A self-adaption normal direction and active variable stiffness low-frequency vibration-assisted system for curved surface drilling
Precision Engineering(2020)
摘要
The drilling operation occupies an important position in the aircraft assembly workload, and it accounts for a large proportion of the assembly cost. Previous reports show that drilling quality affects aircraft safety factor such as the probability of fatigue failure accidents. This paper proposes an automatic machining system for curved surface drilling. In this scheme, the self-adaption normal direction is realized by using the secondary positioning strategy (primary positioning and precise positioning). An elastic structure and the key positions smooth processing are applied to enhance the positioning guidance. The active variable stiffness mechanism satisfies the different requirements for system stiffness during the positioning stage and the drilling stage. Expansion sleeve locking and state switching of drilling assistance pneumatic cylinder lead to changes in the actuator's DOF and external forces, thereby achieving active control of the stiffness. Vibration-assisted machining technology is introduced to improve drilling quality. Compared with conventional drilling, the results show that this drilling system produces thin and slender chips, smaller burrs, and better internal surface quality.
更多查看译文
关键词
Self-adaption normal direction,Curved surface drilling,Low-frequency,Vibration-assisted drilling
AI 理解论文
溯源树
样例
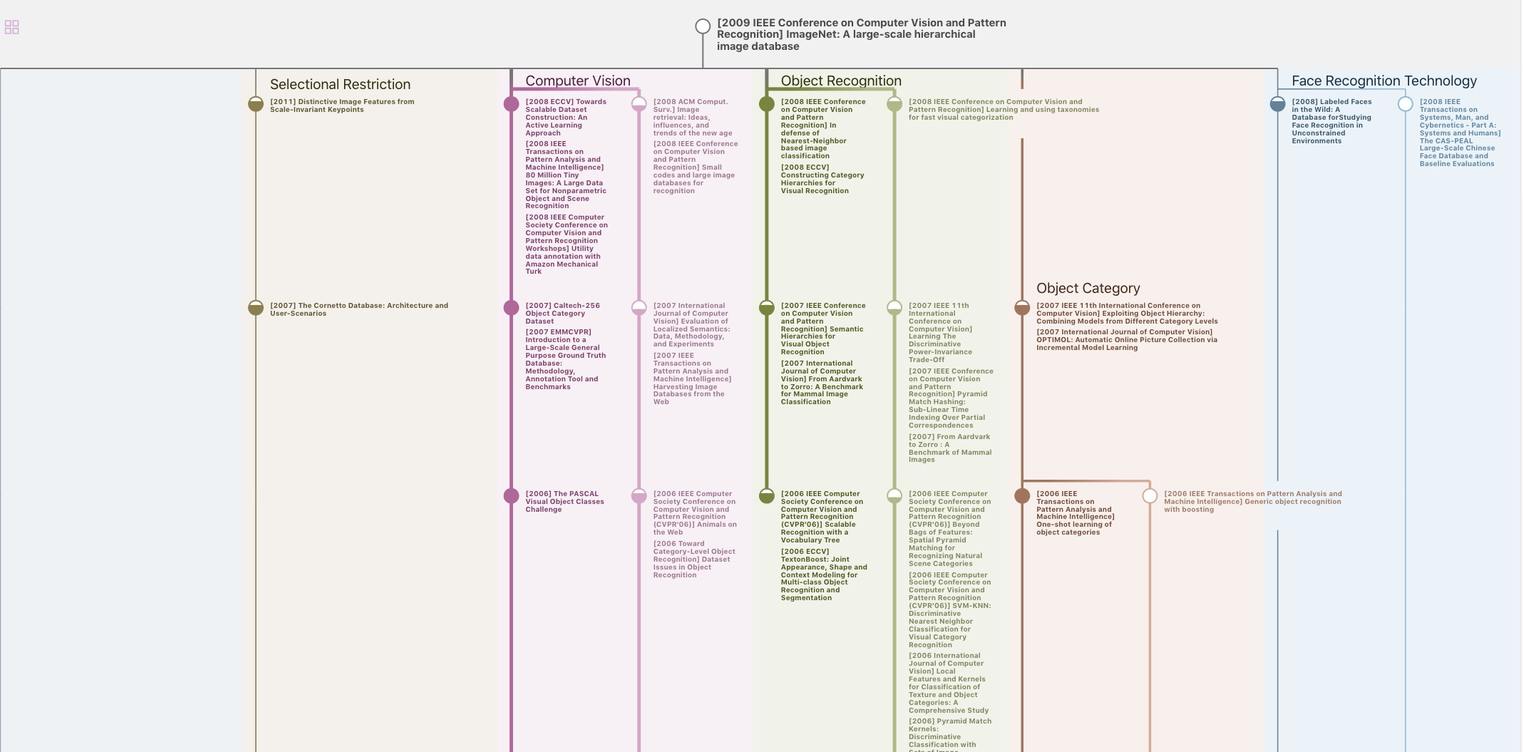
生成溯源树,研究论文发展脉络
Chat Paper
正在生成论文摘要