BENCHMARKING CCPP DESIGNS EMPLOYING 9-12%CR CSEF STEELS IN STEAM OXIDATION PRONE ENVIRONMENTS
JOINT EPRI - 123HIMAT INTERNATIONAL CONFERENCE ON ADVANCES IN HIGH-TEMPERATURE MATERIALS, 2019(2019)
摘要
To maintain their competitiveness in today's continuously changing energy market, conventional thermal power plants need to strive for higher efficiency and flexible operation whilst decreasing greenhouse gas emissions, This trend sets new challenges to material industries to offer solutions allowing the power plants to operate in a market with increasing competition. Materials employed in power plant are nowadays exposed to both severe conditions and cycling load. Today's dispatchable plants reach lower capacity factors due to a load following operation or due to the fluctuating availability of renewable sources in the electrical grid. The quest for higher efficiency leads to the need of employing steels with a high steam oxidation resistance, while ferritic steels are favored under cycling operation thanks to limited thermal expansion compared to austenitic stainless steel. 9% Cr Creep Strength Enhanced Ferritic (CSEF) steels are limited in temperature mainly due to capping their steam oxidation resistance capabilities at levels required by the drive for efficiency increase. For heat-exchangers manufactured from conventional materials, the formation, growth and spallation of oxide scale on the steam side may eventually impair plant operations and damage other downstream components. This work presents a case study collaboratively performed together with the Department of Energy of Politecnico di Milano (Italy). A combined cycle power plant consisting of the GE 9HA0.2 GT has been modelled based on first principles, considering as a collection of interconnected equipment. The Heat Recovery Heat generator (HRSG) design features three pressure levels, including a once-through boiler for the highest pressure level. A comparative analysis of this plant has been performed by considering three different maximum live steam temperatures (585 degrees C, 605 degrees C, 620 degrees C) and four different alloys, the standard ferritic grades 91 and 92; stainless S304H; and the new Tenaris solution Thor (TM) 115 (Tenaris High Oxidation Resistance), for the heat-exchangers severely exposed to steam oxidation, i.e. the final superheater (SH) and reheater (RH) sections. The study highlights that the Tenaris solution, the CSEF steel grade Thor (TM) 115, with its improved steam oxidation resistance, offers an alternative to stainless steel solutions for live steam temperatures above 600 degrees C. The use of conventional 9%Cr CSEF steel grades at live steam temperatures above 600 degrees C is generally impeded due to an accelerated corrosion. The improved steam oxidation resistance of Thor (TM) 115 consequently leads to negligible corrosion allowances, resulting in marginal overall weight increase of the HRSG for the same rated power output compared to stainless solutions, while still offering the manufacturing advantages of ferritic grades. Moreover modern CSEF steels are more recommended than stainless steel solutions for power plants operated at lower capacity factors, due to their superior thermophysical properties compared thus limiting the thermal fatigue; as these plants need to cope with fast and frequent load change. Considering the efficiency boost linked to the live steam temperature increase of the power plant it considerably contributes to CO2 savings for the same nominal power output.
更多查看译文
AI 理解论文
溯源树
样例
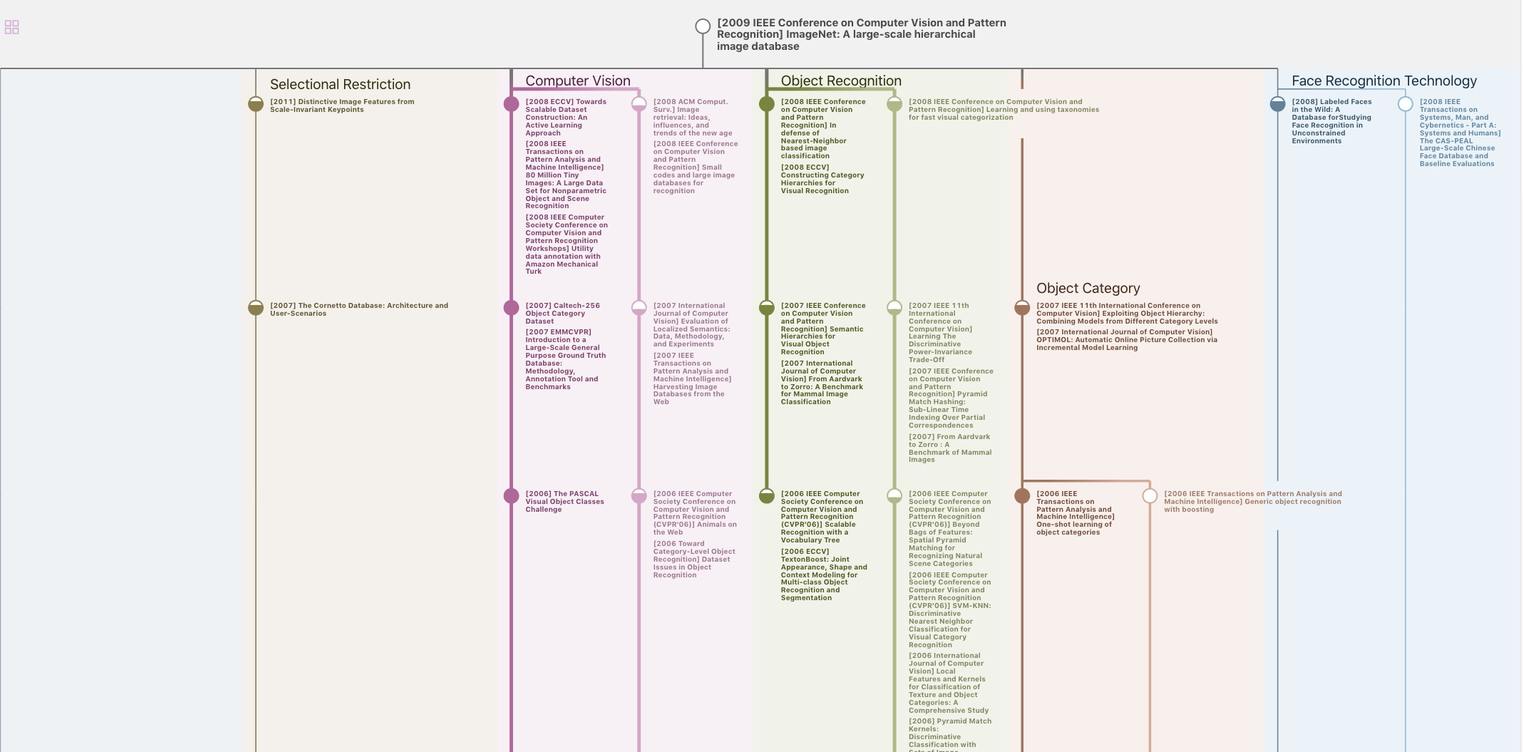
生成溯源树,研究论文发展脉络
Chat Paper
正在生成论文摘要