Wear of potential tool materials for aluminium alloys friction stir welding at weld temperatures
PROCEEDINGS OF THE ESTONIAN ACADEMY OF SCIENCES(2019)
摘要
Friction stir welding is a solid-state joining process that uses a non-consumable tool to join materials by mixing them mechanically in the weld area instead of melting them. The high-quality friction stir welding (FSW) process temperatures are in the range of 400-500 degrees C. Adhesive wear is suggested to be the main wear mechanism for the FSW tool. Adhesive wear testing should be performed at the weld temperature or close to the welding process temperatures for better simulation of real-life FSW tool wearing conditions. Adhesive wear tests of three FSW tool materials, WC-Co and TiC based with NiMo and FeCr binders at temperatures of 70 degrees C (low) and 400 degrees C (high) were performed by turning aluminium alloy AW6082-T6. The higher temperature in the cutting zone was achieved by increasing the cutting speed. To measure the temperature at the interface of the cutting tool and the workpiece, a novel method based on the thermoelectric effect was used. The wear was determined as the change of the geometry of the cutting edges of the tool. Microscopic investigations were performed by using scanning electron microscopy. The distribution of chemical elements and the chemical composition of the tool cutting edge were analysed by energy dispersive X-ray spectroscopy. The TiC-based cermets (TiC-NiMo and TiC-FeCr) demonstrated superiority over WC-Co cemented carbide at both low (70 degrees C) and high (400 degrees C) temperatures. The highest wear performance at the low temperature was shown by the Fe-alloy bonded composite TiC-FeCr while at the high temperature the Ni-alloy bonded cermet TiC-NiMo had the highest wear performance.
更多查看译文
关键词
friction stir welding,cermet,cemented carbide,adhesive wear,weld temperature
AI 理解论文
溯源树
样例
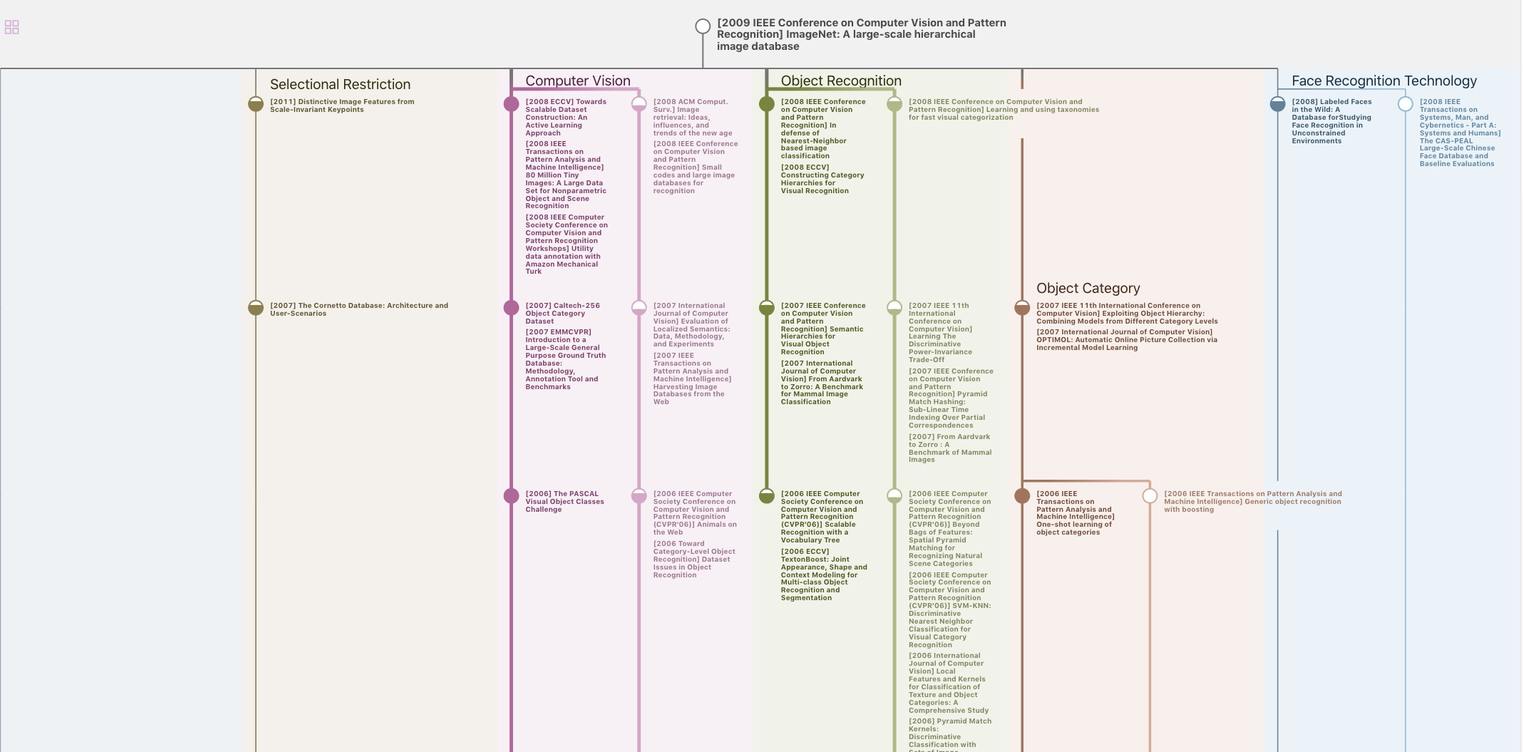
生成溯源树,研究论文发展脉络
Chat Paper
正在生成论文摘要