Using 2D/3D FEM Simulation to Determine Drawing Force in Cold Drawing of Steel Tubes with Straight Internal Rifling
Solid State Phenomena(2020)
Abstract
The most comprehensive steel tube portfolio is used to produce all kinds of modern energy production and the corresponding auxiliary unit such as boilers and heat exchangers. Multi-rifled seamless steel tubes are distinguished by maximum pressure, heat resistance, strength and durability. Production of multi-rifled seamless steel tubes by cold draw process using multi-rifled mandrel is quite a new technology. Shape and dimension of the drawing tool depend on drawing tube reduction degree, i. e. on the original diameter of the initial tube and final diameter of the tube. The technology of drawing tubes is influenced by process parameters, dimensions of tools and cold forming process conditions. Optimization of the whole forming process naturally involve the FEM analyses and simulation. One of the most important information of the cold drawing process is the load stroke of the tools. The contribution is concerned at the usability of FEM simulation on an evaluation of cold draw forming process condition and prediction of load stroke of the forming tools. DEFORM 2D/3D FEM software is used to compare the result of the drawing force and to determine the appropriate methodology to set FEM simulation of cold forming.
MoreTranslated text
Key words
Sheet Metal Forming,TRIP/TWIP Steels
AI Read Science
Must-Reading Tree
Example
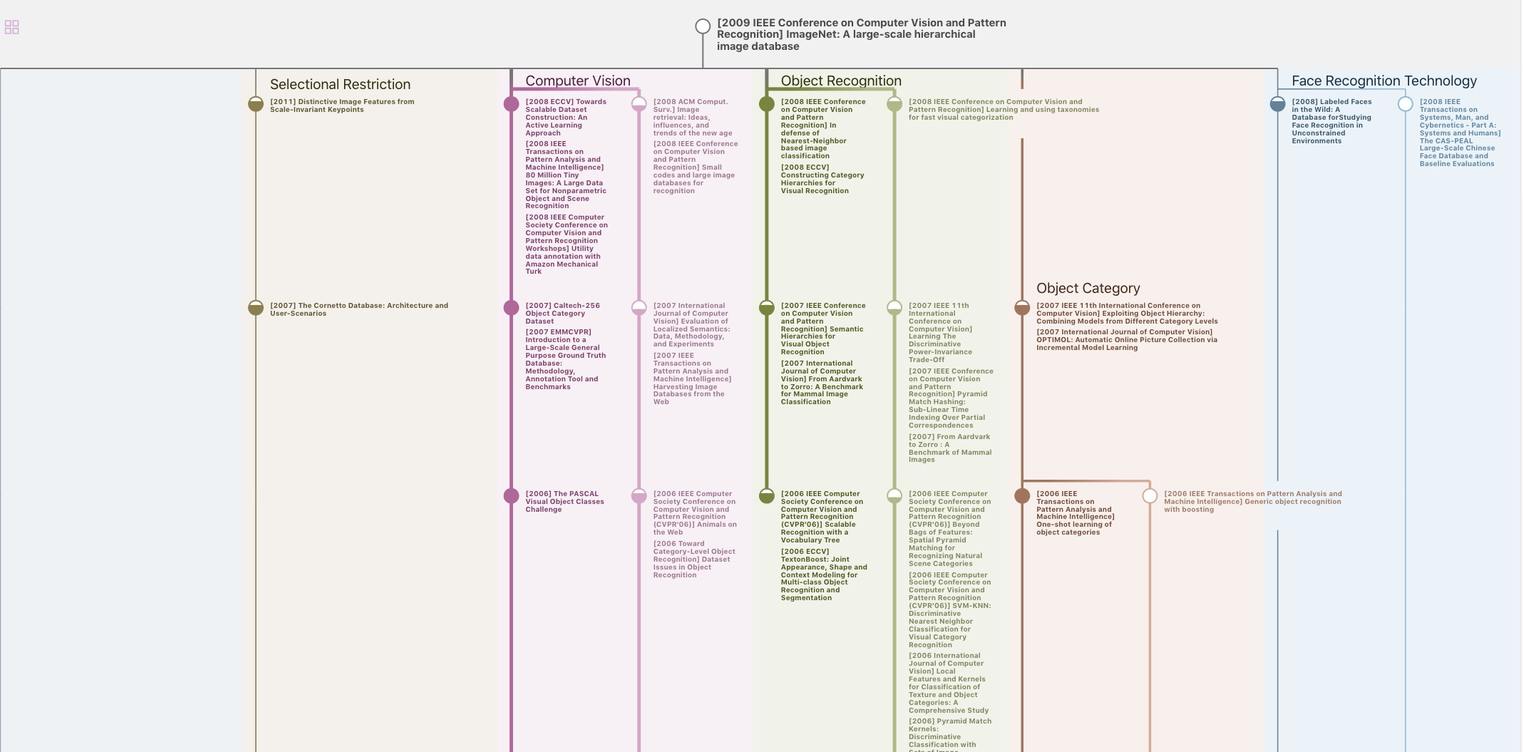
Generate MRT to find the research sequence of this paper
Chat Paper
Summary is being generated by the instructions you defined