Advances in additive manufacturing process simulation: Residual stresses and distortion predictions in complex metallic components
Materials & Design(2020)
摘要
Due to rapid solidification of melted powders in metal additive manufacturing processes and high thermal gradients, large residual stresses are created in the build. This can lead to undesired distortions as well as crack initiation. The main aim of this work is to optimize the Additive Manufacturing (AM) process parameters by finite element modelling of the entire process to minimize the resulting residual stresses and distortions. We focus on two most important metal AM processes: (a) Laser Direct Energy Deposition (LDED) and (b) Selective Laser Melting (SLM). The ABAQUS AM module is employed to simulate both processes as it provides an automated interface allowing the user to define event data, such as element activation and heat input, as a function of both position and time to achieve process simulation of complex 3D parts. For the LDED processes, thin wall components are simulated, and residual stresses predictions are compared with both FIB-DIC and XRD measurement results at different scales. For the SLM process, overhanging structures with different support thicknesses are simulated and compared with experimental part distortion after support removal. It is shown that the support thickness together with selected process and material properties play a key role in resulting distortions.
更多查看译文
关键词
Additive manufacturing (AM),Laser Direct Energy Deposition (LDED),Selective Laser Melting (SLM),Finite element analysis (FEA),Residual stresses (RS),Geometric distortion
AI 理解论文
溯源树
样例
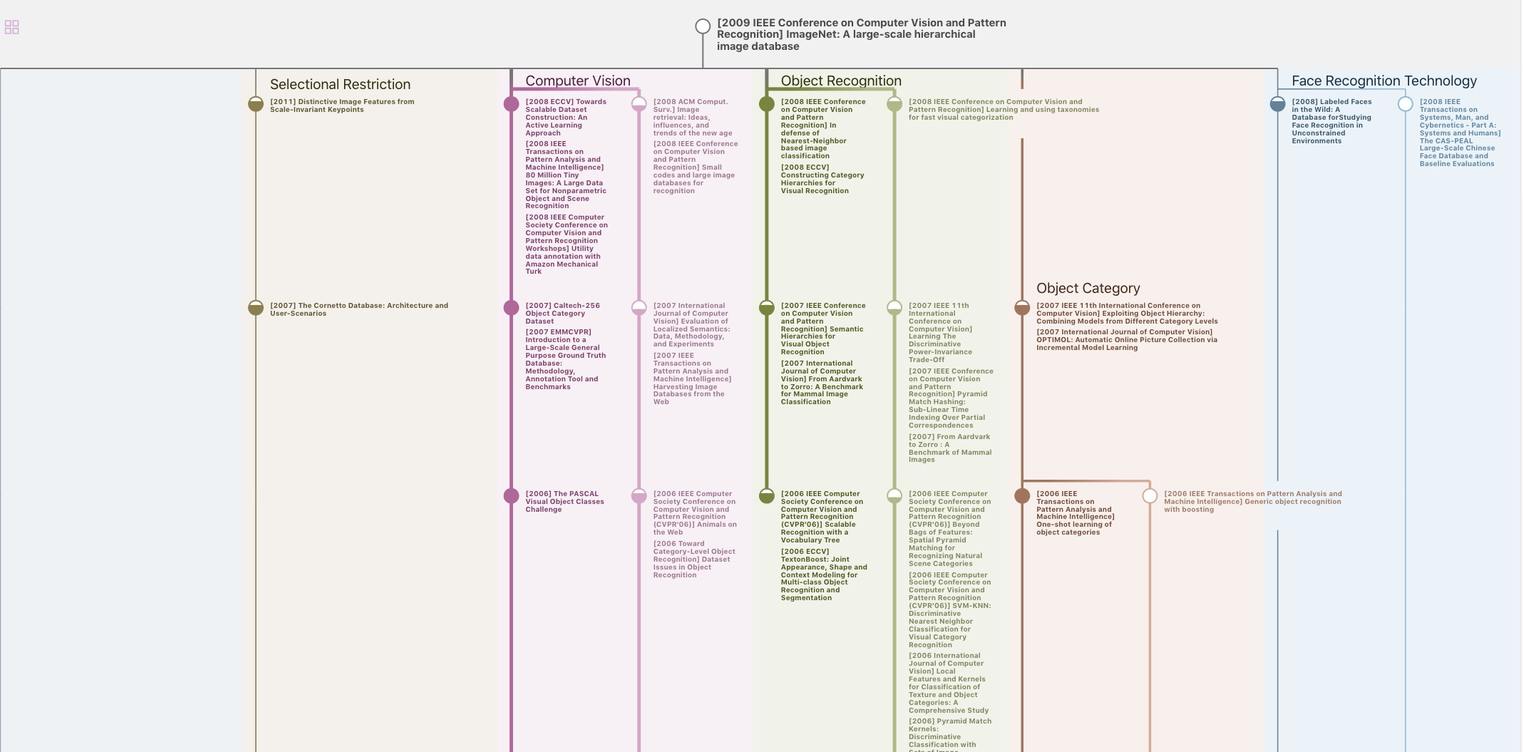
生成溯源树,研究论文发展脉络
Chat Paper
正在生成论文摘要