ISO Stress Analysis and Micro Geometry Corrections of Parallel Axis Gearbox Using Dontyne Systems Gear Production Suite
International Journal of Engineering(2020)
摘要
This paper shows the design procedure of a parallel axis gearbox for an electric power steering system using Dontyne Gear Production Suite (GPS) software. It will also investigate the effect of microgeometry correction on contact stress values. Initially, the quantitative design procedure of gears geometry is implemented through an iterative selection process. This includes a proper selection of several geometrical parameters to match the design requirements. Then, ISO 6336, which is the most common analytical gear stress analysis approach, is applied for calculating surface contact and root bending stresses in involute gears. Applying a good macro geometry technique is desirable in order to optimize gear design. However, the increasing demand for reliable and compact gear pair requires specifying proper micro geometry corrections in order to ensure minimum peak stress, low noise, and vibration. Thus, the tooth profile is modified by applying for tip relief from the start to the end of active profiles taken into consideration the value of the mean mesh deflection and the profile error. Similarly, tooth flank is crowned to compensate for equivalent misalignment and to achieve a uniform load distribution over the gear face width. The amount of crowning is determined by adding shaft deflection error to manufacturing error and torsional deflection. The results suggest that there is a significant improvement in contact stress value after applying tip relief and helix crowning.
更多查看译文
关键词
Gear Dynamics
AI 理解论文
溯源树
样例
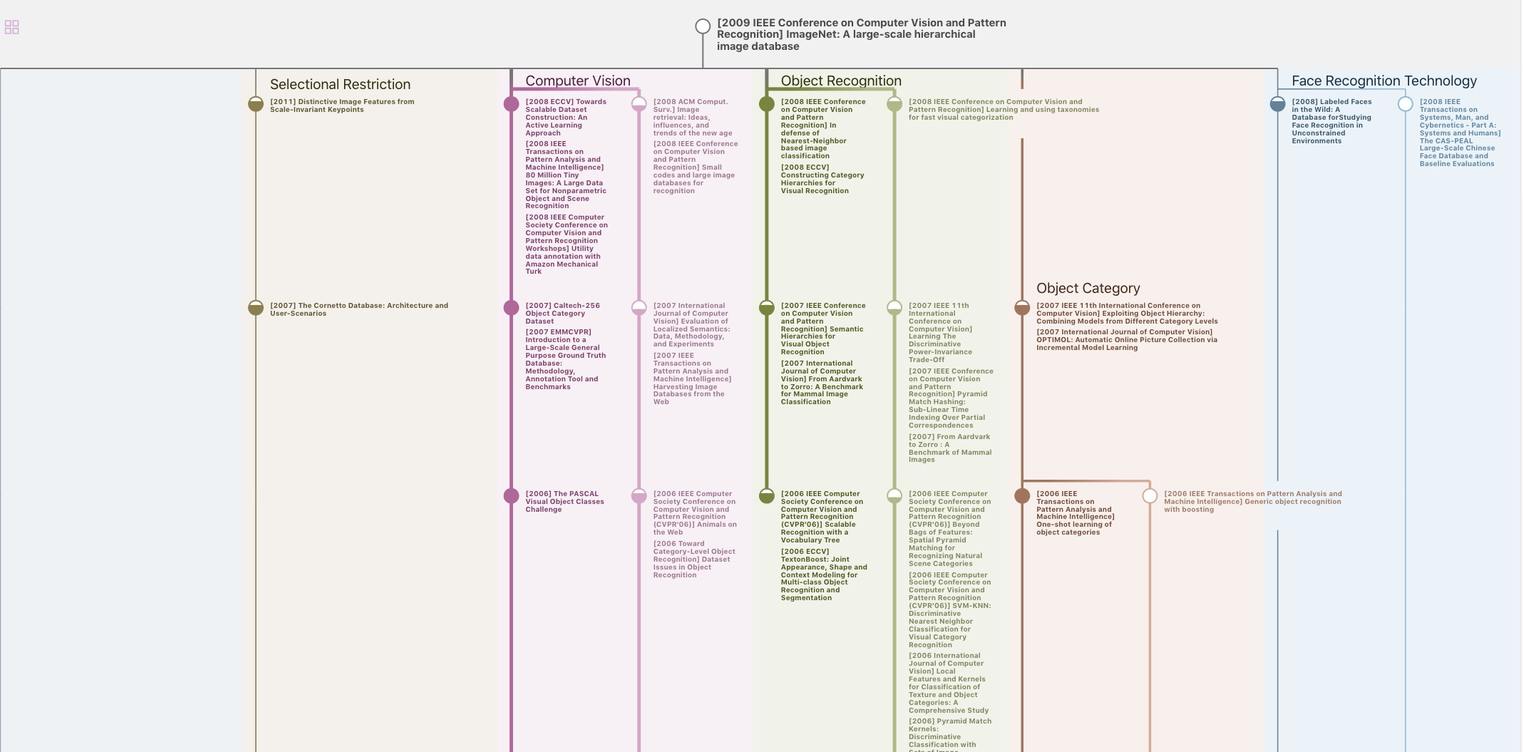
生成溯源树,研究论文发展脉络
Chat Paper
正在生成论文摘要