NUMERICAL SIMULATION AND EXPERIMENT OF THE FIRE PROTECTING SYSTEM OF THE MANIPULATOR IN HIGH TEMPERATURE ENVIRONMENT
ASME JSME KSME Joint Fluids Engineering Conference Proceedings(2019)
摘要
In the present work, the strategy for cooling the manipulator in high temperature environment is studied using both numerical and experimental methods. Since the manipulator is designed to operate in the environment with the maximum 250 degrees C temperature, fire protection system and the cooling system should be installed for normal operation of the manipulator. The para-aramid-filament with the thickness of 0.5 mm and Graphite felt with the thickness of 5.5 mm is considered for fire protection suit and air blowing technique is applied for cooling the electronic circuit and hydraulic pressure cylinders. For numerical simulation, ANSYS Fluent V18.2 is adopted to simulate the convective heat transfer flows and the radiation with the model, S2S (Surface to surface). Two types of blowing techniques are considered, global blowing and local one. Even though the global blowing at the inlet is most effective for cooling system, so much amount of compressed air is required, which means that extra big compression system should be added in the system. The local blowing is applied to the component with small holes of the flexible pipe and the magnitude of the local blowing mass flow rate is 0.0166kg/s. The technique of local blowing is more effective than the global blowing for cooling the system. To validate numerical simulation, the model is tested within the hot temperature chamber whose mean temperature is approximately 250 degrees C.
更多查看译文
关键词
Computational Fluid Dynamics (CFD),Reynolds Averaged Navier-Stockes (RANS),Conjugate heat transfer,Manipulator,Air-cooled system,High temperature chamber
AI 理解论文
溯源树
样例
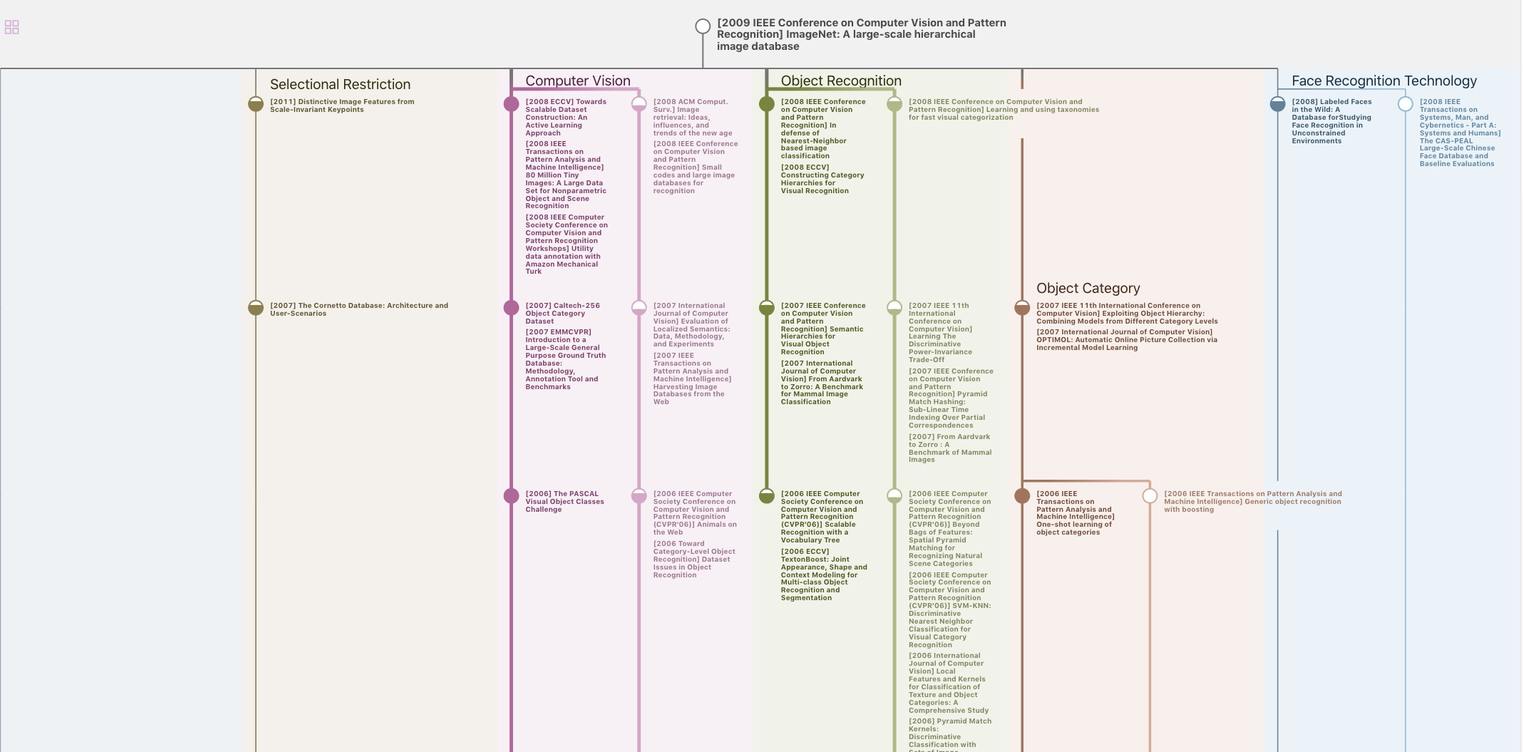
生成溯源树,研究论文发展脉络
Chat Paper
正在生成论文摘要