Study on the hot extrusion forming process of the cylindrical shell of automobile hydraulic shock absorber
ADVANCED MATERIALS AND ENERGY SUSTAINABILITY(2017)
Abstract
In order to solve the complex problems of manufacturing process of automobile hydraulic shock absorber shell, the technology of hot extrusion was presented. Based on the rigidplastic finite element analysis method, numerical simulation of extrusion process of AZ31 agnesium alloy cylindrical shell was carried out by by using the Deform-3D finite element simulation software. The stroke - load curve in extrusion process and the distribution of velocity field of flow metal were analyzed. The influence of different process parameters on the extrusion force and specimen quality were analyzed also. The results show that there are four stages in the process of extrusion deformation, including heading-deformation stage, lug blank forming stage, composite extrusion stage and the final forming stage. When the initial temperature of the blank is set to 350 degrees C, the die preheating temperature is set to 280 degrees C, and the working speed of the male die is controlled in the range of 6 similar to 12 mm/s, the load platform is stable, the forming quality of the cylinder shell is higher. And the feasibility of the technology is verified by experimental method. The study provides a theoretical basis for the optimization of die design and making reasonable hot extrusion process parameters.
MoreTranslated text
Key words
Hot extrusion forming,rigid-plastic finite element,AZ31 magnesium alloy,velocity field
AI Read Science
Must-Reading Tree
Example
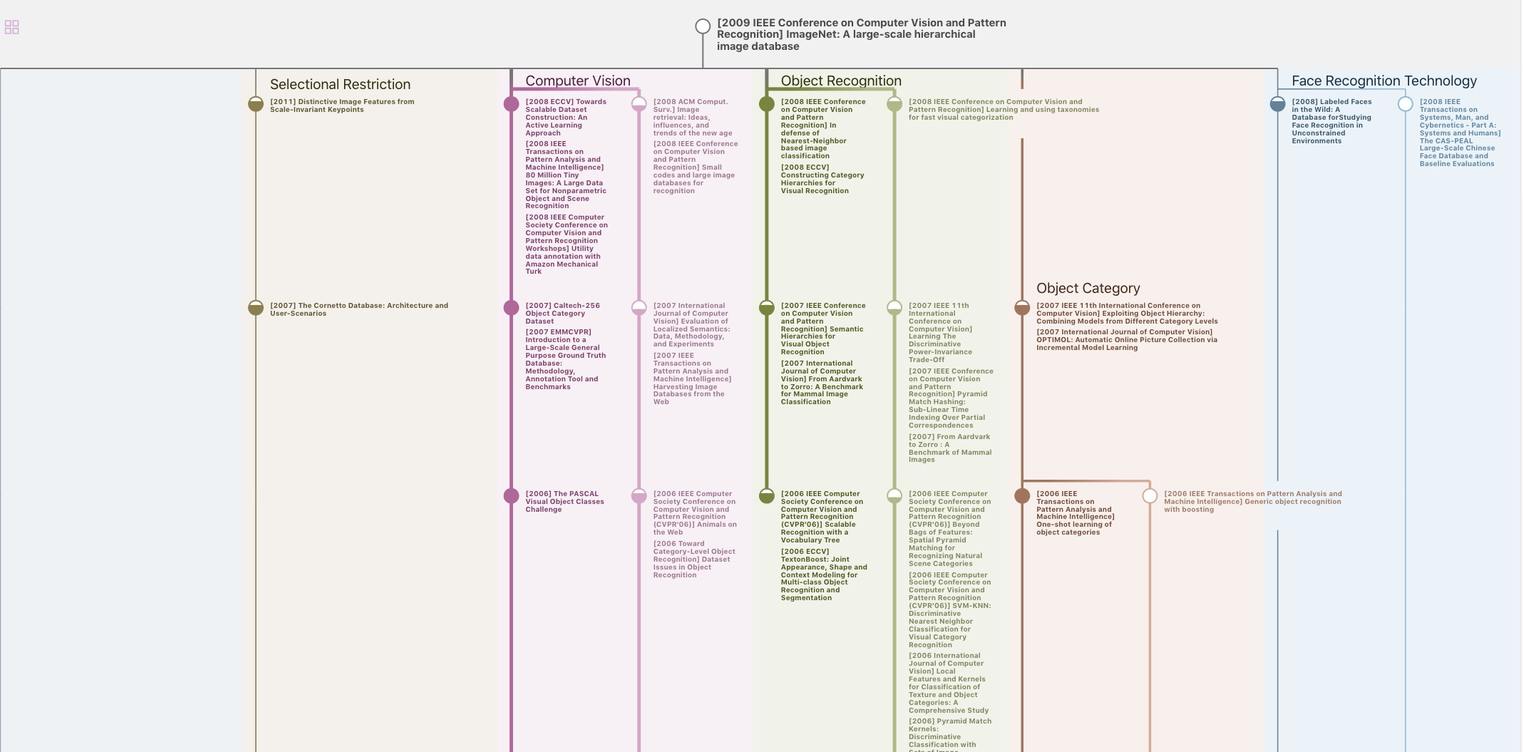
Generate MRT to find the research sequence of this paper
Chat Paper
Summary is being generated by the instructions you defined