Changes In Emissivity Of The Electrodes For Resistence Spot Welding Due To Their Wear
28TH INTERNATIONAL CONFERENCE ON METALLURGY AND MATERIALS (METAL 2019)(2019)
Abstract
Resistance spot welding is one of the most used welding technologies for joining of thin, deep drawn steel sheets in automotive industry. The condition of electrodes may have significant impact on the resulting weld quality, therefore it is necessary to check the electrodes' wear that otherwise may cause creation of specific defects in the weld joints. One of the possibilities is utilization of infrared thermography. In order to perform the testing correctly it is essential to know the expected emissivity of the electrodes. This article deals with the changes in emissivity due to wear. It demonstrates that the emissivity of new electrodes is significantly different in comparison with worn electrodes. The biggest change is observed between the first and 25th weld. With increasing number of performed welds the emissivity drops slightly with increasing number of welds. The increased temperature caused significant drops when temperature is elevated up to 40 degrees C, but it is virtually constant for temperatures above 40 degrees C. It concludes that a mean,operational emisivity of the electrodes operated at higher temperatures (i.e. 40 degrees C +) is a suitably accurate factor to be used during the weld inspection on defects.
MoreTranslated text
Key words
Automotive, resistance spot welding, thermography, ultrasonic testing
AI Read Science
Must-Reading Tree
Example
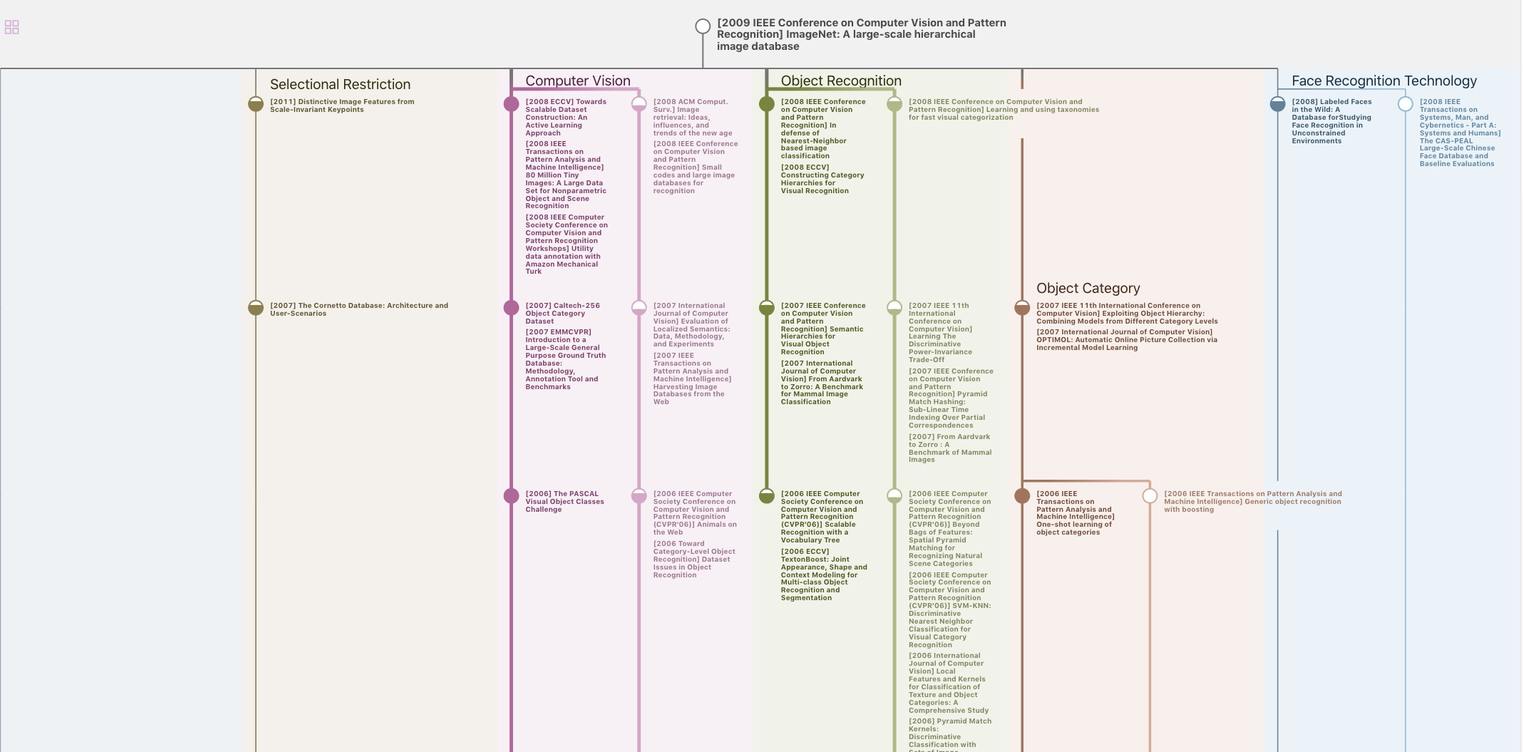
Generate MRT to find the research sequence of this paper
Chat Paper
Summary is being generated by the instructions you defined