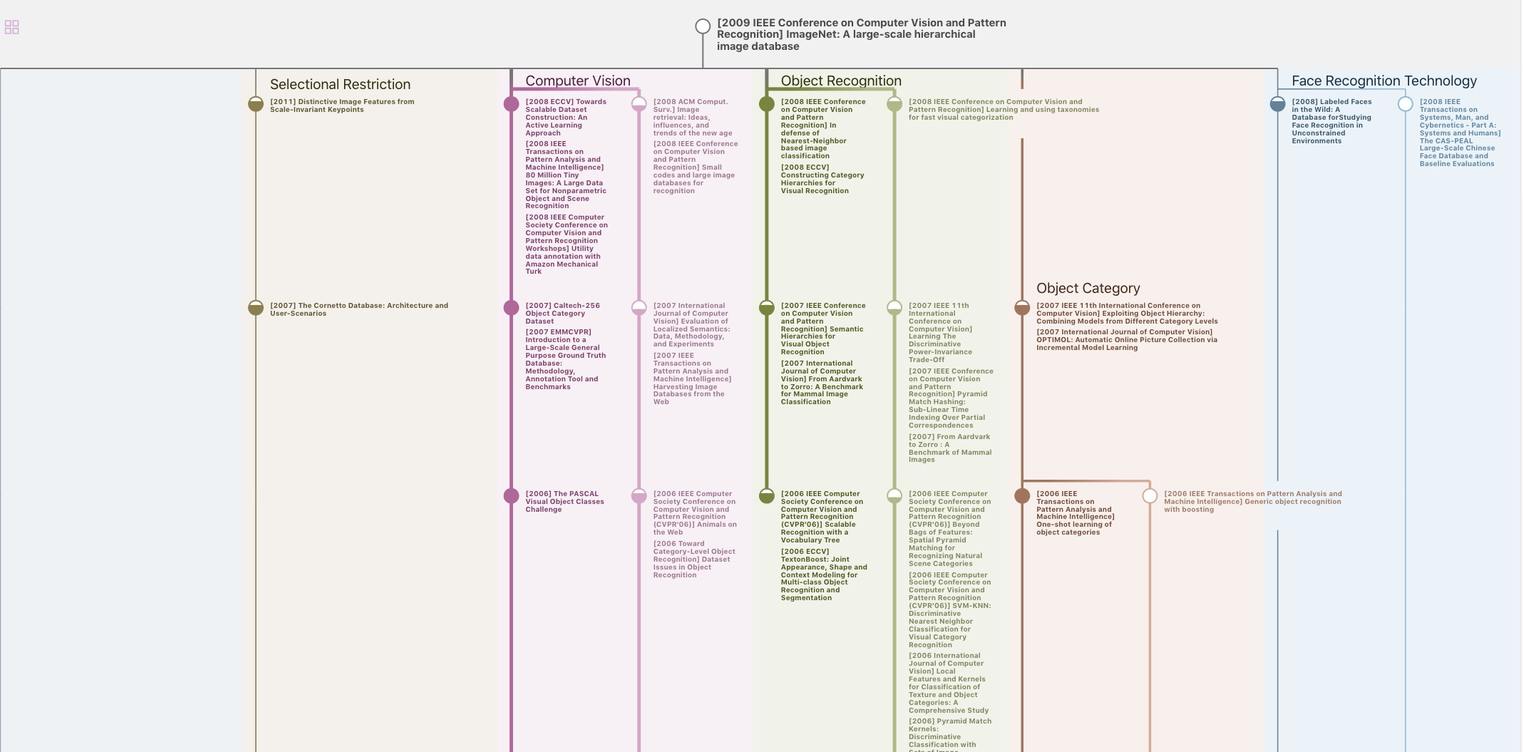
Generate MRT to find the research sequence of this paper
Chat Paper
Summary is being generated by the instructions you defined